धातु के लिए प्लास्टिक कोटिंग
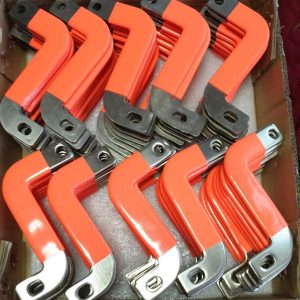
धातु प्रक्रिया के लिए प्लास्टिक कोटिंग में धातु के हिस्सों की सतह पर प्लास्टिक की एक परत लगाई जाती है, जो उन्हें धातु की मूल विशेषताओं को बनाए रखने की अनुमति देती है, साथ ही प्लास्टिक के कुछ गुण भी प्रदान करती है, जैसे संक्षारण प्रतिरोध, पहनने के प्रतिरोध, विद्युत इन्सुलेशन और स्वयं। -स्नेहन. उत्पादों की अनुप्रयोग सीमा का विस्तार करने और उनके आर्थिक मूल्य को बढ़ाने में यह प्रक्रिया बहुत महत्वपूर्ण है।
धातु के लिए प्लास्टिक कोटिंग की विधियाँ
प्लास्टिक कोटिंग के लिए कई तरीके हैं, जिनमें फ्लेम स्प्रेइंग भी शामिल है। द्रविकृत बिस्तर छिड़काव, पाउडर इलेक्ट्रोस्टैटिक छिड़काव, गर्म पिघल कोटिंग, और निलंबन कोटिंग। ऐसे कई प्रकार के प्लास्टिक भी हैं जिनका उपयोग कोटिंग के लिए किया जा सकता है PVC, पीई और पीए का सबसे अधिक उपयोग किया जा रहा है। कोटिंग के लिए इस्तेमाल किया जाने वाला प्लास्टिक पाउडर के रूप में होना चाहिए, जिसकी सुंदरता 80-120 मेश हो।
कोटिंग के बाद, वर्कपीस को ठंडे पानी में डुबो कर जल्दी से ठंडा करना सबसे अच्छा है। तेजी से ठंडा करने से प्लास्टिक कोटिंग की क्रिस्टलीयता कम हो सकती है, पानी की मात्रा बढ़ सकती है, कोटिंग की कठोरता और सतह की चमक में सुधार हो सकता है, आसंजन बढ़ सकता है और आंतरिक तनाव के कारण होने वाली कोटिंग टुकड़ी पर काबू पाया जा सकता है।
कोटिंग और बेस मेटल के बीच आसंजन को बेहतर बनाने के लिए, वर्कपीस की सतह धूल रहित और सूखी होनी चाहिए, कोटिंग से पहले जंग और ग्रीस के बिना। ज्यादातर मामलों में, वर्कपीस को सतह के उपचार से गुजरना पड़ता है। उपचार के तरीकों में सैंडब्लास्टिंग, रासायनिक उपचार और अन्य यांत्रिक तरीके शामिल हैं। उनमें से, सैंडब्लास्टिंग का प्रभाव बेहतर होता है क्योंकि यह वर्कपीस की सतह को खुरदरा कर देता है, सतह क्षेत्र को बढ़ाता है और हुक बनाता है, जिससे आसंजन में सुधार होता है। सैंडब्लास्टिंग के बाद, धूल हटाने के लिए वर्कपीस की सतह को साफ संपीड़ित हवा से उड़ाया जाना चाहिए, और प्लास्टिक को 6 घंटे के भीतर लेपित किया जाना चाहिए, अन्यथा, सतह ऑक्सीकरण हो जाएगी, जिससे कोटिंग का आसंजन प्रभावित होगा।
फायदा
पाउडरयुक्त प्लास्टिक की सीधी कोटिंग के निम्नलिखित फायदे हैं:
- इसका उपयोग उन रेजिन के साथ किया जा सकता है जो केवल पाउडर के रूप में उपलब्ध हैं।
- एक ही प्रयोग में मोटी कोटिंग प्राप्त की जा सकती है।
- जटिल आकार या नुकीले किनारों वाले उत्पादों को अच्छी तरह से लेपित किया जा सकता है।
- अधिकांश पाउडर वाले प्लास्टिक में उत्कृष्ट भंडारण स्थिरता होती है।
- किसी विलायक की आवश्यकता नहीं है, जिससे सामग्री तैयार करने की प्रक्रिया सरल हो जाती है। हालाँकि, पाउडर कोटिंग की कुछ कमियाँ या सीमाएँ भी हैं। उदाहरण के लिए, यदि वर्कपीस को पहले से गरम करने की आवश्यकता है, तो इसका आकार सीमित होगा। क्योंकि कोटिंग प्रक्रिया में समय लगता है, बड़े आकार के वर्कपीस के लिए, जबकि छिड़काव अभी तक समाप्त नहीं हुआ है, कुछ क्षेत्र पहले ही आवश्यक तापमान से नीचे ठंडे हो चुके हैं। प्लास्टिक पाउडर कोटिंग प्रक्रिया के दौरान, पाउडर का नुकसान 60% तक हो सकता है, इसलिए आर्थिक आवश्यकताओं को पूरा करने के लिए इसे एकत्र किया जाना चाहिए और पुन: उपयोग किया जाना चाहिए।
लौ छिड़काव
धातु के लिए फ्लेम स्प्रेइंग प्लास्टिक कोटिंग एक ऐसी प्रक्रिया है जिसमें स्प्रे गन से निकलने वाली लौ के साथ पाउडर या पेस्टी प्लास्टिक को पिघलाना या आंशिक रूप से पिघलाना शामिल है, और फिर प्लास्टिक कोटिंग बनाने के लिए पिघले हुए प्लास्टिक को किसी वस्तु की सतह पर स्प्रे करना शामिल है। कोटिंग की मोटाई आमतौर पर 0.1 और 0.7 मिमी के बीच होती है। ज्वाला छिड़काव के लिए पाउडर प्लास्टिक का उपयोग करते समय, वर्कपीस को पहले से गरम किया जाना चाहिए। प्रीहीटिंग ओवन में किया जा सकता है, और प्रीहीटिंग का तापमान अलग-अलग होता हैepeछिड़काव किए जाने वाले प्लास्टिक के प्रकार पर निर्भर करता है।
छिड़काव के दौरान लौ के तापमान को सख्ती से नियंत्रित किया जाना चाहिए, क्योंकि बहुत अधिक तापमान प्लास्टिक को जला सकता है या क्षतिग्रस्त कर सकता है, जबकि बहुत कम तापमान आसंजन को प्रभावित कर सकता है। आमतौर पर, प्लास्टिक की पहली परत का छिड़काव करते समय तापमान सबसे अधिक होता है, जिससे धातु और प्लास्टिक के बीच आसंजन में सुधार हो सकता है। जैसे ही बाद की परतों का छिड़काव किया जाता है, तापमान को थोड़ा कम किया जा सकता है। स्प्रे गन और वर्कपीस के बीच की दूरी 100 से 200 सेमी के बीच होनी चाहिए। फ्लैट वर्कपीस के लिए, वर्कपीस को क्षैतिज रूप से रखा जाना चाहिए और स्प्रे गन को आगे और पीछे ले जाना चाहिए; बेलनाकार या आंतरिक बोर वर्कपीस के लिए, उन्हें घूर्णी छिड़काव के लिए एक खराद पर लगाया जाना चाहिए। घूमने वाले वर्कपीस की रैखिक गति 20 से 60 मीटर/मिनट के बीच होनी चाहिए। कोटिंग की आवश्यक मोटाई प्राप्त होने के बाद, छिड़काव बंद कर देना चाहिए और पिघला हुआ प्लास्टिक जमने तक वर्कपीस को घुमाना जारी रखना चाहिए, और फिर इसे तेजी से ठंडा करना चाहिए।
यद्यपि लौ छिड़काव में अपेक्षाकृत कम उत्पादन क्षमता होती है और इसमें परेशान करने वाली गैसों का उपयोग शामिल होता है, फिर भी यह अन्य तरीकों की तुलना में टैंक, कंटेनर और बड़े वर्कपीस के अंदरूनी हिस्सों को कोटिंग करने में कम उपकरण निवेश और प्रभावशीलता के कारण उद्योग में एक महत्वपूर्ण प्रसंस्करण विधि है। .
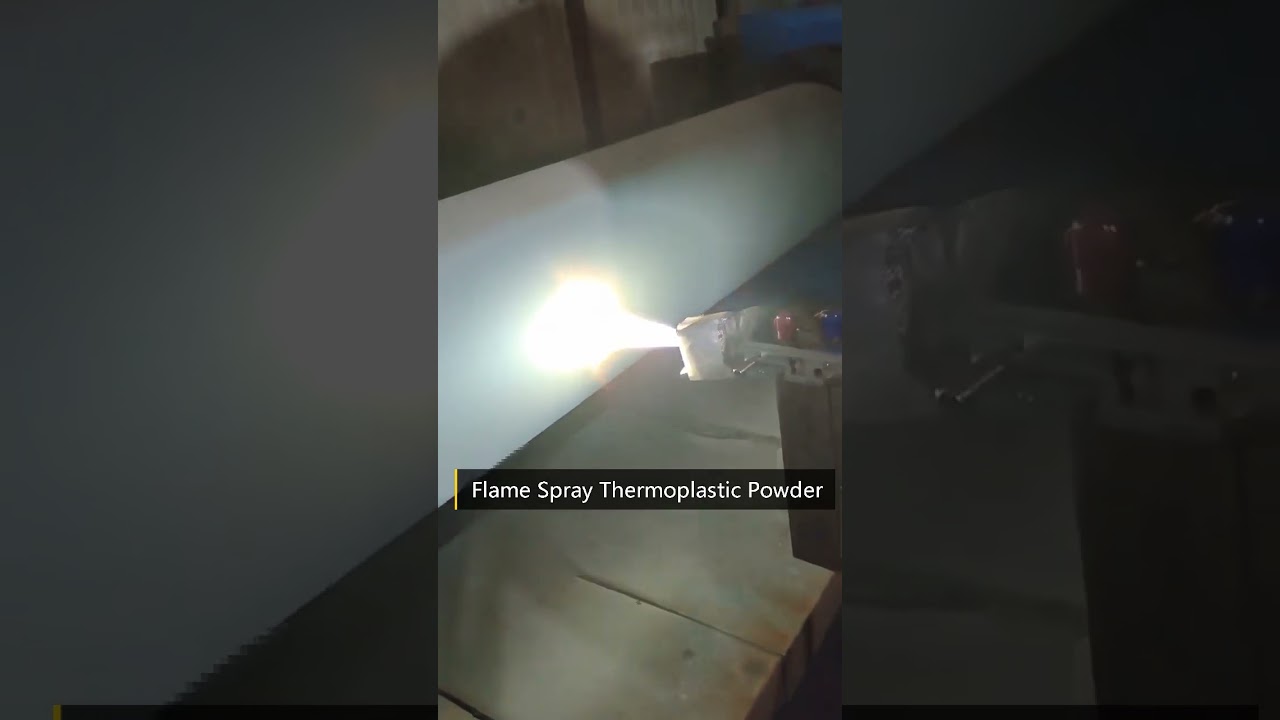
द्रवीकृत-बिस्तर डिप प्लास्टिक कोटिंग
धातु के लिए द्रवयुक्त बेड डिप प्लास्टिक कोटिंग का कार्य सिद्धांत इस प्रकार है: प्लास्टिक कोटिंग पाउडर को एक बेलनाकार कंटेनर में शीर्ष पर एक छिद्रपूर्ण विभाजन के साथ रखा जाता है जो केवल हवा को गुजरने की अनुमति देता है, पाउडर को नहीं। जब संपीड़ित हवा कंटेनर के नीचे से प्रवेश करती है, तो यह पाउडर को उड़ा देती है और कंटेनर में निलंबित कर देती है। यदि पहले से गर्म किए गए वर्कपीस को इसमें डुबोया जाए, तो राल पाउडर पिघल जाएगा और वर्कपीस से चिपक जाएगा, जिससे एक कोटिंग बन जाएगी।
द्रवीकृत बिस्तर में प्राप्त कोटिंग की मोटाई depeजब वर्कपीस द्रवीकृत कक्ष में प्रवेश करता है तो तापमान, विशिष्ट ताप क्षमता, सतह गुणांक, स्प्रे समय और उपयोग किए जाने वाले प्लास्टिक के प्रकार पर निर्भर करता है। हालाँकि, इस प्रक्रिया में केवल वर्कपीस के तापमान और स्प्रे समय को नियंत्रित किया जा सकता है, और उन्हें उत्पादन में प्रयोगों द्वारा निर्धारित करने की आवश्यकता होती है।
डिपिंग के दौरान, यह आवश्यक है कि प्लास्टिक पाउडर सुचारू रूप से और समान रूप से बहे, बिना एकत्रीकरण, भंवर प्रवाह या प्लास्टिक कणों के अत्यधिक फैलाव के। इन आवश्यकताओं को पूरा करने के लिए तदनुरूप उपाय किए जाने चाहिए। एक सरगर्मी उपकरण जोड़ने से ढेर और भंवर प्रवाह को कम किया जा सकता है, जबकि प्लास्टिक पाउडर में थोड़ी मात्रा में टैल्कम पाउडर मिलाना द्रवीकरण के लिए फायदेमंद है, लेकिन यह कोटिंग की गुणवत्ता को प्रभावित कर सकता है। प्लास्टिक कणों के फैलाव को रोकने के लिए वायु प्रवाह दर और प्लास्टिक पाउडर कणों की एकरूपता को सख्ती से नियंत्रित किया जाना चाहिए। हालाँकि, कुछ फैलाव अपरिहार्य है, इसलिए द्रवयुक्त बिस्तर के ऊपरी हिस्से में एक पुनर्प्राप्ति उपकरण स्थापित किया जाना चाहिए।
द्रवीकृत बेड डिप प्लास्टिक कोटिंग के फायदे जटिल आकार के वर्कपीस को कोट करने की क्षमता, उच्च कोटिंग गुणवत्ता, एक आवेदन में मोटी कोटिंग प्राप्त करना, न्यूनतम राल हानि और एक स्वच्छ कार्य वातावरण हैं। नुकसान बड़े वर्कपीस को संसाधित करने में कठिनाई है।
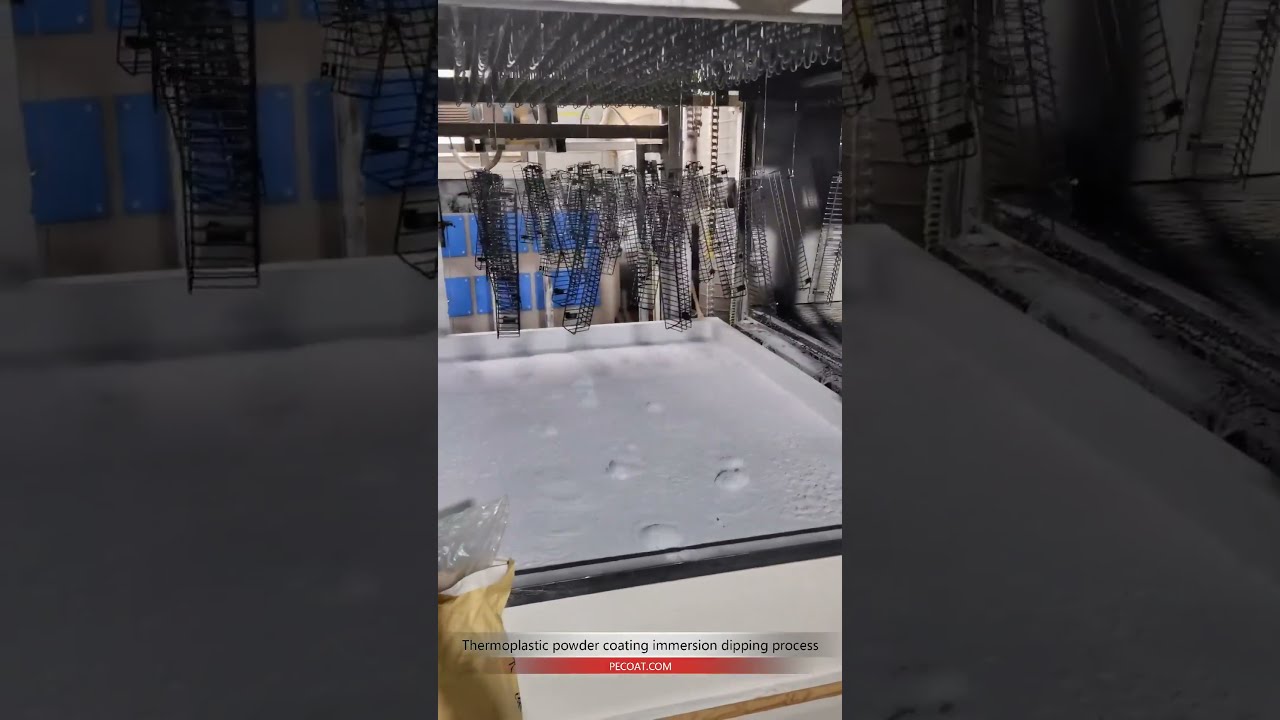
धातु के लिए इलेक्ट्रोस्टैटिक छिड़काव प्लास्टिक कोटिंग
इलेक्ट्रोस्टैटिक छिड़काव में, राल प्लास्टिक कोटिंग पाउडर को पिघलने या सिंटरिंग के बजाय इलेक्ट्रोस्टैटिक बल द्वारा वर्कपीस की सतह पर तय किया जाता है। सिद्धांत यह है कि स्प्रे बंदूक से स्प्रे किए गए राल पाउडर को स्थैतिक बिजली से चार्ज करने के लिए एक उच्च-वोल्टेज इलेक्ट्रोस्टैटिक जनरेटर द्वारा गठित इलेक्ट्रोस्टैटिक क्षेत्र का उपयोग किया जाता है, और ग्राउंडेड वर्कपीस उच्च-वोल्टेज सकारात्मक इलेक्ट्रोड बन जाता है। परिणामस्वरूप, वर्कपीस की सतह पर एकसमान प्लास्टिक पाउडर की एक परत तेजी से जमा हो जाती है। चार्ज ख़त्म होने से पहले, पाउडर की परत मजबूती से चिपक जाती है। गर्म करने और ठंडा करने के बाद एक समान प्लास्टिक कोटिंग प्राप्त की जा सकती है।
पाउडर इलेक्ट्रोस्टैटिक छिड़काव 1960 के दशक के मध्य में विकसित किया गया था और इसे स्वचालित करना आसान है। यदि कोटिंग को मोटा होने की आवश्यकता नहीं है, तो इलेक्ट्रोस्टैटिक छिड़काव के लिए वर्कपीस को पहले से गरम करने की आवश्यकता नहीं होती है, इसलिए इसका उपयोग गर्मी-संवेदनशील सामग्री या वर्कपीस के लिए किया जा सकता है जो हीटिंग के लिए उपयुक्त नहीं हैं। इसके लिए बड़े भंडारण कंटेनर की भी आवश्यकता नहीं होती है, जो द्रवयुक्त बिस्तर छिड़काव में आवश्यक है। वर्कपीस को बायपास करने वाला पाउडर वर्कपीस के पीछे की ओर आकर्षित होता है, इसलिए ओवरस्प्रे की मात्रा अन्य छिड़काव विधियों की तुलना में बहुत कम होती है, और पूरे वर्कपीस को एक तरफ स्प्रे करके लेपित किया जा सकता है। हालाँकि, बड़े वर्कपीस को अभी भी दोनों तरफ से स्प्रे करने की आवश्यकता है।
विभिन्न क्रॉस-सेक्शन वाले वर्कपीस बाद के हीटिंग के लिए कठिनाइयाँ पैदा कर सकते हैं। यदि क्रॉस-सेक्शन में अंतर बहुत बड़ा है, तो कोटिंग का मोटा हिस्सा पिघलने के तापमान तक नहीं पहुंच सकता है, जबकि पतला हिस्सा पहले ही पिघल चुका है या ख़राब हो चुका है। इस मामले में, राल की थर्मल स्थिरता महत्वपूर्ण है।
साफ आंतरिक कोनों और गहरे छेद वाले घटकों को इलेक्ट्रोस्टैटिक छिड़काव द्वारा आसानी से कवर नहीं किया जाता है क्योंकि इन क्षेत्रों में इलेक्ट्रोस्टैटिक परिरक्षण होता है और आरepeएल पाउडर, कोटिंग को कोनों या छिद्रों में प्रवेश करने से रोकता है जब तक कि स्प्रे बंदूक उनमें नहीं डाली जा सकती। इसके अलावा, इलेक्ट्रोस्टैटिक छिड़काव के लिए महीन कणों की आवश्यकता होती है क्योंकि बड़े कणों के वर्कपीस से अलग होने की अधिक संभावना होती है, और 150 जाल से अधिक महीन कण इलेक्ट्रोस्टैटिक क्रिया में अधिक प्रभावी होते हैं।
गर्म पिघल कोटिंग विधि
गर्म पिघल कोटिंग विधि का कार्य सिद्धांत एक स्प्रे बंदूक का उपयोग करके पहले से गरम वर्कपीस पर प्लास्टिक कोटिंग पाउडर को स्प्रे करना है। वर्कपीस की गर्मी का उपयोग करके प्लास्टिक पिघल जाता है, और ठंडा होने के बाद, वर्कपीस पर प्लास्टिक कोटिंग लगाई जा सकती है। यदि आवश्यक हो तो पोस्ट-हीटिंग उपचार की भी आवश्यकता होती है।
गर्म पिघल कोटिंग प्रक्रिया को नियंत्रित करने की कुंजी वर्कपीस का प्रीहीटिंग तापमान है। जब प्रीहीटिंग तापमान बहुत अधिक होता है, तो यह धातु की सतह के गंभीर ऑक्सीकरण का कारण बन सकता है, कोटिंग के आसंजन को कम कर सकता है, और यहां तक कि राल के अपघटन और कोटिंग के झाग या मलिनकिरण का कारण भी बन सकता है। जब प्रीहीटिंग तापमान बहुत कम होता है, तो राल में खराब प्रवाह क्षमता होती है, जिससे एक समान कोटिंग प्राप्त करना मुश्किल हो जाता है। अक्सर, गर्म पिघल कोटिंग विधि का एक एकल स्प्रे अनुप्रयोग वांछित मोटाई प्राप्त नहीं कर सकता है, इसलिए कई स्प्रे अनुप्रयोगों की आवश्यकता होती है। प्रत्येक स्प्रे लगाने के बाद, दूसरी परत लगाने से पहले कोटिंग को पूरी तरह से पिघलाने और चमकाने के लिए हीटिंग उपचार आवश्यक है। यह न केवल एक समान और चिकनी कोटिंग सुनिश्चित करता है बल्कि यांत्रिक शक्ति में भी काफी सुधार करता है। उच्च-घनत्व पॉलीथीन के लिए अनुशंसित हीटिंग उपचार तापमान लगभग 170°C है, और क्लोरीनयुक्त पॉलीथर के लिए, यह लगभग 200°C है, जिसमें 1 घंटे का अनुशंसित समय है।
गर्म पिघल कोटिंग विधि न्यूनतम राल हानि के साथ उच्च गुणवत्ता वाली, सौंदर्य की दृष्टि से मनभावन, मजबूती से बंधी कोटिंग का उत्पादन करती है। इसे नियंत्रित करना आसान है, इसमें न्यूनतम गंध होती है, और उपयोग की जाने वाली स्प्रे गन ऐसा करती है।
धातु पर प्लास्टिक कोटिंग के लिए अन्य विधियाँ उपलब्ध हैं
1. छिड़काव: सस्पेंशन को स्प्रे गन जलाशय में भरें और वर्कपीस की सतह पर कोटिंग को समान रूप से स्प्रे करने के लिए 0.1 एमपीए से अधिक के गेज दबाव के साथ संपीड़ित हवा का उपयोग करें। निलंबन हानि को कम करने के लिए हवा का दबाव यथासंभव कम रखा जाना चाहिए। वर्कपीस और नोजल के बीच की दूरी 10-20 सेमी बनाए रखी जानी चाहिए, और छिड़काव सतह को सामग्री प्रवाह की दिशा के लंबवत रखा जाना चाहिए।
2. विसर्जन: वर्कपीस को कुछ सेकंड के लिए सस्पेंशन में डुबोएं, फिर इसे हटा दें। इस बिंदु पर, निलंबन की एक परत वर्कपीस की सतह पर चिपक जाएगी, और अतिरिक्त तरल स्वाभाविक रूप से नीचे बह सकता है। यह विधि छोटे आकार के वर्कपीस के लिए उपयुक्त है जिन्हें बाहरी सतह पर पूर्ण कोटिंग की आवश्यकता होती है।
3. ब्रश करना: ब्रश करने में वर्कपीस की सतह पर सस्पेंशन लगाने, एक कोटिंग बनाने के लिए पेंटब्रश या ब्रश का उपयोग करना शामिल है। ब्रश करना सामान्य स्थानीयकृत कोटिंग या संकीर्ण सतहों पर एकल-पक्षीय कोटिंग के लिए उपयुक्त है। हालाँकि, कोटिंग सूखने के बाद कम चिकनी और समान सतह और प्रत्येक कोटिंग परत की मोटाई पर सीमा के कारण इसका उपयोग शायद ही कभी किया जाता है।
4. डालना: सस्पेंशन को घूमने वाले खोखले वर्कपीस में डालें, यह सुनिश्चित करते हुए कि आंतरिक सतह पूरी तरह से सस्पेंशन से ढकी हुई है। फिर, एक कोटिंग बनाने के लिए अतिरिक्त तरल डालें। यह विधि छोटे रिएक्टरों, पाइपलाइनों, एल्बो, वाल्व, पंप केसिंग, टीज़ और अन्य समान वर्कपीस को कोटिंग करने के लिए उपयुक्त है।
मैं धातु के तार के लिए थर्मोप्लास्टिक कोटिंग्स की तलाश में हूं
यह इंटरनेट साइट मेरी प्रेरणा है, वास्तव में अच्छा लेआउट और उत्तम सामग्री।
मुझे लगता है कि यह मेरे लिए बहुत महत्वपूर्ण जानकारी में से एक है। और मुझे आपका लेख पढ़कर ख़ुशी हुई. लेकिन कुछ सामान्य चीजों पर बयान देना चाहता हूं, साइट का स्वाद उत्तम है, लेख वास्तव में बहुत अच्छे हैं: डी. अच्छा काम, जयकार