Controllo della temperatura di preriscaldamento nel processo di immersione a letto fluidizzato
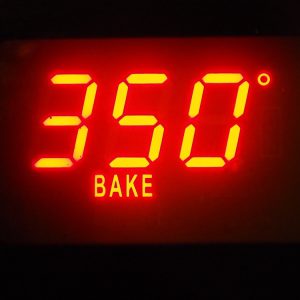
Introduzione allo sfondo
In letto fluido processo di immersione, la capacità termica del pezzo viene utilizzata per fondere la polvere termoplastica e ottenere lo spessore e la qualità del rivestimento desiderati. Pertanto, determinare la temperatura di preriscaldamento appropriata del pezzo è fondamentale. La temperatura di preriscaldamento dovrebbe essere leggermente superiore alla temperatura di fusione polvere termoplastica. Se è troppo elevato, potrebbero verificarsi difetti di flusso dovuti a rivestimenti eccessivamente spessi o alla rottura della resina polimerica, con conseguenti bolle, ingiallimento o bruciatura. Al contrario, se è troppo basso, una fusione insufficiente porterà a rivestimenti sottili con buchi superficiali o incompletezze che non riescono a soddisfare gli obiettivi di immersione.
In generale, la temperatura di preriscaldamento del pezzo è influenzata da fattori quali materiale, dimensioni, forma, prestazioni della polvere termoplastica, spessore del rivestimento richiesto, tempo di riscaldamento e durata di immersione. Tuttavia, nelle operazioni pratiche, i pezzi variano notevolmente in termini di spessore, dimensione e forma, rendendo difficile determinare quantitativamente la temperatura di preriscaldamento.
Per esplorare la temperatura di preriscaldamento appropriata per i pezzi durante polvere del letto fluidizzato processo di immersione, utilizziamo il nostro sistema di immersione automatico a letto fluidizzato autoprogettato e prodotto. Combinando questo con la nostra esperienza nella produzione di vari prodotti come recinzioni per l'isolamento del traffico, reti di protezione per guardrail di edifici comunali e di giardini, scaffali di frigoriferi, scaffali per la spesa, reti per gabbie per allevamento, molle e tubi di acciaio utilizzando diverse polveri termoplastiche, gli esperimenti forniscono una base teorica e metodologia per ottimizzare il processo di immersione.
Metodi sperimentali
1. Preparazione del campione
I campioni sono costituiti principalmente da acciaio a forma di bastoncino, alcuni anche in rame e alluminio, con diametri 0.8, 1.0, 2.0, 3.0, 4.0, 5.0, 6.0, 7.0, 8.0, 9.0, 10.0, 12.0, 14.0, 16.0, 18.0 , 20.0
2. Polvere termoplastica
Nell'esperimento sono state utilizzate prevalentemente polveri termoplastiche LDPE, mentre PVCAnche , PA e altre polveri sono state sottoposte a test.
3.Processo
Pretrattamento → preriscaldamento → immersione in polvere → post-riscaldamento (indurimento) → raffreddamento
4. Qualità del rivestimento
Sono state impiegate diverse temperature di preriscaldamento per immergere i suddetti campioni in varie polveri termoplastiche; dopo i processi di polimerizzazione e livellamento a bassa temperatura, la qualità del rivestimento era evavalutati e registrati nella Tabella 1, Tabella 2 e Tabella 3.
Analisi dei fattori che influenzano
Sulla base dei risultati sperimentali e insieme ai dati presentati nella Tabella 1, Tabella 2 e Tabella 3, è stata tracciata una curva per rappresentare il valore ottimale della temperatura di preriscaldamento per ciascun campione, come illustrato nella figura.
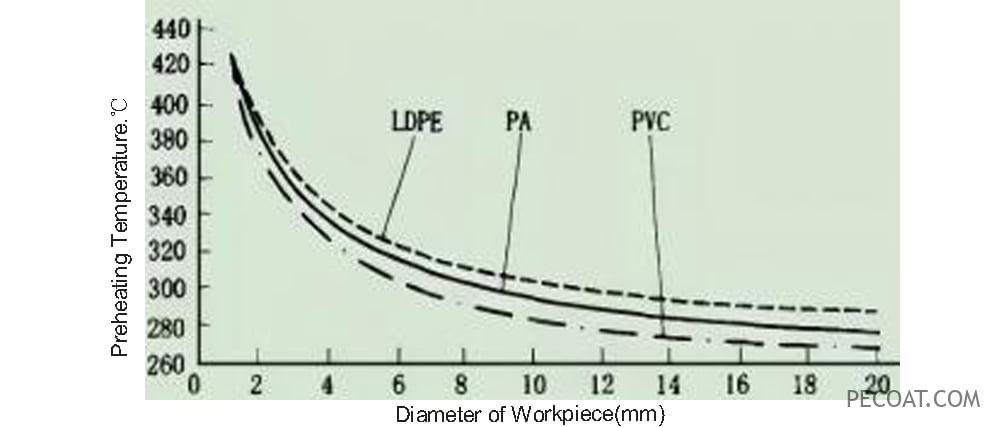
Impatti della polvere termoplastica
La curva di riscaldamento del pezzo varia a seconda delle diverse resine in polvere, come illustrato nella figura sopra. A causa dell'ampio intervallo tra il punto di rammollimento (80 – 90 ℃) e il punto di fusione (105 – 130 ℃) del polietilene (PE)Oltre ad una temperatura di cracking di 300 ℃, è necessaria una temperatura di preriscaldamento più elevata per il pezzo. Solo se riscaldato a temperature superiori a 360 ℃ per un periodo prolungato si verifica un ingiallimento del rivestimento.
Cloruro di polivinile(PVC) non ha un punto di fusione distinto ma inizia ad ammorbidirsi a 130 ℃ e può scorrere a 180 ℃. Inizia a decomporsi sopra i 200 ℃, rilasciando acido cloridrico, fumo ed emettendo un odore nasale. Lievi aumenti di temperatura o tempi di esposizione più lunghi provocano gradualmente l'ingiallimento e l'annerimento del rivestimento. COME PVCPoiché la temperatura di fusione è vicina alla temperatura di decomposizione, è necessario un controllo più rigoroso sulla temperatura di preriscaldamento del pezzo.
I rivestimenti in poliammide (PA) (tipicamente nylon 1010, nylon 11, nylon 12) hanno un punto di fusione compreso tra 180 e 230 ℃ e temperature di decomposizione termica superiori a 300 ℃; tuttavia, l'intervallo tra le temperature di fusione e di decomposizione rimane ristretto. L'immersione del nylon spesso richiede un raffreddamento immediato e il controllo della temperatura di preriscaldamento risulta impegnativo.
Influenza dello spessore del pezzo
In teoria, la temperatura di preriscaldamento del pezzo dovrebbe essere leggermente superiore alla temperatura di fusione della polvere per facilitare l'indurimento e la deposizione della polvere sulla superficie metallica. Tuttavia, i risultati sperimentali indicano variazioni significative nelle temperature di preriscaldamento per pezzi con diametri e spessori diversi. Ciò è dovuto alla maggiore capacità termica dei pezzi più spessi, che ostacola un'efficiente dissipazione del calore dopo il riscaldamento e porta a variazioni minime di temperatura durante il trasferimento dal forno al serbatoio della polvere. Di conseguenza, una temperatura di preriscaldamento elevata non può essere applicata a pezzi più spessi; devono invece essere riscaldati a temperature più basse per periodi più lunghi. Al contrario, i pezzi più piccoli possiedono capacità termiche inferiori e dissipano il calore rapidamente, rendendo necessario l’utilizzo dell’”effetto shock termico” attraverso temperature di preriscaldamento più elevate per un’efficace fusione della resina in polvere. I pezzi ultrasottili hanno una capacità termica minima e anche con elevatemperature elevate diventa difficile ottenere la completa adesione del rivestimento.
Per i pezzi realizzati con materiali con diametri o spessori variabili, è necessario prestare una considerazione approfondita nel determinare le temperature di preriscaldamento, assicurando che la temperatura più bassa garantisca una copertura completa del rivestimento nelle aree più sottili evitando l'ingiallimento sulle sezioni più spesse selezionando un limite superiore appropriato.
Influenza del materiale del pezzo
La maggior parte dei pezzi di prova sopra menzionati sono realizzati in acciaio a basso tenore di carbonio. Per diversi tipi di acciaio, sia esso acciaio al carbonio o acciaio legato, la temperatura di preriscaldamento ha un impatto minimo. La temperatura di preriscaldamento del rame è simile a quella dell'acciaio ma leggermente superiore. L'alluminio ha una rapida conduzione e dissipazione del calore, quindi la temperatura di preriscaldamento dovrebbe essere più alta.
Influenza della forma del pezzo
Sono stati condotti esperimenti anche su pezzi di forme diverse, rivelando che le parti solide mostrano velocità di accumulo e dissipazione del calore più lente, mentre le parti cave chiuse come i componenti tubolari mostrano anche una ridotta dissipazione del calore. Al contrario, le parti in rete e sottili subiscono la perdita di calore più rapida. La velocità di accumulo e dissipazione del calore è determinata principalmente dal rapporto volume/superficie del pezzo. Pertanto è necessario regolare la temperatura di preriscaldamento in base ad un opportuno coefficiente corrispondente alla forma del pezzo. Sono necessarie ulteriori ricerche in questo settore.
Conclusione
- La temperatura di preriscaldamento del pezzo è il fattore più critico nel determinare la qualità del rivestimento durante l'immersione in letto fluidizzato.
- La temperatura di preriscaldamento del pezzo è determinata principalmente dal suo diametro o spessore e può essere determinata facendo riferimento alla Figura 1 come guida.
- Diverse resine in polvere hanno punti di fusione e di decomposizione diversi, che dovrebbero essere attentamente considerati quando si determina il processo di immersione.
- Il materiale e la forma del pezzo influiscono anche sulla temperatura di preriscaldamento richiesta, che può essere compensata mediante un fattore di correzione.