धातूसाठी प्लास्टिक कोटिंग
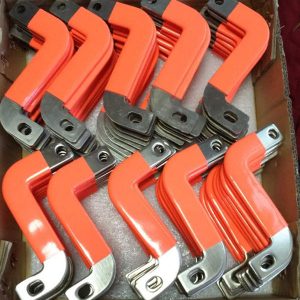
धातूच्या प्रक्रियेसाठी प्लॅस्टिक कोटिंग म्हणजे धातूच्या भागांच्या पृष्ठभागावर प्लास्टिकचा थर लावणे, ज्यामुळे त्यांना धातूची मूळ वैशिष्ट्ये टिकवून ठेवता येतात आणि प्लास्टिकचे विशिष्ट गुणधर्म जसे की गंज प्रतिकार, पोशाख प्रतिरोध, इलेक्ट्रिकल इन्सुलेशन आणि स्वत: ची वैशिष्ट्ये देखील प्रदान करतात. - स्नेहन. उत्पादनांच्या अनुप्रयोग श्रेणीचा विस्तार करण्यासाठी आणि त्यांचे आर्थिक मूल्य वाढविण्यासाठी ही प्रक्रिया खूप महत्त्वाची आहे.
धातूसाठी प्लास्टिक कोटिंगसाठी पद्धती
ज्वाला फवारणीसह प्लास्टिक कोटिंगसाठी अनेक पद्धती आहेत. द्रवीकृत बेड फवारणी, पावडर इलेक्ट्रोस्टॅटिक फवारणी, हॉट मेल्ट कोटिंग आणि सस्पेंशन कोटिंग. कोटिंगसाठी वापरल्या जाणार्या प्लास्टिकचे अनेक प्रकार देखील आहेत PVC, PE, आणि PA सर्वात सामान्यपणे वापरले जात आहे. कोटिंगसाठी वापरलेले प्लास्टिक पावडर स्वरूपात असणे आवश्यक आहे, ज्याची सूक्ष्मता 80-120 जाळी आहे.
कोटिंग केल्यानंतर, वर्कपीस थंड पाण्यात बुडवून त्वरीत थंड करणे चांगले. जलद थंडीमुळे प्लॅस्टिक कोटिंगची स्फटिकता कमी होऊ शकते, पाण्याचे प्रमाण वाढू शकते, कोटिंगचा कडकपणा आणि पृष्ठभागाची चमक सुधारू शकते, आसंजन वाढू शकते आणि अंतर्गत तणावामुळे कोटिंगच्या अलिप्ततेवर मात करता येते.
कोटिंग आणि बेस मेटलमधील आसंजन सुधारण्यासाठी, वर्कपीसची पृष्ठभाग धूळमुक्त आणि कोरडी असावी, कोटिंग करण्यापूर्वी गंज आणि ग्रीसशिवाय. बर्याच बाबतीत, वर्कपीसला पृष्ठभागावर उपचार करणे आवश्यक आहे. उपचार पद्धतींमध्ये सँडब्लास्टिंग, रासायनिक उपचार आणि इतर यांत्रिक पद्धतींचा समावेश होतो. त्यापैकी, सँडब्लास्टिंगचे चांगले परिणाम होतात कारण ते वर्कपीसची पृष्ठभाग खडबडीत करते, पृष्ठभागाचे क्षेत्रफळ वाढवते आणि हुक बनवते, त्यामुळे चिकटपणा सुधारतो. सँडब्लास्टिंग केल्यानंतर, धूळ काढण्यासाठी वर्कपीसच्या पृष्ठभागावर स्वच्छ संकुचित हवेने उडवले पाहिजे आणि 6 तासांच्या आत प्लास्टिकचे लेप केले पाहिजे, अन्यथा, पृष्ठभाग ऑक्सिडाइझ होईल, ज्यामुळे कोटिंगच्या चिकटपणावर परिणाम होईल.
फायदा
पावडर प्लास्टिकसह थेट कोटिंगचे खालील फायदे आहेत:
- हे रेजिनसह वापरले जाऊ शकते जे केवळ पावडर स्वरूपात उपलब्ध आहेत.
- एका अर्जात जाड कोटिंग मिळू शकते.
- जटिल आकार किंवा तीक्ष्ण कडा असलेली उत्पादने चांगले लेपित केली जाऊ शकतात.
- बहुतेक पावडर प्लास्टिकमध्ये उत्कृष्ट स्टोरेज स्थिरता असते.
- कोणत्याही सॉल्व्हेंट्सची आवश्यकता नाही, ज्यामुळे सामग्री तयार करण्याची प्रक्रिया सोपी होते. तथापि, पावडर कोटिंगमध्ये काही कमतरता किंवा मर्यादा देखील आहेत. उदाहरणार्थ, जर वर्कपीस प्रीहीट करणे आवश्यक असेल तर त्याचा आकार मर्यादित असेल. मोठ्या आकाराच्या वर्कपीससाठी कोटिंग प्रक्रियेस वेळ लागतो, फवारणी अद्याप पूर्ण झालेली नसताना, काही भाग आधीच आवश्यक तापमानापेक्षा कमी झाले आहेत. प्लॅस्टिक पावडर कोटिंग प्रक्रियेदरम्यान, पावडरचे नुकसान 60% इतके जास्त असू शकते, म्हणून आर्थिक गरजा पूर्ण करण्यासाठी ते गोळा करणे आणि पुन्हा वापरणे आवश्यक आहे.
ज्योत फवारणी
धातूसाठी फ्लेम स्प्रेिंग प्लॅस्टिक कोटिंग ही एक प्रक्रिया आहे ज्यामध्ये स्प्रे गनमधून उत्सर्जित केलेल्या ज्वालासह पावडर किंवा पेस्टी प्लास्टिक वितळणे किंवा अंशतः वितळणे आणि नंतर प्लास्टिक कोटिंग तयार करण्यासाठी वितळलेल्या प्लास्टिकची वस्तूच्या पृष्ठभागावर फवारणी करणे समाविष्ट आहे. कोटिंगची जाडी सामान्यतः 0.1 आणि 0.7 मिमी दरम्यान असते. ज्वाला फवारणीसाठी पावडर प्लास्टिक वापरताना, वर्कपीस आधीपासून गरम केले पाहिजे. ओव्हनमध्ये प्रीहीटिंग करता येते आणि प्रीहीटिंग तापमान बदलते depeप्लास्टिक फवारणीच्या प्रकारावर nding.
फवारणी दरम्यान ज्वालाचे तापमान काटेकोरपणे नियंत्रित केले जाणे आवश्यक आहे, कारण खूप जास्त तापमान प्लास्टिक जाळू शकते किंवा नुकसान करू शकते, तर खूप कमी तापमान चिकटपणावर परिणाम करू शकते. सामान्यतः, प्लास्टिकच्या पहिल्या थराची फवारणी करताना तापमान सर्वात जास्त असते, ज्यामुळे धातू आणि प्लास्टिकमधील चिकटपणा सुधारू शकतो. त्यानंतरच्या थरांवर फवारणी केल्याने, तापमान किंचित कमी केले जाऊ शकते. स्प्रे गन आणि वर्कपीसमधील अंतर 100 ते 200 सेमी दरम्यान असावे. सपाट वर्कपीससाठी, वर्कपीस क्षैतिजरित्या ठेवली पाहिजे आणि स्प्रे गन पुढे आणि मागे हलवावी; दंडगोलाकार किंवा अंतर्गत बोअर वर्कपीससाठी, ते रोटेशनल फवारणीसाठी लेथवर बसवावे. फिरणाऱ्या वर्कपीसची रेषीय गती 20 ते 60 मी/मिनिट दरम्यान असावी. कोटिंगची आवश्यक जाडी प्राप्त झाल्यानंतर, फवारणी थांबविली पाहिजे आणि वितळलेले प्लास्टिक घट्ट होईपर्यंत वर्कपीस फिरत रहावे आणि नंतर ते वेगाने थंड केले पाहिजे.
जरी फ्लेम फवारणीची उत्पादन क्षमता तुलनेने कमी आहे आणि त्यात त्रासदायक वायूंचा वापर समाविष्ट आहे, तरीही कमी उपकरणे गुंतवणुकीमुळे आणि इतर पद्धतींच्या तुलनेत टाक्या, कंटेनर आणि मोठ्या वर्कपीसच्या आतील भागांना कोटिंग करण्यात प्रभावीपणामुळे ही एक महत्त्वाची प्रक्रिया पद्धत आहे. .
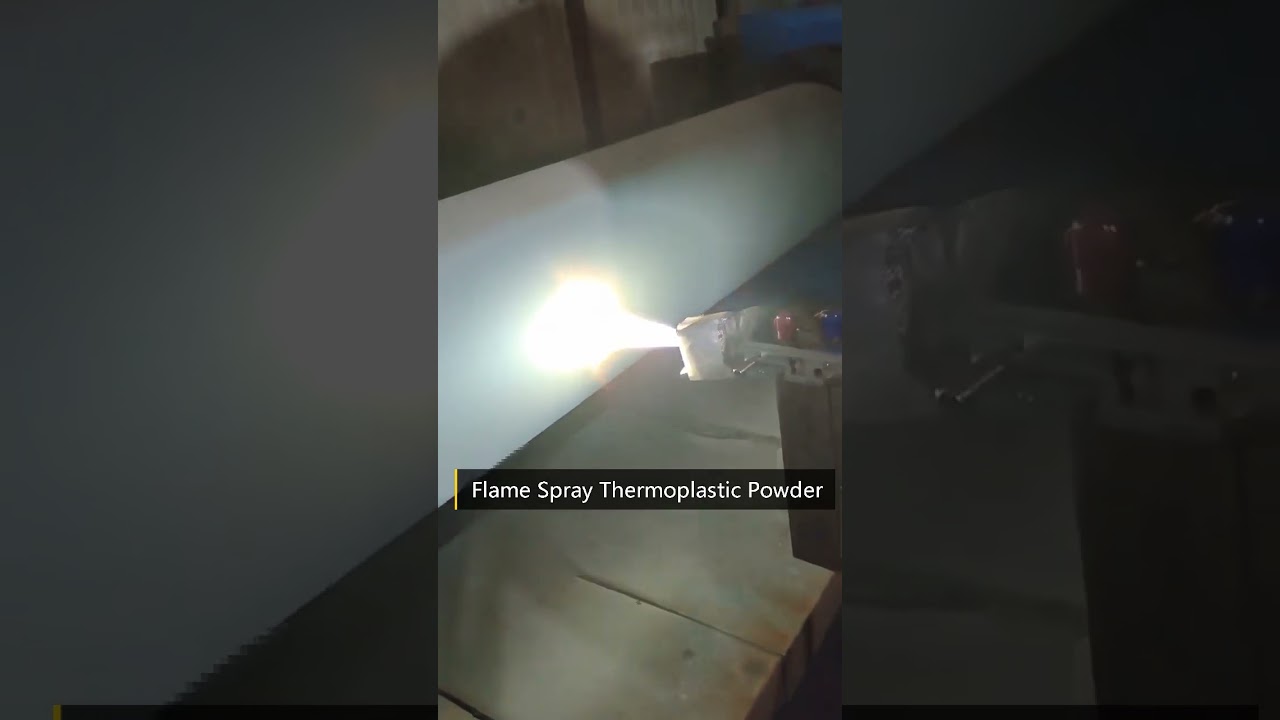
फ्लुइडाइज्ड-बेड डिप प्लॅस्टिक कोटिंग
धातूसाठी फ्लुइडाइज्ड बेड डिप प्लास्टिक कोटिंगचे कार्य तत्त्व खालीलप्रमाणे आहे: प्लास्टिक कोटिंग पावडर एका दंडगोलाकार कंटेनरमध्ये ठेवली जाते ज्यामध्ये शीर्षस्थानी सच्छिद्र विभाजन असते ज्यामुळे फक्त हवा जाऊ शकते, पावडर नाही. जेव्हा संकुचित हवा कंटेनरच्या तळापासून आत जाते तेव्हा ती पावडर वर उडवते आणि कंटेनरमध्ये निलंबित करते. जर प्रीहिटेड वर्कपीस त्यात बुडवले असेल तर, राळ पावडर वितळेल आणि वर्कपीसला चिकटून एक कोटिंग तयार करेल.
द्रवीकृत पलंगात प्राप्त कोटिंगची जाडी depeतापमान, विशिष्ट उष्णता क्षमता, पृष्ठभाग गुणांक, फवारणीची वेळ आणि वर्कपीस द्रवीकृत चेंबरमध्ये प्रवेश करते तेव्हा वापरल्या जाणार्या प्लास्टिकचा प्रकार यावर एनडीएस. तथापि, प्रक्रियेत वर्कपीसचे तापमान आणि फवारणीची वेळ नियंत्रित केली जाऊ शकते आणि ते उत्पादनातील प्रयोगांद्वारे निर्धारित करणे आवश्यक आहे.
डिपिंग करताना, प्लास्टिक पावडर सुरळीतपणे आणि समान रीतीने वाहते, एकत्रीकरण, भोवरा प्रवाह किंवा प्लास्टिकच्या कणांचा जास्त प्रसार न करता आवश्यक आहे. या गरजा पूर्ण करण्यासाठी संबंधित उपाययोजना केल्या पाहिजेत. ढवळणारे यंत्र जोडल्याने संचलन आणि भोवरा कमी होऊ शकतो, तर प्लॅस्टिक पावडरमध्ये थोड्या प्रमाणात टॅल्कम पावडर टाकणे द्रवीकरणासाठी फायदेशीर आहे, परंतु त्याचा कोटिंगच्या गुणवत्तेवर परिणाम होऊ शकतो. प्लॅस्टिकच्या कणांचा प्रसार रोखण्यासाठी, प्लॅस्टिक पावडरच्या कणांचा वायुप्रवाह दर आणि एकसमानता काटेकोरपणे नियंत्रित केली पाहिजे. तथापि, काही पांगापांग अपरिहार्य आहे, म्हणून द्रवीकरण केलेल्या बेडच्या वरच्या भागात पुनर्प्राप्ती उपकरण स्थापित केले पाहिजे.
फ्लुइडाइज्ड बेड डिप प्लॅस्टिक कोटिंगचे फायदे म्हणजे कॉम्प्लेक्स-आकाराच्या वर्कपीस कोटिंग करण्याची क्षमता, उच्च कोटिंगची गुणवत्ता, एका ऍप्लिकेशनमध्ये जाड कोटिंग मिळवणे, कमीतकमी राळ कमी होणे आणि स्वच्छ कार्य वातावरण. गैरसोय म्हणजे मोठ्या वर्कपीसवर प्रक्रिया करण्यात अडचण.
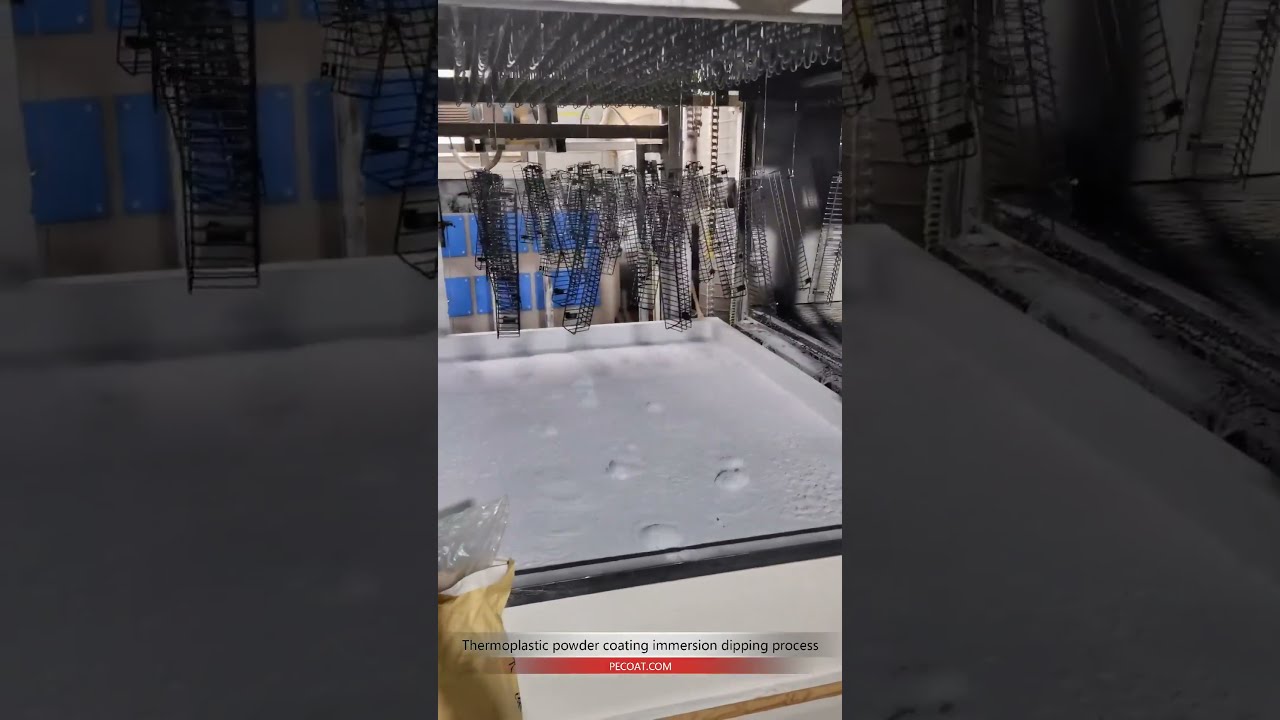
धातूसाठी इलेक्ट्रोस्टॅटिक फवारणी करणारे प्लास्टिक कोटिंग
इलेक्ट्रोस्टॅटिक फवारणीमध्ये, राळ प्लास्टिक कोटिंग पावडर वितळण्याऐवजी किंवा सिंटरिंग करण्याऐवजी इलेक्ट्रोस्टॅटिक शक्तीने वर्कपीसच्या पृष्ठभागावर निश्चित केली जाते. उच्च-व्होल्टेज इलेक्ट्रोस्टॅटिक जनरेटरद्वारे तयार केलेल्या इलेक्ट्रोस्टॅटिक फील्डचा वापर स्प्रे गनमधून स्प्रे केलेल्या राळ पावडरला स्थिर विजेसह चार्ज करण्यासाठी वापरणे हे आहे आणि ग्राउंडेड वर्कपीस उच्च-व्होल्टेज पॉझिटिव्ह इलेक्ट्रोड बनते. परिणामी, एकसमान प्लास्टिक पावडरचा थर वर्कपीसच्या पृष्ठभागावर पटकन जमा होतो. चार्ज नष्ट होण्यापूर्वी, पावडरचा थर घट्टपणे चिकटतो. गरम आणि थंड झाल्यानंतर, एकसमान प्लास्टिक कोटिंग मिळवता येते.
पावडर इलेक्ट्रोस्टॅटिक फवारणी 1960 च्या मध्यात विकसित केली गेली आणि स्वयंचलित करणे सोपे आहे. कोटिंग जाड असण्याची गरज नसल्यास, इलेक्ट्रोस्टॅटिक फवारणीसाठी वर्कपीस प्रीहीटिंगची आवश्यकता नसते, म्हणून ती उष्णता-संवेदनशील सामग्री किंवा गरम करण्यासाठी योग्य नसलेल्या वर्कपीससाठी वापरली जाऊ शकते. यासाठी मोठ्या स्टोरेज कंटेनरची देखील आवश्यकता नाही, जे फ्लुइडाइज्ड बेड फवारणीसाठी आवश्यक आहे. वर्कपीसला बायपास करणारी पावडर वर्कपीसच्या मागील बाजूस आकर्षित होते, म्हणून ओव्हरस्प्रेचे प्रमाण इतर फवारणी पद्धतींपेक्षा खूपच कमी असते आणि संपूर्ण वर्कपीस एका बाजूला फवारणी करून लेपित केले जाऊ शकते. तथापि, मोठ्या वर्कपीसला अद्याप दोन्ही बाजूंनी फवारणी करणे आवश्यक आहे.
वेगवेगळ्या क्रॉस-सेक्शनसह वर्कपीस नंतरच्या हीटिंगसाठी अडचणी निर्माण करू शकतात. क्रॉस-सेक्शनमधील फरक खूप मोठा असल्यास, कोटिंगचा जाड भाग वितळण्याच्या तपमानापर्यंत पोहोचू शकत नाही, तर पातळ भाग आधीच वितळलेला किंवा खराब झालेला असू शकतो. या प्रकरणात, राळची थर्मल स्थिरता महत्वाची आहे.
नीटनेटके अंतर्गत कोपरे आणि खोल छिद्रे असलेले घटक इलेक्ट्रोस्टॅटिक फवारणीद्वारे सहजपणे झाकले जात नाहीत कारण या भागात इलेक्ट्रोस्टॅटिक शील्डिंग असते आणि आर.epel पावडर, स्प्रे गन घातल्याशिवाय कोटिंगला कोपऱ्यात किंवा छिद्रांमध्ये प्रवेश करण्यास अडथळा आणते. याव्यतिरिक्त, इलेक्ट्रोस्टॅटिक फवारणीसाठी बारीक कणांची आवश्यकता असते कारण मोठे कण वर्कपीसमधून वेगळे होण्याची अधिक शक्यता असते आणि 150 जाळीपेक्षा बारीक कण इलेक्ट्रोस्टॅटिक क्रियेत अधिक प्रभावी असतात.
गरम वितळणे कोटिंग पद्धत
हॉट मेल्ट कोटिंग पद्धतीचे कार्य तत्त्व म्हणजे स्प्रे गन वापरून प्रीहेटेड वर्कपीसवर प्लास्टिक कोटिंग पावडर फवारणे. वर्कपीसच्या उष्णतेचा वापर करून प्लास्टिक वितळते आणि थंड झाल्यावर वर्कपीसवर प्लास्टिकचा लेप लावता येतो. आवश्यक असल्यास, पोस्ट-हीटिंग उपचार देखील आवश्यक आहे.
गरम वितळलेल्या कोटिंग प्रक्रियेवर नियंत्रण ठेवण्याची गुरुकिल्ली म्हणजे वर्कपीसचे प्रीहीटिंग तापमान. जेव्हा प्रीहीटिंग तापमान खूप जास्त असते, तेव्हा ते धातूच्या पृष्ठभागाचे तीव्र ऑक्सिडेशन होऊ शकते, कोटिंगचे आसंजन कमी करू शकते आणि राळचे विघटन आणि फेस किंवा कोटिंगचे विकृतीकरण देखील होऊ शकते. जेव्हा प्रीहीटिंग तापमान खूप कमी असते, तेव्हा राळची प्रवाहक्षमता खराब असते, ज्यामुळे एकसमान कोटिंग मिळवणे कठीण होते. बर्याचदा, हॉट मेल्ट कोटिंग पद्धतीचा एकच फवारणी इच्छित जाडी साध्य करू शकत नाही, म्हणून अनेक फवारणी आवश्यक असतात. प्रत्येक स्प्रे ऍप्लिकेशननंतर, दुसरा थर लावण्यापूर्वी कोटिंग पूर्णपणे वितळण्यासाठी आणि उजळ करण्यासाठी हीटिंग ट्रीटमेंट आवश्यक आहे. हे केवळ एकसमान आणि गुळगुळीत कोटिंग सुनिश्चित करत नाही तर यांत्रिक सामर्थ्य देखील लक्षणीयरीत्या सुधारते. उच्च-घनता पॉलीथिलीनसाठी शिफारस केलेले हीटिंग ट्रीटमेंट तापमान सुमारे 170°C आहे, आणि क्लोरीनयुक्त पॉलिथरसाठी, 200 तासाच्या शिफारस केलेल्या वेळेसह, ते सुमारे 1°C आहे.
हॉट मेल्ट कोटिंग पद्धत उच्च-गुणवत्तेचे, सौंदर्यदृष्ट्या सुखकारक, कमीत कमी रेजिनच्या नुकसानासह मजबूत बंधनकारक कोटिंग्ज तयार करते. हे नियंत्रित करणे सोपे आहे, कमीत कमी गंध आहे आणि वापरलेली स्प्रे गन हे करते.
धातूसाठी प्लास्टिक कोटिंगसाठी उपलब्ध इतर पद्धती
1. फवारणी: स्प्रे गन जलाशयात सस्पेन्शन भरा आणि वर्कपीसच्या पृष्ठभागावर समान रीतीने कोटिंग फवारण्यासाठी 0.1 MPa पेक्षा जास्त नसलेल्या गेज दाबाने संकुचित हवा वापरा. निलंबनाचे नुकसान कमी करण्यासाठी, हवेचा दाब शक्य तितका कमी ठेवावा. वर्कपीस आणि नोजलमधील अंतर 10-20 सेमी राखले पाहिजे आणि फवारणीची पृष्ठभाग सामग्रीच्या प्रवाहाच्या दिशेने लंब ठेवली पाहिजे.
2. विसर्जन: वर्कपीस काही सेकंदांसाठी निलंबनामध्ये बुडवा, नंतर ते काढून टाका. या टप्प्यावर, निलंबनाचा एक थर वर्कपीसच्या पृष्ठभागावर चिकटून राहील आणि अतिरिक्त द्रव नैसर्गिकरित्या खाली वाहू शकतो. ही पद्धत लहान आकाराच्या वर्कपीससाठी योग्य आहे ज्यांना बाह्य पृष्ठभागावर संपूर्ण कोटिंग आवश्यक आहे.
3. घासणे: ब्रशिंगमध्ये पेंटब्रश किंवा ब्रश वापरून वर्कपीसच्या पृष्ठभागावर सस्पेंशन लागू करणे, एक कोटिंग तयार करणे समाविष्ट आहे. अरुंद पृष्ठभागांवर सामान्य स्थानिकीकृत कोटिंग किंवा एकल-बाजूच्या कोटिंगसाठी ब्रशिंग योग्य आहे. तथापि, कोटिंग सुकल्यानंतर परिणामी कमी गुळगुळीत आणि अगदी पृष्ठभागामुळे आणि कोटिंगच्या प्रत्येक थराच्या जाडीवर मर्यादा असल्यामुळे ते क्वचितच वापरले जाते.
4. ओतणे: निलंबन एका फिरत्या पोकळ वर्कपीसमध्ये घाला, आतील पृष्ठभाग निलंबनाने पूर्णपणे झाकलेले आहे याची खात्री करा. नंतर, कोटिंग तयार करण्यासाठी अतिरिक्त द्रव ओतणे. ही पद्धत लहान अणुभट्ट्या, पाइपलाइन, कोपर, वाल्व्ह, पंप कॅसिंग, टीज आणि इतर तत्सम वर्कपीस कोटिंगसाठी योग्य आहे.
मी मेटल वायरसाठी थर्माप्लास्टिक कोटिंग्ज शोधत आहे
ही इंटरनेट साइट माझ्या श्वासोच्छवासाची, खरोखर चांगली मांडणी आणि परिपूर्ण सामग्री आहे.
I think this is one of the so much important info for me. And i’m happy reading your article. But want to statement on few normal things, The site taste is perfect, the articles is in reality great : D. Good job, cheers