ਧਾਤ ਲਈ ਪਲਾਸਟਿਕ ਪਰਤ
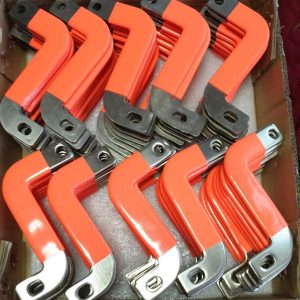
ਧਾਤ ਦੀ ਪ੍ਰਕਿਰਿਆ ਲਈ ਪਲਾਸਟਿਕ ਕੋਟਿੰਗ ਦਾ ਮਤਲਬ ਧਾਤ ਦੇ ਹਿੱਸਿਆਂ ਦੀ ਸਤ੍ਹਾ 'ਤੇ ਪਲਾਸਟਿਕ ਦੀ ਇੱਕ ਪਰਤ ਲਗਾਉਣਾ ਹੈ, ਜੋ ਉਹਨਾਂ ਨੂੰ ਧਾਤ ਦੀਆਂ ਮੂਲ ਵਿਸ਼ੇਸ਼ਤਾਵਾਂ ਨੂੰ ਬਰਕਰਾਰ ਰੱਖਣ ਦੀ ਇਜਾਜ਼ਤ ਦਿੰਦਾ ਹੈ ਅਤੇ ਪਲਾਸਟਿਕ ਦੀਆਂ ਕੁਝ ਵਿਸ਼ੇਸ਼ ਵਿਸ਼ੇਸ਼ਤਾਵਾਂ ਵੀ ਪ੍ਰਦਾਨ ਕਰਦਾ ਹੈ, ਜਿਵੇਂ ਕਿ ਖੋਰ ਪ੍ਰਤੀਰੋਧ, ਪਹਿਨਣ ਪ੍ਰਤੀਰੋਧ, ਇਲੈਕਟ੍ਰੀਕਲ ਇਨਸੂਲੇਸ਼ਨ, ਅਤੇ ਸਵੈ। - ਲੁਬਰੀਕੇਸ਼ਨ. ਇਹ ਪ੍ਰਕਿਰਿਆ ਉਤਪਾਦਾਂ ਦੀ ਐਪਲੀਕੇਸ਼ਨ ਸੀਮਾ ਨੂੰ ਵਧਾਉਣ ਅਤੇ ਉਹਨਾਂ ਦੇ ਆਰਥਿਕ ਮੁੱਲ ਨੂੰ ਵਧਾਉਣ ਵਿੱਚ ਬਹੁਤ ਮਹੱਤਵ ਰੱਖਦੀ ਹੈ।
ਧਾਤ ਲਈ ਪਲਾਸਟਿਕ ਪਰਤ ਲਈ ਢੰਗ
ਪਲਾਸਟਿਕ ਕੋਟਿੰਗ ਦੇ ਕਈ ਤਰੀਕੇ ਹਨ, ਜਿਸ ਵਿੱਚ ਫਲੇਮ ਸਪਰੇਅ, ਤਰਲ ਬਿਸਤਰਾ ਛਿੜਕਾਅ, ਪਾਊਡਰ ਇਲੈਕਟ੍ਰੋਸਟੈਟਿਕ ਛਿੜਕਾਅ, ਗਰਮ ਪਿਘਲਣ ਵਾਲੀ ਕੋਟਿੰਗ, ਅਤੇ ਸਸਪੈਂਸ਼ਨ ਕੋਟਿੰਗ। ਪਲਾਸਟਿਕ ਦੀਆਂ ਕਈ ਕਿਸਮਾਂ ਵੀ ਹਨ ਜੋ ਕੋਟਿੰਗ ਲਈ ਵਰਤੇ ਜਾ ਸਕਦੇ ਹਨ, ਨਾਲ PVC, PE, ਅਤੇ PA ਸਭ ਤੋਂ ਵੱਧ ਵਰਤੇ ਜਾਂਦੇ ਹਨ। ਕੋਟਿੰਗ ਲਈ ਵਰਤਿਆ ਜਾਣ ਵਾਲਾ ਪਲਾਸਟਿਕ ਪਾਊਡਰ ਦੇ ਰੂਪ ਵਿੱਚ ਹੋਣਾ ਚਾਹੀਦਾ ਹੈ, ਜਿਸਦੀ ਬਾਰੀਕਤਾ 80-120 ਜਾਲੀ ਹੈ।
ਕੋਟਿੰਗ ਤੋਂ ਬਾਅਦ, ਵਰਕਪੀਸ ਨੂੰ ਠੰਡੇ ਪਾਣੀ ਵਿੱਚ ਡੁਬੋ ਕੇ ਜਲਦੀ ਠੰਡਾ ਕਰਨਾ ਸਭ ਤੋਂ ਵਧੀਆ ਹੈ. ਰੈਪਿਡ ਕੂਲਿੰਗ ਪਲਾਸਟਿਕ ਕੋਟਿੰਗ ਦੀ ਕ੍ਰਿਸਟਲਿਨਿਟੀ ਨੂੰ ਘਟਾ ਸਕਦੀ ਹੈ, ਪਾਣੀ ਦੀ ਸਮਗਰੀ ਨੂੰ ਵਧਾ ਸਕਦੀ ਹੈ, ਕੋਟਿੰਗ ਦੀ ਕਠੋਰਤਾ ਅਤੇ ਸਤਹ ਦੀ ਚਮਕ ਨੂੰ ਸੁਧਾਰ ਸਕਦੀ ਹੈ, ਅਡੈਸ਼ਨ ਨੂੰ ਵਧਾ ਸਕਦੀ ਹੈ, ਅਤੇ ਅੰਦਰੂਨੀ ਤਣਾਅ ਦੇ ਕਾਰਨ ਕੋਟਿੰਗ ਨਿਰਲੇਪਤਾ ਨੂੰ ਦੂਰ ਕਰ ਸਕਦੀ ਹੈ।
ਕੋਟਿੰਗ ਅਤੇ ਬੇਸ ਮੈਟਲ ਦੇ ਵਿਚਕਾਰ ਚਿਪਕਣ ਨੂੰ ਬਿਹਤਰ ਬਣਾਉਣ ਲਈ, ਵਰਕਪੀਸ ਦੀ ਸਤਹ ਧੂੜ-ਮੁਕਤ ਅਤੇ ਸੁੱਕੀ ਹੋਣੀ ਚਾਹੀਦੀ ਹੈ, ਪਰਤ ਤੋਂ ਪਹਿਲਾਂ ਜੰਗਾਲ ਅਤੇ ਗਰੀਸ ਤੋਂ ਬਿਨਾਂ। ਜ਼ਿਆਦਾਤਰ ਮਾਮਲਿਆਂ ਵਿੱਚ, ਵਰਕਪੀਸ ਨੂੰ ਸਤਹ ਦੇ ਇਲਾਜ ਤੋਂ ਗੁਜ਼ਰਨਾ ਪੈਂਦਾ ਹੈ। ਇਲਾਜ ਦੇ ਤਰੀਕਿਆਂ ਵਿੱਚ ਸੈਂਡਬਲਾਸਟਿੰਗ, ਰਸਾਇਣਕ ਇਲਾਜ ਅਤੇ ਹੋਰ ਮਕੈਨੀਕਲ ਤਰੀਕੇ ਸ਼ਾਮਲ ਹਨ। ਉਹਨਾਂ ਵਿੱਚੋਂ, ਸੈਂਡਬਲਾਸਟਿੰਗ ਦੇ ਵਧੀਆ ਪ੍ਰਭਾਵ ਹੁੰਦੇ ਹਨ ਕਿਉਂਕਿ ਇਹ ਵਰਕਪੀਸ ਦੀ ਸਤ੍ਹਾ ਨੂੰ ਮੋਟਾ ਕਰਦਾ ਹੈ, ਸਤਹ ਦੇ ਖੇਤਰ ਨੂੰ ਵਧਾਉਂਦਾ ਹੈ ਅਤੇ ਹੁੱਕ ਬਣਾਉਂਦਾ ਹੈ, ਇਸ ਤਰ੍ਹਾਂ ਅਡਜਸ਼ਨ ਵਿੱਚ ਸੁਧਾਰ ਹੁੰਦਾ ਹੈ। ਸੈਂਡਬਲਾਸਟਿੰਗ ਤੋਂ ਬਾਅਦ, ਧੂੜ ਨੂੰ ਹਟਾਉਣ ਲਈ ਵਰਕਪੀਸ ਦੀ ਸਤ੍ਹਾ ਨੂੰ ਸਾਫ਼ ਕੰਪਰੈੱਸਡ ਹਵਾ ਨਾਲ ਉਡਾ ਦਿੱਤਾ ਜਾਣਾ ਚਾਹੀਦਾ ਹੈ, ਅਤੇ ਪਲਾਸਟਿਕ ਨੂੰ 6 ਘੰਟਿਆਂ ਦੇ ਅੰਦਰ ਕੋਟ ਕੀਤਾ ਜਾਣਾ ਚਾਹੀਦਾ ਹੈ, ਨਹੀਂ ਤਾਂ, ਸਤਹ ਆਕਸੀਡਾਈਜ਼ ਹੋ ਜਾਵੇਗੀ, ਪਰਤ ਦੇ ਅਨੁਕੂਲਨ ਨੂੰ ਪ੍ਰਭਾਵਤ ਕਰੇਗੀ।
ਫਾਇਦਾ
ਪਾਊਡਰ ਪਲਾਸਟਿਕ ਦੇ ਨਾਲ ਸਿੱਧੀ ਕੋਟਿੰਗ ਦੇ ਹੇਠ ਲਿਖੇ ਫਾਇਦੇ ਹਨ:
- ਇਹ ਰੈਜ਼ਿਨ ਨਾਲ ਵਰਤਿਆ ਜਾ ਸਕਦਾ ਹੈ ਜੋ ਸਿਰਫ ਪਾਊਡਰ ਦੇ ਰੂਪ ਵਿੱਚ ਉਪਲਬਧ ਹਨ.
- ਇੱਕ ਐਪਲੀਕੇਸ਼ਨ ਵਿੱਚ ਇੱਕ ਮੋਟੀ ਪਰਤ ਪ੍ਰਾਪਤ ਕੀਤੀ ਜਾ ਸਕਦੀ ਹੈ.
- ਗੁੰਝਲਦਾਰ ਆਕਾਰਾਂ ਜਾਂ ਤਿੱਖੇ ਕਿਨਾਰਿਆਂ ਵਾਲੇ ਉਤਪਾਦਾਂ ਨੂੰ ਚੰਗੀ ਤਰ੍ਹਾਂ ਕੋਟ ਕੀਤਾ ਜਾ ਸਕਦਾ ਹੈ।
- ਜ਼ਿਆਦਾਤਰ ਪਾਊਡਰ ਪਲਾਸਟਿਕ ਵਿੱਚ ਸ਼ਾਨਦਾਰ ਸਟੋਰੇਜ ਸਥਿਰਤਾ ਹੁੰਦੀ ਹੈ।
- ਕਿਸੇ ਘੋਲਨ ਦੀ ਲੋੜ ਨਹੀਂ ਹੈ, ਸਮੱਗਰੀ ਦੀ ਤਿਆਰੀ ਦੀ ਪ੍ਰਕਿਰਿਆ ਨੂੰ ਸਰਲ ਬਣਾਉਂਦੇ ਹੋਏ। ਹਾਲਾਂਕਿ, ਪਾਊਡਰ ਕੋਟਿੰਗ ਦੀਆਂ ਕੁਝ ਕਮੀਆਂ ਜਾਂ ਕਮੀਆਂ ਵੀ ਹਨ। ਉਦਾਹਰਨ ਲਈ, ਜੇਕਰ ਵਰਕਪੀਸ ਨੂੰ ਪਹਿਲਾਂ ਤੋਂ ਗਰਮ ਕਰਨ ਦੀ ਲੋੜ ਹੈ, ਤਾਂ ਇਸਦਾ ਆਕਾਰ ਸੀਮਤ ਹੋਵੇਗਾ। ਕਿਉਂਕਿ ਕੋਟਿੰਗ ਪ੍ਰਕਿਰਿਆ ਵਿੱਚ ਸਮਾਂ ਲੱਗਦਾ ਹੈ, ਵੱਡੇ ਆਕਾਰ ਦੇ ਵਰਕਪੀਸ ਲਈ, ਜਦੋਂ ਕਿ ਛਿੜਕਾਅ ਅਜੇ ਪੂਰਾ ਨਹੀਂ ਹੋਇਆ ਹੈ, ਕੁਝ ਖੇਤਰ ਪਹਿਲਾਂ ਹੀ ਲੋੜੀਂਦੇ ਤਾਪਮਾਨ ਤੋਂ ਹੇਠਾਂ ਠੰਢੇ ਹੋ ਗਏ ਹਨ। ਪਲਾਸਟਿਕ ਪਾਊਡਰ ਕੋਟਿੰਗ ਪ੍ਰਕਿਰਿਆ ਦੇ ਦੌਰਾਨ, ਪਾਊਡਰ ਦਾ ਨੁਕਸਾਨ 60% ਤੱਕ ਵੱਧ ਹੋ ਸਕਦਾ ਹੈ, ਇਸਲਈ ਆਰਥਿਕ ਲੋੜਾਂ ਨੂੰ ਪੂਰਾ ਕਰਨ ਲਈ ਇਸਨੂੰ ਇਕੱਠਾ ਕਰਨਾ ਅਤੇ ਦੁਬਾਰਾ ਵਰਤਿਆ ਜਾਣਾ ਚਾਹੀਦਾ ਹੈ।
ਫਲੇਮ ਸਪਰੇਅ
ਧਾਤ ਲਈ ਫਲੇਮ ਸਪਰੇਅ ਪਲਾਸਟਿਕ ਕੋਟਿੰਗ ਇੱਕ ਪ੍ਰਕਿਰਿਆ ਹੈ ਜਿਸ ਵਿੱਚ ਇੱਕ ਸਪਰੇਅ ਬੰਦੂਕ ਤੋਂ ਨਿਕਲਣ ਵਾਲੀ ਲਾਟ ਨਾਲ ਪਾਊਡਰ ਜਾਂ ਪੇਸਟ ਪਲਾਸਟਿਕ ਨੂੰ ਪਿਘਲਣਾ ਜਾਂ ਅੰਸ਼ਕ ਤੌਰ 'ਤੇ ਪਿਘਲਣਾ ਸ਼ਾਮਲ ਹੁੰਦਾ ਹੈ, ਅਤੇ ਫਿਰ ਪਿਘਲੇ ਹੋਏ ਪਲਾਸਟਿਕ ਨੂੰ ਇੱਕ ਪਲਾਸਟਿਕ ਕੋਟਿੰਗ ਬਣਾਉਣ ਲਈ ਕਿਸੇ ਵਸਤੂ ਦੀ ਸਤਹ 'ਤੇ ਛਿੜਕਣਾ ਸ਼ਾਮਲ ਹੁੰਦਾ ਹੈ। ਪਰਤ ਦੀ ਮੋਟਾਈ ਆਮ ਤੌਰ 'ਤੇ 0.1 ਅਤੇ 0.7 ਮਿਲੀਮੀਟਰ ਦੇ ਵਿਚਕਾਰ ਹੁੰਦੀ ਹੈ। ਲਾਟ ਦੇ ਛਿੜਕਾਅ ਲਈ ਪਾਊਡਰ ਪਲਾਸਟਿਕ ਦੀ ਵਰਤੋਂ ਕਰਦੇ ਸਮੇਂ, ਵਰਕਪੀਸ ਨੂੰ ਪਹਿਲਾਂ ਹੀ ਗਰਮ ਕੀਤਾ ਜਾਣਾ ਚਾਹੀਦਾ ਹੈ। ਪ੍ਰੀਹੀਟਿੰਗ ਇੱਕ ਓਵਨ ਵਿੱਚ ਕੀਤੀ ਜਾ ਸਕਦੀ ਹੈ, ਅਤੇ ਪ੍ਰੀਹੀਟਿੰਗ ਦਾ ਤਾਪਮਾਨ ਬਦਲਦਾ ਹੈ depeਪਲਾਸਟਿਕ ਦੇ ਛਿੜਕਾਅ ਦੀ ਕਿਸਮ 'ਤੇ nding.
ਛਿੜਕਾਅ ਦੌਰਾਨ ਲਾਟ ਦੇ ਤਾਪਮਾਨ ਨੂੰ ਸਖਤੀ ਨਾਲ ਨਿਯੰਤਰਿਤ ਕੀਤਾ ਜਾਣਾ ਚਾਹੀਦਾ ਹੈ, ਕਿਉਂਕਿ ਬਹੁਤ ਜ਼ਿਆਦਾ ਤਾਪਮਾਨ ਪਲਾਸਟਿਕ ਨੂੰ ਸਾੜ ਸਕਦਾ ਹੈ ਜਾਂ ਨੁਕਸਾਨ ਪਹੁੰਚਾ ਸਕਦਾ ਹੈ, ਜਦੋਂ ਕਿ ਬਹੁਤ ਘੱਟ ਤਾਪਮਾਨ ਅਨੁਕੂਲਨ ਨੂੰ ਪ੍ਰਭਾਵਤ ਕਰ ਸਕਦਾ ਹੈ। ਆਮ ਤੌਰ 'ਤੇ, ਪਲਾਸਟਿਕ ਦੀ ਪਹਿਲੀ ਪਰਤ ਦਾ ਛਿੜਕਾਅ ਕਰਦੇ ਸਮੇਂ ਤਾਪਮਾਨ ਸਭ ਤੋਂ ਵੱਧ ਹੁੰਦਾ ਹੈ, ਜੋ ਧਾਤ ਅਤੇ ਪਲਾਸਟਿਕ ਦੇ ਵਿਚਕਾਰ ਚਿਪਕਣ ਨੂੰ ਸੁਧਾਰ ਸਕਦਾ ਹੈ। ਜਿਵੇਂ ਕਿ ਅਗਲੀਆਂ ਪਰਤਾਂ ਦਾ ਛਿੜਕਾਅ ਕੀਤਾ ਜਾਂਦਾ ਹੈ, ਤਾਪਮਾਨ ਨੂੰ ਥੋੜ੍ਹਾ ਘੱਟ ਕੀਤਾ ਜਾ ਸਕਦਾ ਹੈ। ਸਪਰੇਅ ਬੰਦੂਕ ਅਤੇ ਵਰਕਪੀਸ ਵਿਚਕਾਰ ਦੂਰੀ 100 ਤੋਂ 200 ਸੈਂਟੀਮੀਟਰ ਦੇ ਵਿਚਕਾਰ ਹੋਣੀ ਚਾਹੀਦੀ ਹੈ। ਫਲੈਟ ਵਰਕਪੀਸ ਲਈ, ਵਰਕਪੀਸ ਨੂੰ ਖਿਤਿਜੀ ਤੌਰ 'ਤੇ ਰੱਖਿਆ ਜਾਣਾ ਚਾਹੀਦਾ ਹੈ ਅਤੇ ਸਪਰੇਅ ਬੰਦੂਕ ਨੂੰ ਅੱਗੇ ਅਤੇ ਪਿੱਛੇ ਹਿਲਾਇਆ ਜਾਣਾ ਚਾਹੀਦਾ ਹੈ; ਸਿਲੰਡਰ ਜਾਂ ਅੰਦਰੂਨੀ ਬੋਰ ਵਰਕਪੀਸ ਲਈ, ਉਹਨਾਂ ਨੂੰ ਰੋਟੇਸ਼ਨਲ ਸਪਰੇਅ ਕਰਨ ਲਈ ਖਰਾਦ 'ਤੇ ਮਾਊਂਟ ਕੀਤਾ ਜਾਣਾ ਚਾਹੀਦਾ ਹੈ। ਰੋਟੇਟਿੰਗ ਵਰਕਪੀਸ ਦੀ ਰੇਖਿਕ ਗਤੀ 20 ਅਤੇ 60 ਮੀਟਰ/ਮਿੰਟ ਦੇ ਵਿਚਕਾਰ ਹੋਣੀ ਚਾਹੀਦੀ ਹੈ। ਕੋਟਿੰਗ ਦੀ ਲੋੜੀਂਦੀ ਮੋਟਾਈ ਪ੍ਰਾਪਤ ਕਰਨ ਤੋਂ ਬਾਅਦ, ਛਿੜਕਾਅ ਨੂੰ ਰੋਕ ਦੇਣਾ ਚਾਹੀਦਾ ਹੈ ਅਤੇ ਵਰਕਪੀਸ ਨੂੰ ਘੁਮਾਉਣਾ ਜਾਰੀ ਰੱਖਣਾ ਚਾਹੀਦਾ ਹੈ ਜਦੋਂ ਤੱਕ ਪਿਘਲੇ ਹੋਏ ਪਲਾਸਟਿਕ ਦੇ ਠੋਸ ਨਹੀਂ ਹੋ ਜਾਂਦੇ, ਅਤੇ ਫਿਰ ਇਸਨੂੰ ਤੇਜ਼ੀ ਨਾਲ ਠੰਢਾ ਕੀਤਾ ਜਾਣਾ ਚਾਹੀਦਾ ਹੈ।
ਹਾਲਾਂਕਿ ਫਲੇਮ ਸਪਰੇਅ ਵਿੱਚ ਮੁਕਾਬਲਤਨ ਘੱਟ ਉਤਪਾਦਨ ਕੁਸ਼ਲਤਾ ਹੈ ਅਤੇ ਇਸ ਵਿੱਚ ਜਲਣ ਵਾਲੀਆਂ ਗੈਸਾਂ ਦੀ ਵਰਤੋਂ ਸ਼ਾਮਲ ਹੈ, ਇਹ ਅਜੇ ਵੀ ਉਦਯੋਗ ਵਿੱਚ ਇੱਕ ਮਹੱਤਵਪੂਰਨ ਪ੍ਰੋਸੈਸਿੰਗ ਵਿਧੀ ਹੈ ਕਿਉਂਕਿ ਇਸਦੇ ਘੱਟ ਸਾਜ਼ੋ-ਸਾਮਾਨ ਦੇ ਨਿਵੇਸ਼ ਅਤੇ ਟੈਂਕਾਂ, ਕੰਟੇਨਰਾਂ ਅਤੇ ਵੱਡੇ ਵਰਕਪੀਸ ਦੇ ਅੰਦਰਲੇ ਹਿੱਸੇ ਨੂੰ ਹੋਰ ਤਰੀਕਿਆਂ ਦੇ ਮੁਕਾਬਲੇ ਕੋਟਿੰਗ ਕਰਨ ਵਿੱਚ ਪ੍ਰਭਾਵਸ਼ੀਲਤਾ ਹੈ। .
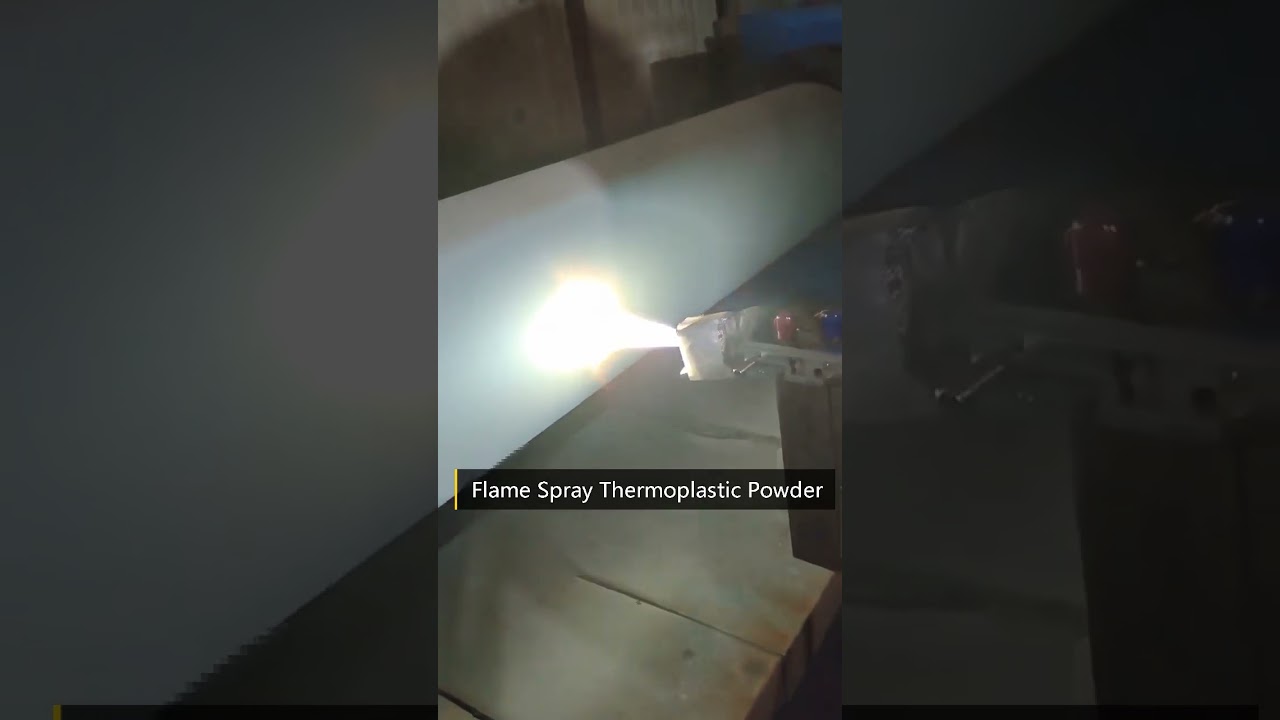
ਤਰਲ-ਬੈੱਡ ਡਿਪ ਪਲਾਸਟਿਕ ਕੋਟਿੰਗ
ਧਾਤੂ ਲਈ ਤਰਲ ਬੈੱਡ ਡਿਪ ਪਲਾਸਟਿਕ ਕੋਟਿੰਗ ਦਾ ਕੰਮ ਕਰਨ ਦਾ ਸਿਧਾਂਤ ਇਸ ਤਰ੍ਹਾਂ ਹੈ: ਪਲਾਸਟਿਕ ਕੋਟਿੰਗ ਪਾਊਡਰ ਨੂੰ ਇੱਕ ਸਿਲੰਡਰ ਕੰਟੇਨਰ ਵਿੱਚ ਰੱਖਿਆ ਜਾਂਦਾ ਹੈ ਜਿਸ ਵਿੱਚ ਸਿਖਰ 'ਤੇ ਇੱਕ ਪੋਰਸ ਪਾਰਟੀਸ਼ਨ ਹੁੰਦਾ ਹੈ ਜੋ ਸਿਰਫ ਹਵਾ ਨੂੰ ਲੰਘਣ ਦਿੰਦਾ ਹੈ, ਪਾਊਡਰ ਨੂੰ ਨਹੀਂ। ਜਦੋਂ ਕੰਟੇਨਰ ਦੇ ਤਲ ਤੋਂ ਕੰਪਰੈੱਸਡ ਹਵਾ ਦਾਖਲ ਹੁੰਦੀ ਹੈ, ਤਾਂ ਇਹ ਪਾਊਡਰ ਨੂੰ ਉਡਾ ਦਿੰਦੀ ਹੈ ਅਤੇ ਇਸ ਨੂੰ ਕੰਟੇਨਰ ਵਿੱਚ ਮੁਅੱਤਲ ਕਰ ਦਿੰਦੀ ਹੈ। ਜੇਕਰ ਪਹਿਲਾਂ ਤੋਂ ਗਰਮ ਕੀਤੇ ਵਰਕਪੀਸ ਨੂੰ ਇਸ ਵਿੱਚ ਡੁਬੋਇਆ ਜਾਂਦਾ ਹੈ, ਤਾਂ ਰਾਲ ਪਾਊਡਰ ਪਿਘਲ ਜਾਵੇਗਾ ਅਤੇ ਵਰਕਪੀਸ ਦੇ ਨਾਲ ਚਿਪਕ ਜਾਵੇਗਾ, ਇੱਕ ਪਰਤ ਬਣ ਜਾਵੇਗਾ।
ਤਰਲ ਬਿਸਤਰੇ ਵਿੱਚ ਪ੍ਰਾਪਤ ਕੋਟਿੰਗ ਦੀ ਮੋਟਾਈ depeਤਾਪਮਾਨ 'ਤੇ nds, ਖਾਸ ਤਾਪ ਸਮਰੱਥਾ, ਸਤਹ ਗੁਣਾਂਕ, ਸਪਰੇਅ ਦਾ ਸਮਾਂ, ਅਤੇ ਵਰਕਪੀਸ ਤਰਲ ਚੈਂਬਰ ਵਿੱਚ ਦਾਖਲ ਹੋਣ 'ਤੇ ਵਰਤੇ ਗਏ ਪਲਾਸਟਿਕ ਦੀ ਕਿਸਮ। ਹਾਲਾਂਕਿ, ਪ੍ਰਕਿਰਿਆ ਵਿੱਚ ਵਰਕਪੀਸ ਦੇ ਸਿਰਫ ਤਾਪਮਾਨ ਅਤੇ ਸਪਰੇਅ ਦੇ ਸਮੇਂ ਨੂੰ ਨਿਯੰਤਰਿਤ ਕੀਤਾ ਜਾ ਸਕਦਾ ਹੈ, ਅਤੇ ਉਹਨਾਂ ਨੂੰ ਉਤਪਾਦਨ ਵਿੱਚ ਪ੍ਰਯੋਗਾਂ ਦੁਆਰਾ ਨਿਰਧਾਰਤ ਕਰਨ ਦੀ ਲੋੜ ਹੁੰਦੀ ਹੈ।
ਡੁਬੋਣ ਦੇ ਦੌਰਾਨ, ਇਹ ਜ਼ਰੂਰੀ ਹੁੰਦਾ ਹੈ ਕਿ ਪਲਾਸਟਿਕ ਪਾਊਡਰ ਆਸਾਨੀ ਨਾਲ ਅਤੇ ਸਮਾਨ ਰੂਪ ਵਿੱਚ ਵਹਿੰਦਾ ਹੋਵੇ, ਬਿਨਾਂ ਇਕੱਠਾ ਹੋਣ, ਵੌਰਟੈਕਸ ਵਹਾਅ, ਜਾਂ ਪਲਾਸਟਿਕ ਦੇ ਕਣਾਂ ਦੇ ਬਹੁਤ ਜ਼ਿਆਦਾ ਫੈਲਣ ਤੋਂ ਬਿਨਾਂ। ਇਹਨਾਂ ਲੋੜਾਂ ਨੂੰ ਪੂਰਾ ਕਰਨ ਲਈ ਅਨੁਸਾਰੀ ਉਪਾਅ ਕੀਤੇ ਜਾਣੇ ਚਾਹੀਦੇ ਹਨ. ਹਲਚਲ ਕਰਨ ਵਾਲੇ ਯੰਤਰ ਨੂੰ ਜੋੜਨ ਨਾਲ ਸੰਗ੍ਰਹਿ ਅਤੇ ਵੌਰਟੇਕਸ ਦੇ ਪ੍ਰਵਾਹ ਨੂੰ ਘਟਾਇਆ ਜਾ ਸਕਦਾ ਹੈ, ਜਦੋਂ ਕਿ ਪਲਾਸਟਿਕ ਪਾਊਡਰ ਵਿੱਚ ਥੋੜੀ ਜਿਹੀ ਮਾਤਰਾ ਵਿੱਚ ਟੈਲਕਮ ਪਾਊਡਰ ਜੋੜਨਾ ਤਰਲੀਕਰਨ ਲਈ ਫਾਇਦੇਮੰਦ ਹੁੰਦਾ ਹੈ, ਪਰ ਇਹ ਕੋਟਿੰਗ ਦੀ ਗੁਣਵੱਤਾ ਨੂੰ ਪ੍ਰਭਾਵਿਤ ਕਰ ਸਕਦਾ ਹੈ। ਪਲਾਸਟਿਕ ਦੇ ਕਣਾਂ ਦੇ ਫੈਲਾਅ ਨੂੰ ਰੋਕਣ ਲਈ, ਪਲਾਸਟਿਕ ਪਾਊਡਰ ਕਣਾਂ ਦੀ ਹਵਾ ਦੇ ਪ੍ਰਵਾਹ ਦੀ ਦਰ ਅਤੇ ਇਕਸਾਰਤਾ ਨੂੰ ਸਖਤੀ ਨਾਲ ਨਿਯੰਤਰਿਤ ਕੀਤਾ ਜਾਣਾ ਚਾਹੀਦਾ ਹੈ। ਹਾਲਾਂਕਿ, ਕੁਝ ਫੈਲਾਅ ਅਟੱਲ ਹੈ, ਇਸ ਲਈ ਤਰਲ ਵਾਲੇ ਬਿਸਤਰੇ ਦੇ ਉੱਪਰਲੇ ਹਿੱਸੇ ਵਿੱਚ ਇੱਕ ਰਿਕਵਰੀ ਯੰਤਰ ਸਥਾਪਤ ਕੀਤਾ ਜਾਣਾ ਚਾਹੀਦਾ ਹੈ।
ਤਰਲ ਬੈੱਡ ਡਿਪ ਪਲਾਸਟਿਕ ਕੋਟਿੰਗ ਦੇ ਫਾਇਦੇ ਗੁੰਝਲਦਾਰ-ਆਕਾਰ ਦੇ ਵਰਕਪੀਸ ਨੂੰ ਕੋਟ ਕਰਨ ਦੀ ਸਮਰੱਥਾ, ਉੱਚ ਕੋਟਿੰਗ ਦੀ ਗੁਣਵੱਤਾ, ਇੱਕ ਐਪਲੀਕੇਸ਼ਨ ਵਿੱਚ ਇੱਕ ਮੋਟੀ ਪਰਤ ਪ੍ਰਾਪਤ ਕਰਨਾ, ਘੱਟ ਤੋਂ ਘੱਟ ਰਾਲ ਦਾ ਨੁਕਸਾਨ, ਅਤੇ ਇੱਕ ਸਾਫ਼ ਕੰਮ ਕਰਨ ਵਾਲਾ ਵਾਤਾਵਰਣ ਹੈ। ਨੁਕਸਾਨ ਵੱਡੇ ਵਰਕਪੀਸ ਦੀ ਪ੍ਰਕਿਰਿਆ ਕਰਨ ਦੀ ਮੁਸ਼ਕਲ ਹੈ.
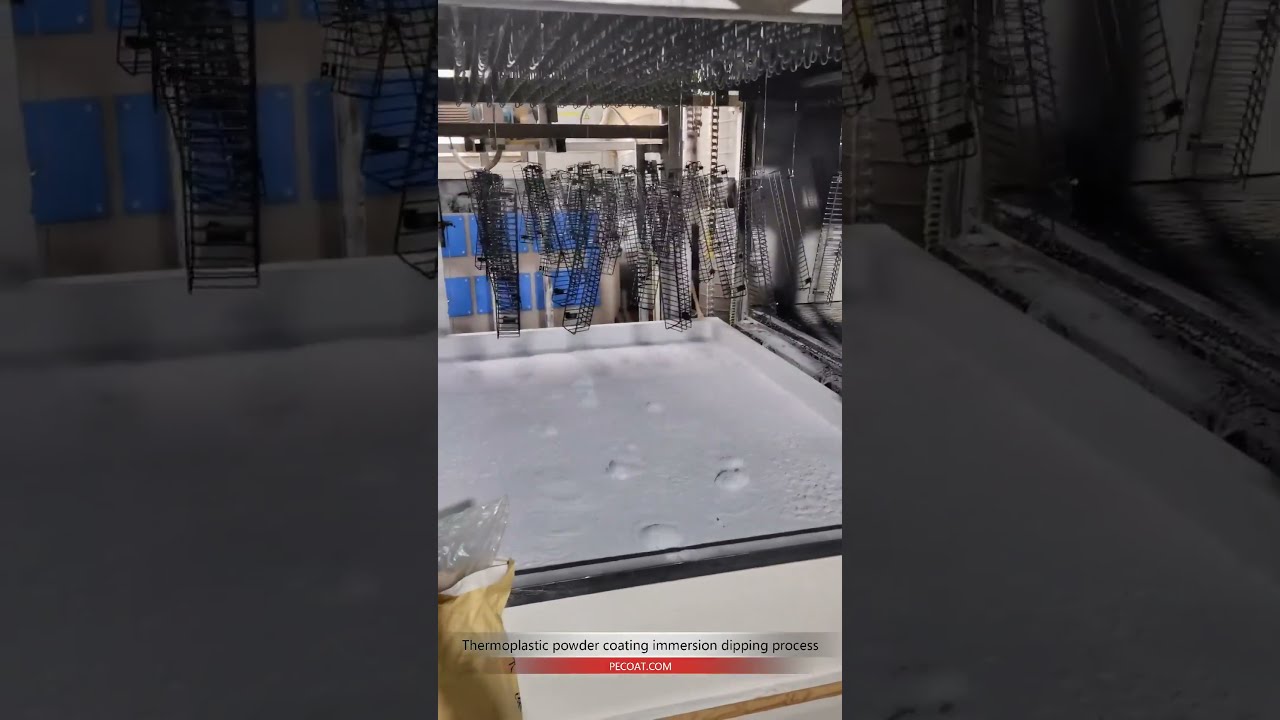
ਧਾਤ ਲਈ ਇਲੈਕਟ੍ਰੋਸਟੈਟਿਕ ਛਿੜਕਾਅ ਪਲਾਸਟਿਕ ਪਰਤ
ਇਲੈਕਟ੍ਰੋਸਟੈਟਿਕ ਸਪਰੇਅ ਵਿੱਚ, ਰਾਲ ਪਲਾਸਟਿਕ ਕੋਟਿੰਗ ਪਾਊਡਰ ਨੂੰ ਪਿਘਲਣ ਜਾਂ ਸਿੰਟਰਿੰਗ ਦੀ ਬਜਾਏ ਇਲੈਕਟ੍ਰੋਸਟੈਟਿਕ ਫੋਰਸ ਦੁਆਰਾ ਵਰਕਪੀਸ ਦੀ ਸਤਹ 'ਤੇ ਸਥਿਰ ਕੀਤਾ ਜਾਂਦਾ ਹੈ। ਸਿਧਾਂਤ ਇੱਕ ਉੱਚ-ਵੋਲਟੇਜ ਇਲੈਕਟ੍ਰੋਸਟੈਟਿਕ ਜਨਰੇਟਰ ਦੁਆਰਾ ਬਣਾਏ ਗਏ ਇਲੈਕਟ੍ਰੋਸਟੈਟਿਕ ਫੀਲਡ ਨੂੰ ਸਥਿਰ ਬਿਜਲੀ ਨਾਲ ਸਪਰੇਅ ਗਨ ਤੋਂ ਸਪਰੇਅ ਕੀਤੇ ਰਾਲ ਪਾਊਡਰ ਨੂੰ ਚਾਰਜ ਕਰਨ ਲਈ ਵਰਤਣਾ ਹੈ, ਅਤੇ ਜ਼ਮੀਨੀ ਵਰਕਪੀਸ ਉੱਚ-ਵੋਲਟੇਜ ਸਕਾਰਾਤਮਕ ਇਲੈਕਟ੍ਰੋਡ ਬਣ ਜਾਂਦੀ ਹੈ। ਨਤੀਜੇ ਵਜੋਂ, ਵਰਕਪੀਸ ਦੀ ਸਤ੍ਹਾ 'ਤੇ ਇਕਸਾਰ ਪਲਾਸਟਿਕ ਪਾਊਡਰ ਦੀ ਇੱਕ ਪਰਤ ਤੇਜ਼ੀ ਨਾਲ ਜਮ੍ਹਾਂ ਹੋ ਜਾਂਦੀ ਹੈ। ਚਾਰਜ ਦੇ ਖ਼ਤਮ ਹੋਣ ਤੋਂ ਪਹਿਲਾਂ, ਪਾਊਡਰ ਪਰਤ ਮਜ਼ਬੂਤੀ ਨਾਲ ਚਿਪਕ ਜਾਂਦੀ ਹੈ। ਹੀਟਿੰਗ ਅਤੇ ਕੂਲਿੰਗ ਤੋਂ ਬਾਅਦ, ਇੱਕ ਸਮਾਨ ਪਲਾਸਟਿਕ ਕੋਟਿੰਗ ਪ੍ਰਾਪਤ ਕੀਤੀ ਜਾ ਸਕਦੀ ਹੈ.
ਪਾਊਡਰ ਇਲੈਕਟ੍ਰੋਸਟੈਟਿਕ ਛਿੜਕਾਅ 1960 ਦੇ ਦਹਾਕੇ ਦੇ ਮੱਧ ਵਿੱਚ ਵਿਕਸਤ ਕੀਤਾ ਗਿਆ ਸੀ ਅਤੇ ਸਵੈਚਲਿਤ ਕਰਨਾ ਆਸਾਨ ਹੈ। ਜੇ ਕੋਟਿੰਗ ਨੂੰ ਮੋਟਾ ਹੋਣ ਦੀ ਲੋੜ ਨਹੀਂ ਹੈ, ਤਾਂ ਇਲੈਕਟ੍ਰੋਸਟੈਟਿਕ ਛਿੜਕਾਅ ਲਈ ਵਰਕਪੀਸ ਨੂੰ ਪਹਿਲਾਂ ਤੋਂ ਗਰਮ ਕਰਨ ਦੀ ਲੋੜ ਨਹੀਂ ਹੈ, ਇਸਲਈ ਇਸਨੂੰ ਗਰਮੀ-ਸੰਵੇਦਨਸ਼ੀਲ ਸਮੱਗਰੀ ਜਾਂ ਵਰਕਪੀਸ ਲਈ ਵਰਤਿਆ ਜਾ ਸਕਦਾ ਹੈ ਜੋ ਹੀਟਿੰਗ ਲਈ ਢੁਕਵੇਂ ਨਹੀਂ ਹਨ। ਇਸ ਨੂੰ ਇੱਕ ਵੱਡੇ ਸਟੋਰੇਜ਼ ਕੰਟੇਨਰ ਦੀ ਵੀ ਲੋੜ ਨਹੀਂ ਹੈ, ਜੋ ਕਿ ਤਰਲ ਬਿਸਤਰੇ ਦੇ ਛਿੜਕਾਅ ਵਿੱਚ ਜ਼ਰੂਰੀ ਹੈ। ਵਰਕਪੀਸ ਨੂੰ ਬਾਈਪਾਸ ਕਰਨ ਵਾਲਾ ਪਾਊਡਰ ਵਰਕਪੀਸ ਦੇ ਪਿਛਲੇ ਪਾਸੇ ਖਿੱਚਿਆ ਜਾਂਦਾ ਹੈ, ਇਸਲਈ ਓਵਰਸਪ੍ਰੇ ਦੀ ਮਾਤਰਾ ਹੋਰ ਛਿੜਕਾਅ ਦੇ ਤਰੀਕਿਆਂ ਨਾਲੋਂ ਬਹੁਤ ਘੱਟ ਹੁੰਦੀ ਹੈ, ਅਤੇ ਪੂਰੇ ਵਰਕਪੀਸ ਨੂੰ ਇੱਕ ਪਾਸੇ ਸਪਰੇਅ ਕਰਕੇ ਕੋਟ ਕੀਤਾ ਜਾ ਸਕਦਾ ਹੈ। ਹਾਲਾਂਕਿ, ਵੱਡੇ ਵਰਕਪੀਸ ਨੂੰ ਅਜੇ ਵੀ ਦੋਵਾਂ ਪਾਸਿਆਂ ਤੋਂ ਸਪਰੇਅ ਕਰਨ ਦੀ ਲੋੜ ਹੈ।
ਵੱਖ-ਵੱਖ ਕਰਾਸ-ਸੈਕਸ਼ਨਾਂ ਵਾਲੇ ਵਰਕਪੀਸ ਬਾਅਦ ਦੇ ਹੀਟਿੰਗ ਲਈ ਮੁਸ਼ਕਲਾਂ ਪੈਦਾ ਕਰ ਸਕਦੇ ਹਨ। ਜੇ ਕਰਾਸ-ਸੈਕਸ਼ਨ ਵਿੱਚ ਅੰਤਰ ਬਹੁਤ ਵੱਡਾ ਹੈ, ਤਾਂ ਕੋਟਿੰਗ ਦਾ ਮੋਟਾ ਹਿੱਸਾ ਪਿਘਲਣ ਦੇ ਤਾਪਮਾਨ ਤੱਕ ਨਹੀਂ ਪਹੁੰਚ ਸਕਦਾ ਹੈ, ਜਦੋਂ ਕਿ ਪਤਲਾ ਹਿੱਸਾ ਪਹਿਲਾਂ ਹੀ ਪਿਘਲਿਆ ਜਾਂ ਘਟਿਆ ਹੋ ਸਕਦਾ ਹੈ। ਇਸ ਕੇਸ ਵਿੱਚ, ਰਾਲ ਦੀ ਥਰਮਲ ਸਥਿਰਤਾ ਮਹੱਤਵਪੂਰਨ ਹੈ.
ਸਾਫ਼-ਸੁਥਰੇ ਅੰਦਰੂਨੀ ਕੋਨੇ ਅਤੇ ਡੂੰਘੇ ਛੇਕ ਵਾਲੇ ਹਿੱਸੇ ਇਲੈਕਟ੍ਰੋਸਟੈਟਿਕ ਛਿੜਕਾਅ ਦੁਆਰਾ ਆਸਾਨੀ ਨਾਲ ਢੱਕੇ ਨਹੀਂ ਜਾਂਦੇ ਕਿਉਂਕਿ ਇਹਨਾਂ ਖੇਤਰਾਂ ਵਿੱਚ ਇਲੈਕਟ੍ਰੋਸਟੈਟਿਕ ਸ਼ੀਲਡਿੰਗ ਅਤੇ ਆਰ.epel ਪਾਊਡਰ, ਪਰਤ ਨੂੰ ਕੋਨਿਆਂ ਜਾਂ ਛੇਕਾਂ ਵਿੱਚ ਦਾਖਲ ਹੋਣ ਤੋਂ ਰੋਕਦਾ ਹੈ ਜਦੋਂ ਤੱਕ ਕਿ ਸਪਰੇਅ ਬੰਦੂਕ ਉਹਨਾਂ ਵਿੱਚ ਨਹੀਂ ਪਾਈ ਜਾ ਸਕਦੀ। ਇਸ ਤੋਂ ਇਲਾਵਾ, ਇਲੈਕਟ੍ਰੋਸਟੈਟਿਕ ਛਿੜਕਾਅ ਲਈ ਬਾਰੀਕ ਕਣਾਂ ਦੀ ਲੋੜ ਹੁੰਦੀ ਹੈ ਕਿਉਂਕਿ ਵੱਡੇ ਕਣਾਂ ਦੇ ਵਰਕਪੀਸ ਤੋਂ ਵੱਖ ਹੋਣ ਦੀ ਜ਼ਿਆਦਾ ਸੰਭਾਵਨਾ ਹੁੰਦੀ ਹੈ, ਅਤੇ 150 ਮੈਸ਼ ਤੋਂ ਬਾਰੀਕ ਕਣ ਇਲੈਕਟ੍ਰੋਸਟੈਟਿਕ ਕਾਰਵਾਈ ਵਿੱਚ ਵਧੇਰੇ ਪ੍ਰਭਾਵਸ਼ਾਲੀ ਹੁੰਦੇ ਹਨ।
ਗਰਮ ਪਿਘਲ ਪਰਤ ਵਿਧੀ
ਗਰਮ ਪਿਘਲਣ ਵਾਲੀ ਕੋਟਿੰਗ ਵਿਧੀ ਦਾ ਕਾਰਜਸ਼ੀਲ ਸਿਧਾਂਤ ਇੱਕ ਸਪਰੇਅ ਬੰਦੂਕ ਦੀ ਵਰਤੋਂ ਕਰਕੇ ਪਲਾਸਟਿਕ ਕੋਟਿੰਗ ਪਾਊਡਰ ਨੂੰ ਪਹਿਲਾਂ ਤੋਂ ਗਰਮ ਕੀਤੇ ਵਰਕਪੀਸ ਉੱਤੇ ਸਪਰੇਅ ਕਰਨਾ ਹੈ। ਵਰਕਪੀਸ ਦੀ ਗਰਮੀ ਦੀ ਵਰਤੋਂ ਕਰਕੇ ਪਲਾਸਟਿਕ ਪਿਘਲ ਜਾਂਦਾ ਹੈ, ਅਤੇ ਠੰਢਾ ਹੋਣ ਤੋਂ ਬਾਅਦ, ਵਰਕਪੀਸ 'ਤੇ ਪਲਾਸਟਿਕ ਦੀ ਪਰਤ ਲਗਾਈ ਜਾ ਸਕਦੀ ਹੈ। ਜੇ ਜਰੂਰੀ ਹੋਵੇ, ਤਾਂ ਹੀਟਿੰਗ ਤੋਂ ਬਾਅਦ ਦੇ ਇਲਾਜ ਦੀ ਵੀ ਲੋੜ ਹੁੰਦੀ ਹੈ.
ਗਰਮ ਪਿਘਲਣ ਵਾਲੀ ਪਰਤ ਦੀ ਪ੍ਰਕਿਰਿਆ ਨੂੰ ਨਿਯੰਤਰਿਤ ਕਰਨ ਦੀ ਕੁੰਜੀ ਵਰਕਪੀਸ ਦਾ ਪ੍ਰੀਹੀਟਿੰਗ ਤਾਪਮਾਨ ਹੈ। ਜਦੋਂ ਪ੍ਰੀਹੀਟਿੰਗ ਦਾ ਤਾਪਮਾਨ ਬਹੁਤ ਜ਼ਿਆਦਾ ਹੁੰਦਾ ਹੈ, ਤਾਂ ਇਹ ਧਾਤ ਦੀ ਸਤ੍ਹਾ ਦੇ ਗੰਭੀਰ ਆਕਸੀਕਰਨ ਦਾ ਕਾਰਨ ਬਣ ਸਕਦਾ ਹੈ, ਪਰਤ ਦੀ ਅਸੰਭਵਤਾ ਨੂੰ ਘਟਾ ਸਕਦਾ ਹੈ, ਅਤੇ ਕੋਟਿੰਗ ਦੇ ਰਾਲ ਦੇ ਸੜਨ ਅਤੇ ਫੋਮਿੰਗ ਜਾਂ ਰੰਗੀਨ ਹੋਣ ਦਾ ਕਾਰਨ ਵੀ ਬਣ ਸਕਦਾ ਹੈ। ਜਦੋਂ ਪ੍ਰੀਹੀਟਿੰਗ ਦਾ ਤਾਪਮਾਨ ਬਹੁਤ ਘੱਟ ਹੁੰਦਾ ਹੈ, ਤਾਂ ਰਾਲ ਦੀ ਵਹਾਅ ਘੱਟ ਹੁੰਦੀ ਹੈ, ਜਿਸ ਨਾਲ ਇਕਸਾਰ ਪਰਤ ਪ੍ਰਾਪਤ ਕਰਨਾ ਮੁਸ਼ਕਲ ਹੋ ਜਾਂਦਾ ਹੈ। ਅਕਸਰ, ਗਰਮ ਪਿਘਲਣ ਵਾਲੀ ਪਰਤ ਵਿਧੀ ਦਾ ਇੱਕ ਸਿੰਗਲ ਸਪਰੇਅ ਲੋੜੀਂਦੀ ਮੋਟਾਈ ਪ੍ਰਾਪਤ ਨਹੀਂ ਕਰ ਸਕਦਾ, ਇਸਲਈ ਕਈ ਸਪਰੇਅ ਐਪਲੀਕੇਸ਼ਨਾਂ ਦੀ ਲੋੜ ਹੁੰਦੀ ਹੈ। ਹਰੇਕ ਸਪਰੇਅ ਦੀ ਵਰਤੋਂ ਤੋਂ ਬਾਅਦ, ਦੂਜੀ ਪਰਤ ਨੂੰ ਲਾਗੂ ਕਰਨ ਤੋਂ ਪਹਿਲਾਂ ਪਰਤ ਨੂੰ ਪੂਰੀ ਤਰ੍ਹਾਂ ਪਿਘਲਣ ਅਤੇ ਚਮਕਦਾਰ ਬਣਾਉਣ ਲਈ ਹੀਟਿੰਗ ਟ੍ਰੀਟਮੈਂਟ ਜ਼ਰੂਰੀ ਹੈ। ਇਹ ਨਾ ਸਿਰਫ਼ ਇੱਕ ਸਮਾਨ ਅਤੇ ਨਿਰਵਿਘਨ ਪਰਤ ਨੂੰ ਯਕੀਨੀ ਬਣਾਉਂਦਾ ਹੈ ਬਲਕਿ ਮਕੈਨੀਕਲ ਤਾਕਤ ਵਿੱਚ ਵੀ ਮਹੱਤਵਪੂਰਨ ਸੁਧਾਰ ਕਰਦਾ ਹੈ। ਉੱਚ-ਘਣਤਾ ਵਾਲੀ ਪੋਲੀਥੀਲੀਨ ਲਈ ਸਿਫਾਰਿਸ਼ ਕੀਤਾ ਗਿਆ ਹੀਟਿੰਗ ਟ੍ਰੀਟਮੈਂਟ ਤਾਪਮਾਨ ਲਗਭਗ 170 ਡਿਗਰੀ ਸੈਲਸੀਅਸ ਹੈ, ਅਤੇ ਕਲੋਰੀਨੇਟਿਡ ਪੋਲੀਥਰ ਲਈ, ਇਹ 200 ਡਿਗਰੀ ਸੈਲਸੀਅਸ ਦੇ ਆਸ-ਪਾਸ ਹੈ, 1 ਘੰਟੇ ਦੇ ਸਿਫ਼ਾਰਸ਼ ਕੀਤੇ ਸਮੇਂ ਦੇ ਨਾਲ।
ਗਰਮ ਪਿਘਲਣ ਵਾਲੀ ਕੋਟਿੰਗ ਵਿਧੀ ਘੱਟੋ-ਘੱਟ ਰਾਲ ਦੇ ਨੁਕਸਾਨ ਦੇ ਨਾਲ ਉੱਚ-ਗੁਣਵੱਤਾ, ਸੁਹਜ ਪੱਖੋਂ ਪ੍ਰਸੰਨ, ਜ਼ੋਰਦਾਰ ਬੰਧਨ ਵਾਲੀਆਂ ਕੋਟਿੰਗਾਂ ਪੈਦਾ ਕਰਦੀ ਹੈ। ਇਸ ਨੂੰ ਨਿਯੰਤਰਿਤ ਕਰਨਾ ਆਸਾਨ ਹੈ, ਇਸਦੀ ਗੰਧ ਘੱਟ ਹੈ, ਅਤੇ ਵਰਤੀ ਗਈ ਸਪਰੇਅ ਬੰਦੂਕ ਵੀ ਕਰਦੀ ਹੈ।
ਧਾਤ ਲਈ ਪਲਾਸਟਿਕ ਕੋਟਿੰਗ ਲਈ ਉਪਲਬਧ ਹੋਰ ਤਰੀਕੇ
1. ਛਿੜਕਾਅ: ਸਸਪੈਂਸ਼ਨ ਨੂੰ ਸਪਰੇਅ ਗਨ ਭੰਡਾਰ ਵਿੱਚ ਭਰੋ ਅਤੇ ਵਰਕਪੀਸ ਦੀ ਸਤ੍ਹਾ 'ਤੇ ਕੋਟਿੰਗ ਨੂੰ ਸਮਾਨ ਰੂਪ ਵਿੱਚ ਸਪਰੇਅ ਕਰਨ ਲਈ 0.1 MPa ਤੋਂ ਵੱਧ ਨਾ ਹੋਣ ਵਾਲੇ ਗੇਜ ਪ੍ਰੈਸ਼ਰ ਨਾਲ ਕੰਪਰੈੱਸਡ ਹਵਾ ਦੀ ਵਰਤੋਂ ਕਰੋ। ਮੁਅੱਤਲ ਦੇ ਨੁਕਸਾਨ ਨੂੰ ਘੱਟ ਕਰਨ ਲਈ, ਹਵਾ ਦੇ ਦਬਾਅ ਨੂੰ ਜਿੰਨਾ ਸੰਭਵ ਹੋ ਸਕੇ ਘੱਟ ਰੱਖਿਆ ਜਾਣਾ ਚਾਹੀਦਾ ਹੈ। ਵਰਕਪੀਸ ਅਤੇ ਨੋਜ਼ਲ ਵਿਚਕਾਰ ਦੂਰੀ 10-20 ਸੈਂਟੀਮੀਟਰ 'ਤੇ ਬਣਾਈ ਰੱਖੀ ਜਾਣੀ ਚਾਹੀਦੀ ਹੈ, ਅਤੇ ਛਿੜਕਾਅ ਵਾਲੀ ਸਤਹ ਨੂੰ ਸਮੱਗਰੀ ਦੇ ਵਹਾਅ ਦੀ ਦਿਸ਼ਾ ਲਈ ਲੰਬਵਤ ਰੱਖਿਆ ਜਾਣਾ ਚਾਹੀਦਾ ਹੈ।
2. ਇਮਰਸ਼ਨ: ਵਰਕਪੀਸ ਨੂੰ ਕੁਝ ਸਕਿੰਟਾਂ ਲਈ ਸਸਪੈਂਸ਼ਨ ਵਿੱਚ ਡੁਬੋ ਦਿਓ, ਫਿਰ ਇਸਨੂੰ ਹਟਾਓ। ਇਸ ਬਿੰਦੂ 'ਤੇ, ਮੁਅੱਤਲ ਦੀ ਇੱਕ ਪਰਤ ਵਰਕਪੀਸ ਦੀ ਸਤਹ 'ਤੇ ਲੱਗੇਗੀ, ਅਤੇ ਵਾਧੂ ਤਰਲ ਕੁਦਰਤੀ ਤੌਰ 'ਤੇ ਹੇਠਾਂ ਵਹਿ ਸਕਦਾ ਹੈ। ਇਹ ਵਿਧੀ ਛੋਟੇ ਆਕਾਰ ਦੇ ਵਰਕਪੀਸ ਲਈ ਢੁਕਵੀਂ ਹੈ ਜਿਨ੍ਹਾਂ ਨੂੰ ਬਾਹਰੀ ਸਤਹ 'ਤੇ ਪੂਰੀ ਪਰਤ ਦੀ ਲੋੜ ਹੁੰਦੀ ਹੈ।
3. ਬੁਰਸ਼ ਕਰਨਾ: ਬੁਰਸ਼ ਕਰਨ ਵਿੱਚ ਵਰਕਪੀਸ ਦੀ ਸਤ੍ਹਾ 'ਤੇ ਸਸਪੈਂਸ਼ਨ ਨੂੰ ਲਾਗੂ ਕਰਨ ਲਈ ਇੱਕ ਪੇਂਟਬਰਸ਼ ਜਾਂ ਬੁਰਸ਼ ਦੀ ਵਰਤੋਂ ਕਰਨਾ, ਇੱਕ ਕੋਟਿੰਗ ਬਣਾਉਣਾ ਸ਼ਾਮਲ ਹੈ। ਬੁਰਸ਼ ਕਰਨਾ ਆਮ ਸਥਾਨਿਕ ਕੋਟਿੰਗ ਜਾਂ ਤੰਗ ਸਤਹਾਂ 'ਤੇ ਸਿੰਗਲ-ਸਾਈਡ ਕੋਟਿੰਗ ਲਈ ਢੁਕਵਾਂ ਹੈ। ਹਾਲਾਂਕਿ, ਪਰਤ ਦੇ ਸੁੱਕਣ ਤੋਂ ਬਾਅਦ ਘੱਟ ਨਿਰਵਿਘਨ ਅਤੇ ਇੱਥੋਂ ਤੱਕ ਕਿ ਸਤ੍ਹਾ ਦੇ ਨਤੀਜੇ ਵਜੋਂ, ਅਤੇ ਹਰੇਕ ਕੋਟਿੰਗ ਪਰਤ ਦੀ ਮੋਟਾਈ 'ਤੇ ਸੀਮਾ ਦੇ ਕਾਰਨ ਇਹ ਘੱਟ ਹੀ ਵਰਤੀ ਜਾਂਦੀ ਹੈ।
4. ਡੋਲ੍ਹਣਾ: ਮੁਅੱਤਲ ਨੂੰ ਇੱਕ ਘੁੰਮਦੇ ਹੋਏ ਖੋਖਲੇ ਵਰਕਪੀਸ ਵਿੱਚ ਡੋਲ੍ਹ ਦਿਓ, ਇਹ ਯਕੀਨੀ ਬਣਾਉਂਦੇ ਹੋਏ ਕਿ ਅੰਦਰਲੀ ਸਤਹ ਮੁਅੱਤਲ ਦੁਆਰਾ ਪੂਰੀ ਤਰ੍ਹਾਂ ਢੱਕੀ ਹੋਈ ਹੈ। ਫਿਰ, ਇੱਕ ਕੋਟਿੰਗ ਬਣਾਉਣ ਲਈ ਵਾਧੂ ਤਰਲ ਨੂੰ ਡੋਲ੍ਹ ਦਿਓ। ਇਹ ਵਿਧੀ ਛੋਟੇ ਰਿਐਕਟਰਾਂ, ਪਾਈਪਲਾਈਨਾਂ, ਕੂਹਣੀਆਂ, ਵਾਲਵ, ਪੰਪ ਕੇਸਿੰਗਾਂ, ਟੀਜ਼ ਅਤੇ ਹੋਰ ਸਮਾਨ ਵਰਕਪੀਸ ਨੂੰ ਕੋਟਿੰਗ ਕਰਨ ਲਈ ਢੁਕਵੀਂ ਹੈ।
ਮੈਂ ਧਾਤ ਦੀਆਂ ਤਾਰਾਂ ਲਈ ਥਰਮੋਪਲਾਸਟਿਕ ਕੋਟਿੰਗਾਂ ਦੀ ਤਲਾਸ਼ ਕਰ ਰਿਹਾ/ਰਹੀ ਹਾਂ
ਇਹ ਇੰਟਰਨੈਟ ਸਾਈਟ ਮੇਰੀ ਸਾਹ ਲੈਣ ਵਾਲੀ, ਅਸਲ ਵਿੱਚ ਵਧੀਆ ਲੇਆਉਟ ਅਤੇ ਸੰਪੂਰਨ ਸਮੱਗਰੀ ਹੈ।
ਮੈਨੂੰ ਲਗਦਾ ਹੈ ਕਿ ਇਹ ਮੇਰੇ ਲਈ ਬਹੁਤ ਮਹੱਤਵਪੂਰਨ ਜਾਣਕਾਰੀ ਵਿੱਚੋਂ ਇੱਕ ਹੈ. ਅਤੇ ਮੈਂ ਤੁਹਾਡਾ ਲੇਖ ਪੜ੍ਹ ਕੇ ਖੁਸ਼ ਹਾਂ। ਪਰ ਕੁਝ ਸਾਧਾਰਨ ਚੀਜ਼ਾਂ 'ਤੇ ਬਿਆਨ ਦੇਣਾ ਚਾਹੁੰਦੇ ਹੋ, ਸਾਈਟ ਦਾ ਸਵਾਦ ਸੰਪੂਰਣ ਹੈ, ਲੇਖ ਅਸਲ ਵਿੱਚ ਬਹੁਤ ਵਧੀਆ ਹਨ : D. ਚੰਗੀ ਨੌਕਰੀ, ਸ਼ੁਭਕਾਮਨਾਵਾਂ