Kunststoffbeschichtung für Metall
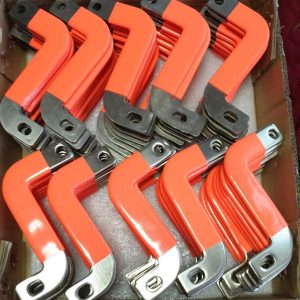
Bei der Kunststoffbeschichtung für Metall wird eine Kunststoffschicht auf die Oberfläche von Metallteilen aufgetragen, die es ihnen ermöglicht, die ursprünglichen Eigenschaften von Metall beizubehalten und gleichzeitig bestimmte Eigenschaften von Kunststoff wie Korrosionsbeständigkeit, Verschleißfestigkeit, elektrische Isolierung und Selbstfestigkeit zu gewährleisten -Schmierung. Dieser Prozess ist von großer Bedeutung für die Erweiterung des Anwendungsspektrums von Produkten und die Steigerung ihres wirtschaftlichen Werts.
Methoden zur Kunststoffbeschichtung von Metall
Es gibt viele Methoden zur Kunststoffbeschichtung, darunter Flammspritzen, Wirbelbett Sprühen, elektrostatisches Pulversprühen, Heißschmelzbeschichtung und Suspensionsbeschichtung. Es gibt auch viele Arten von Kunststoffen, die zum Beschichten verwendet werden können PVC, wobei PE und PA am häufigsten verwendet werden. Der für die Beschichtung verwendete Kunststoff muss in Pulverform mit einer Feinheit von 80–120 Mesh vorliegen.
Nach dem Beschichten kühlt man das Werkstück am besten schnell durch Eintauchen in kaltes Wasser ab. Durch schnelles Abkühlen kann die Kristallinität der Kunststoffbeschichtung verringert, der Wassergehalt erhöht, die Zähigkeit und der Oberflächenglanz der Beschichtung verbessert, die Haftung erhöht und die durch innere Spannung verursachte Ablösung der Beschichtung verhindert werden.
Um die Haftung zwischen der Beschichtung und dem Grundmetall zu verbessern, sollte die Oberfläche des Werkstücks vor dem Beschichten staubfrei und trocken, ohne Rost und Fett sein. In den meisten Fällen muss das Werkstück einer Oberflächenbehandlung unterzogen werden. Zu den Behandlungsmethoden gehören Sandstrahlen, chemische Behandlung und andere mechanische Methoden. Unter anderem hat Sandstrahlen die bessere Wirkung, da es die Oberfläche des Werkstücks aufraut, die Oberfläche vergrößert und Haken bildet, wodurch die Haftung verbessert wird. Nach dem Sandstrahlen sollte die Werkstückoberfläche mit sauberer Druckluft ausgeblasen werden, um Staub zu entfernen, und der Kunststoff sollte innerhalb von 6 Stunden beschichtet werden, da sonst die Oberfläche oxidiert und die Haftung der Beschichtung beeinträchtigt wird.
Vorteile
Die direkte Beschichtung mit Kunststoffpulver hat folgende Vorteile:
- Es kann mit Harzen verwendet werden, die nur in Pulverform erhältlich sind.
- Mit nur einem Auftrag lässt sich eine dicke Schicht erzielen.
- Produkte mit komplexen Formen oder scharfen Kanten können gut beschichtet werden.
- Die meisten pulverförmigen Kunststoffe weisen eine ausgezeichnete Lagerstabilität auf.
- Es sind keine Lösungsmittel erforderlich, was den Materialvorbereitungsprozess vereinfacht. Allerdings gibt es auch einige Nachteile oder Einschränkungen bei der Pulverbeschichtung. Wenn das Werkstück beispielsweise vorgewärmt werden muss, ist seine Größe begrenzt. Da der Beschichtungsprozess einige Zeit in Anspruch nimmt, sind bei großformatigen Werkstücken einige Bereiche bereits unter die erforderliche Temperatur abgekühlt, während das Spritzen noch nicht abgeschlossen ist. Bei der Kunststoff-Pulverbeschichtung kann der Pulververlust bis zu 60 % betragen und muss daher aus wirtschaftlichen Gründen gesammelt und wiederverwendet werden.
Flammspritzen
Beim Flammspritzen von Kunststoffbeschichtungen für Metall handelt es sich um einen Prozess, bei dem pulverförmiger oder pastöser Kunststoff mit einer Flamme aus einer Spritzpistole geschmolzen oder teilweise geschmolzen wird und der geschmolzene Kunststoff dann auf die Oberfläche eines Objekts gesprüht wird, um eine Kunststoffbeschichtung zu bilden. Die Dicke der Beschichtung liegt üblicherweise zwischen 0.1 und 0.7 mm. Bei Verwendung von pulverförmigem Kunststoff zum Flammspritzen sollte das Werkstück vorgewärmt werden. Das Vorheizen kann in einem Ofen erfolgen, wobei die Vorheiztemperatur variiert. depeDies hängt von der Art des zu versprühenden Kunststoffs ab.
Die Flammentemperatur beim Spritzen muss streng kontrolliert werden, da eine zu hohe Temperatur den Kunststoff verbrennen oder beschädigen kann, während eine zu niedrige Temperatur die Haftung beeinträchtigen kann. Im Allgemeinen ist die Temperatur beim Aufsprühen der ersten Kunststoffschicht am höchsten, was die Haftung zwischen Metall und Kunststoff verbessern kann. Beim Aufsprühen weiterer Schichten kann die Temperatur leicht gesenkt werden. Der Abstand zwischen Spritzpistole und Werkstück sollte zwischen 100 und 200 cm betragen. Bei flachen Werkstücken sollte das Werkstück waagerecht platziert und die Spritzpistole hin und her bewegt werden; Bei zylindrischen Werkstücken oder Werkstücken mit Innenbohrung sollten sie zum Rotationsspritzen auf einer Drehmaschine montiert werden. Die Lineargeschwindigkeit des rotierenden Werkstücks sollte zwischen 20 und 60 m/min liegen. Nachdem die erforderliche Schichtdicke erreicht ist, sollte das Sprühen gestoppt werden und das Werkstück weiter rotieren, bis der geschmolzene Kunststoff erstarrt, und dann schnell abgekühlt werden.
Obwohl das Flammspritzen eine relativ geringe Produktionseffizienz aufweist und reizende Gase verwendet, ist es dennoch ein wichtiges Verarbeitungsverfahren in der Industrie, da es im Vergleich zu anderen Verfahren nur geringe Ausrüstungsinvestitionen erfordert und bei der Innenbeschichtung von Tanks, Behältern und großen Werkstücken effektiv ist .
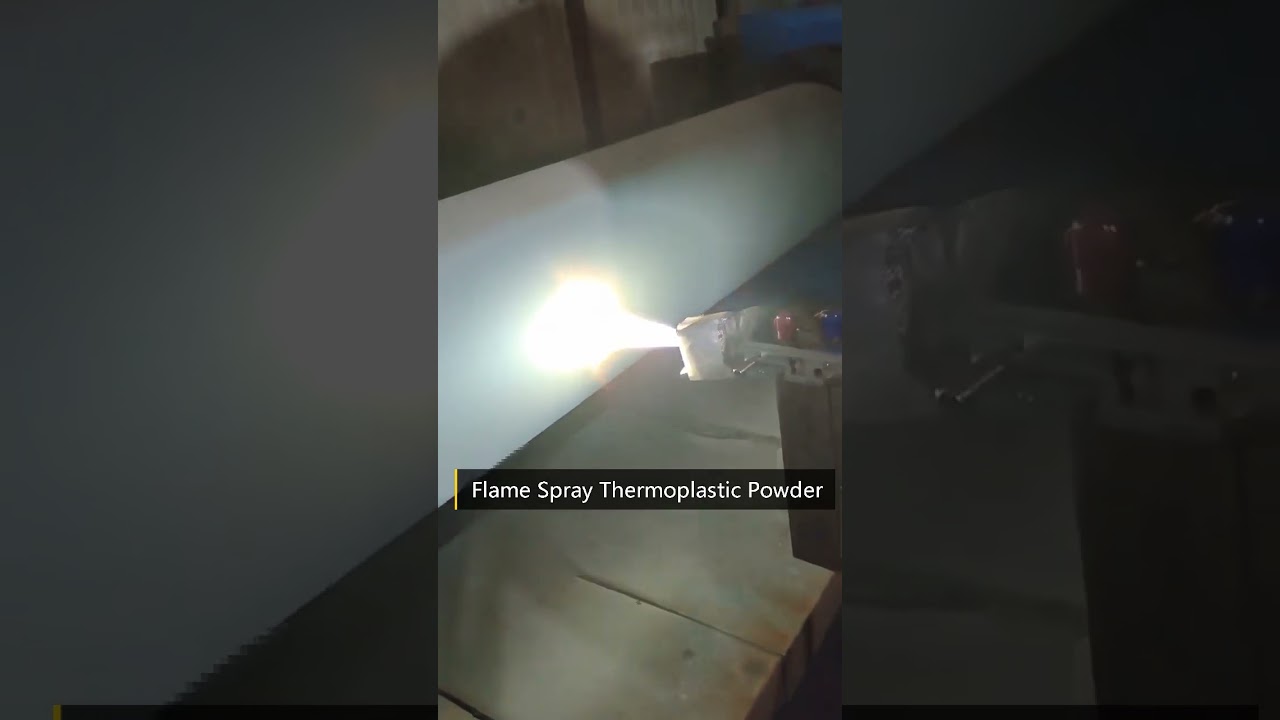
Wirbelschicht-Tauchkunststoffbeschichtung
Das Funktionsprinzip der Kunststoffbeschichtung im Wirbelschichtverfahren für Metalle ist wie folgt: Kunststoffbeschichtungspulver wird in einen zylindrischen Behälter mit einer porösen Trennwand an der Oberseite gegeben, die nur Luft, nicht das Pulver, durchlässt. Wenn Druckluft vom Boden des Behälters eindringt, bläst sie das Pulver auf und suspendiert es im Behälter. Taucht man ein vorgewärmtes Werkstück darin ein, schmilzt das Harzpulver, haftet am Werkstück und bildet einen Überzug.
Die Dicke der im Wirbelbett erhaltenen Beschichtung depeInformationen zu Temperatur, spezifischer Wärmekapazität, Oberflächenkoeffizient, Sprühzeit und Art des verwendeten Kunststoffs beim Eintritt des Werkstücks in die Wirbelkammer. Allerdings können dabei nur die Temperatur und die Sprühzeit des Werkstücks kontrolliert werden, die durch Versuche in der Produktion ermittelt werden müssen.
Beim Eintauchen ist es erforderlich, dass das Kunststoffpulver glatt und gleichmäßig fließt, ohne Agglomeration, Wirbelströmung oder übermäßige Dispersion von Kunststoffpartikeln. Um diesen Anforderungen gerecht zu werden, sind entsprechende Maßnahmen zu ergreifen. Der Zusatz einer Rührvorrichtung kann die Agglomeration und Wirbelströmung reduzieren, während die Zugabe einer kleinen Menge Talkumpuder zum Kunststoffpulver die Fluidisierung fördert, jedoch die Qualität der Beschichtung beeinträchtigen kann. Um die Ausbreitung von Kunststoffpartikeln zu verhindern, sollten die Luftstromrate und die Gleichmäßigkeit der Kunststoffpulverpartikel streng kontrolliert werden. Eine gewisse Dispersion ist jedoch unvermeidlich, daher sollte im oberen Teil des Wirbelbetts eine Rückgewinnungsvorrichtung installiert werden.
Die Vorteile der Wirbelschicht-Tauchbeschichtung von Kunststoffen sind die Möglichkeit, komplex geformte Werkstücke zu beschichten, eine hohe Beschichtungsqualität, die Erzielung einer dickeren Beschichtung in einer Anwendung, ein minimaler Harzverlust und eine saubere Arbeitsumgebung. Der Nachteil ist die Schwierigkeit, große Werkstücke zu bearbeiten.
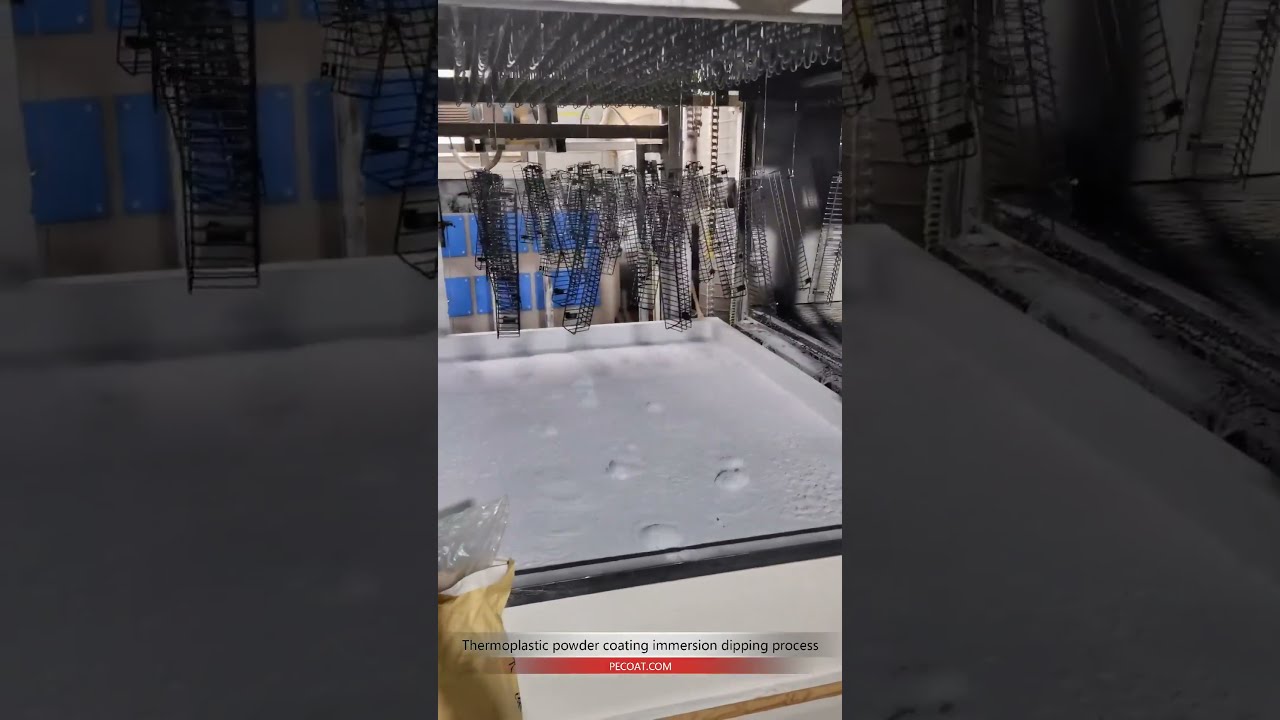
Elektrostatisches Spritzen von Kunststoffbeschichtungen für Metall
Beim elektrostatischen Spritzen wird Harz-Kunststoff-Beschichtungspulver durch elektrostatische Kraft und nicht durch Schmelzen oder Sintern auf der Oberfläche des Werkstücks fixiert. Das Prinzip besteht darin, das von einem elektrostatischen Hochspannungsgenerator erzeugte elektrostatische Feld zu nutzen, um das aus der Spritzpistole gesprühte Harzpulver mit statischer Elektrizität aufzuladen, und das geerdete Werkstück wird zur positiven Hochspannungselektrode. Dadurch lagert sich schnell eine Schicht gleichmäßigen Kunststoffpulvers auf der Oberfläche des Werkstücks ab. Bevor die Ladung abgebaut wird, haftet die Pulverschicht fest. Nach dem Erhitzen und Abkühlen kann eine gleichmäßige Kunststoffbeschichtung erhalten werden.
Das elektrostatische Pulversprühen wurde Mitte der 1960er Jahre entwickelt und lässt sich leicht automatisieren. Wenn die Beschichtung nicht dick sein muss, erfordert das elektrostatische Spritzen kein Vorwärmen des Werkstücks und kann daher für wärmeempfindliche Materialien oder Werkstücke verwendet werden, die nicht zum Erhitzen geeignet sind. Es ist auch kein großer Vorratsbehälter erforderlich, was beim Wirbelschichtsprühen unerlässlich ist. Das am Werkstück vorbeiströmende Pulver wird von der Rückseite des Werkstücks angezogen, sodass die Overspray-Menge deutlich geringer ist als bei anderen Sprühverfahren und das gesamte Werkstück durch einseitiges Sprühen beschichtet werden kann. Allerdings müssen große Werkstücke weiterhin von beiden Seiten besprüht werden.
Werkstücke mit unterschiedlichen Querschnitten können bei der anschließenden Erwärmung Schwierigkeiten bereiten. Wenn der Querschnittsunterschied zu groß ist, erreicht der dickere Teil der Beschichtung möglicherweise nicht die Schmelztemperatur, während der dünnere Teil möglicherweise bereits geschmolzen oder zersetzt ist. In diesem Fall ist die thermische Stabilität des Harzes wichtig.
Komponenten mit sauberen Innenecken und tiefen Löchern können nicht so leicht durch elektrostatisches Sprühen abgedeckt werden, da diese Bereiche über eine elektrostatische Abschirmung und R verfügenepel Das Pulver verhindert, dass die Beschichtung in die Ecken oder Löcher eindringt, es sei denn, die Spritzpistole kann in diese eingeführt werden. Darüber hinaus erfordert das elektrostatische Sprühen feinere Partikel, da größere Partikel eher dazu neigen, sich vom Werkstück zu lösen, und Partikel, die feiner als 150 Mesh sind, bei der elektrostatischen Wirkung wirksamer sind.
Verfahren zur Heißschmelzbeschichtung
Das Funktionsprinzip des Hotmelt-Beschichtungsverfahrens besteht darin, Kunststoffbeschichtungspulver mit einer Spritzpistole auf ein vorgewärmtes Werkstück zu sprühen. Der Kunststoff schmilzt unter Ausnutzung der Wärme des Werkstücks und nach dem Abkühlen kann eine Kunststoffbeschichtung auf das Werkstück aufgebracht werden. Bei Bedarf ist auch eine Nachwärmbehandlung erforderlich.
Der Schlüssel zur Steuerung des Hotmelt-Beschichtungsprozesses ist die Vorwärmtemperatur des Werkstücks. Wenn die Vorwärmtemperatur zu hoch ist, kann dies zu starker Oxidation der Metalloberfläche führen, die Haftung der Beschichtung verringern und sogar zur Zersetzung des Harzes und zur Schaumbildung oder Verfärbung der Beschichtung führen. Wenn die Vorwärmtemperatur zu niedrig ist, hat das Harz eine schlechte Fließfähigkeit, was es schwierig macht, eine gleichmäßige Beschichtung zu erhalten. Oftmals lässt sich mit einem einzigen Sprühauftrag des Hotmelt-Beschichtungsverfahrens nicht die gewünschte Dicke erreichen, sodass mehrere Sprühaufträge erforderlich sind. Nach jedem Sprühauftrag ist eine Wärmebehandlung erforderlich, um die Beschichtung vollständig zu schmelzen und aufzuhellen, bevor die zweite Schicht aufgetragen wird. Dadurch wird nicht nur eine gleichmäßige und glatte Beschichtung gewährleistet, sondern auch die mechanische Festigkeit deutlich verbessert. Die empfohlene Wärmebehandlungstemperatur für Polyethylen hoher Dichte liegt bei etwa 170 °C und für chlorierten Polyether bei etwa 200 °C, mit einer empfohlenen Zeit von 1 Stunde.
Das Hotmelt-Beschichtungsverfahren erzeugt hochwertige, ästhetisch ansprechende, stark haftende Beschichtungen mit minimalem Harzverlust. Es ist leicht zu kontrollieren, hat einen minimalen Geruch und die verwendete Spritzpistole tut dies auch.
Weitere verfügbare Methoden zur Kunststoffbeschichtung von Metall
1. Sprühen: Füllen Sie die Suspension in den Behälter der Sprühpistole und sprühen Sie die Beschichtung mit Druckluft mit einem Manometerdruck von nicht mehr als 0.1 MPa gleichmäßig auf die Oberfläche des Werkstücks. Um Federungsverluste zu minimieren, sollte der Luftdruck so niedrig wie möglich gehalten werden. Der Abstand zwischen Werkstück und Düse sollte 10–20 cm betragen und die Sprühfläche sollte senkrecht zur Richtung des Materialflusses gehalten werden.
2. Eintauchen: Das Werkstück einige Sekunden in die Suspension eintauchen und dann herausnehmen. Zu diesem Zeitpunkt haftet eine Suspensionsschicht an der Oberfläche des Werkstücks und die überschüssige Flüssigkeit kann auf natürliche Weise nach unten abfließen. Dieses Verfahren eignet sich für kleine Werkstücke, die eine vollständige Beschichtung der Außenfläche erfordern.
3. Streichen: Beim Streichen wird die Suspension mit einem Pinsel oder einer Bürste auf die Oberfläche des Werkstücks aufgetragen und so eine Schicht erzeugt. Das Bürsten eignet sich für allgemeine punktuelle Beschichtungen oder einseitige Beschichtungen auf schmalen Flächen. Aufgrund der daraus resultierenden weniger glatten und gleichmäßigen Oberfläche nach dem Trocknen der Beschichtung und der begrenzten Dicke jeder Beschichtungsschicht wird es jedoch selten verwendet.
4. Gießen: Gießen Sie die Suspension in ein rotierendes hohles Werkstück und achten Sie darauf, dass die Innenfläche vollständig von der Suspension bedeckt ist. Gießen Sie dann die überschüssige Flüssigkeit aus, um eine Schicht zu bilden. Dieses Verfahren eignet sich zum Beschichten kleiner Reaktoren, Rohrleitungen, Bögen, Ventile, Pumpengehäuse, T-Stücke und anderer ähnlicher Werkstücke.
Ich suche thermoplastische Beschichtungen für Metalldrähte
Diese Internetseite ist mein Atem, wirklich gutes Layout und perfekter Inhalt.
Ich denke, das ist eine der wichtigsten Informationen für mich. Und ich freue mich, Ihren Artikel zu lesen. Aber ich möchte mich zu ein paar normalen Dingen äußern: Der Geschmack der Seite ist perfekt, die Artikel sind wirklich großartig: D. Gute Arbeit, Prost