파우더 딥 코팅은 여러 가지 장점을 제공합니다.
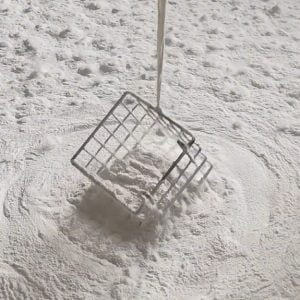
파우더 딥 코팅 공정
가루 딥 코팅 분체 도료에 기판을 담그어 코팅하는 코팅 방법입니다. 이 프로세스에는 여러 단계가 포함됩니다.eps 균일한 도포와 코팅의 적절한 접착을 보장합니다.
분말 딥 코팅의 첫 번째 단계는 기판을 준비하는 것입니다. 분체 코팅의 접착력을 강화하려면 기질을 세척하고, 탈지하고, 거칠게 처리해야 할 수도 있습니다. 표면의 오염 물질이나 잔해물은 코팅의 접착력과 품질에 영향을 미칠 수 있습니다.
기판이 준비되면 특정 온도로 가열됩니다. 기판을 가열하면 분말의 접착력이 향상되고 코팅 균일성이 향상됩니다. 필요한 정확한 온도 depe분체 코팅 유형과 코팅되는 기판에 대해 알아봅니다.
다음으로, 분체 도료가 채워진 용기에 기재를 담급니다. 기재를 분말 코팅 용기에서 꺼내면 분말이 표면에 달라붙습니다. 담그는 과정은 다음과 같습니다.epe원하는 코팅 두께를 만들기 위해 한 번 이상 코팅했습니다.
침지 후 과잉 분말이 기판에서 제거됩니다. 이는 공기 송풍기, 진동 또는 기타 기술을 사용하여 하지에 부착되지 않은 느슨한 분말을 제거할 수 있습니다. 여분의 파우더를 제거하면 매끄럽고 균일한 코팅을 얻는 데 도움이 됩니다.
코팅된 기판은 경화 단계에 들어갑니다. 경화는 일반적으로 오븐에서 기판을 가열하거나 다른 가열 방법을 사용하여 수행됩니다. 열로 인해 분말 코팅이 녹고 흘러서 단단하고 내구성 있는 코팅이 만들어집니다. 경화 시간 및 온도 depe특정 분말 코팅 제제 및 코팅 두께에 따라 달라집니다.
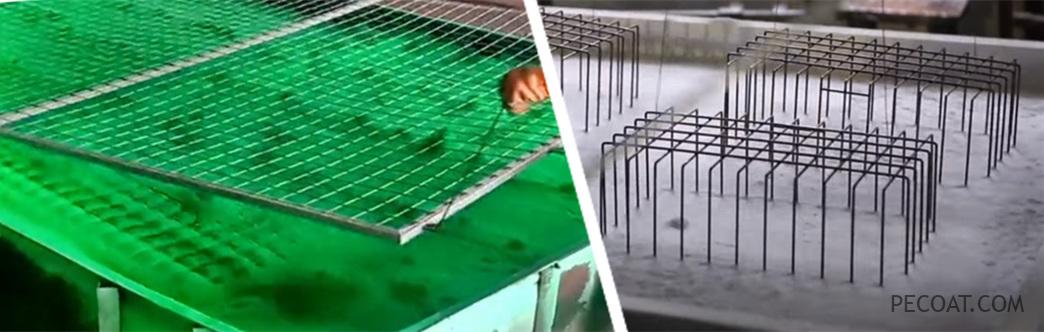
장점
파우더 딥 코팅은 다른 코팅 방법에 비해 몇 가지 장점을 제공합니다. 주요 장점 중 하나는 기판 전체에 걸쳐 균일한 코팅 두께를 달성할 수 있다는 것입니다. 이는 전기 절연이나 부식 방지와 같이 일관된 코팅 특성이 중요한 응용 분야에서 특히 중요합니다. 또한 분체 코팅은 우수한 내구성, 긁힘 방지, 퇴색 방지 및 화학 물질 노출을 제공합니다.
파우더 딥 코팅의 또 다른 장점은 효율성입니다. 코팅 공정을 자동화할 수 있어 대량 생산이 가능합니다. 분체 코팅 재료는 재활용 및 재사용이 가능하여 폐기물과 비용을 줄일 수 있습니다. 또한 분체 코팅은 휘발성 유기 화합물(VOC) 방출이 낮아 일부 용제 기반 코팅에 비해 환경 친화적입니다.
파우더 딥 코팅은 다양한 산업 분야에 적용됩니다. 나사, 너트, 브래킷과 같은 소형 부품을 코팅하기 위해 자동차, 전자 및 가전 제품 산업에서 일반적으로 사용됩니다. 코팅은 부식 방지 기능을 제공하고 전기 절연성을 향상시키며 구성 요소의 외관을 향상시킵니다. 분말 딥 코팅은 깨끗하고 멸균된 코팅이 필요한 의료 기기 제조에도 사용됩니다.
정리하면, 파우더 딥 코팅은 균일한 코팅 두께와 내구성, 효율성을 제공하는 코팅 방식입니다. 분체 도료에 기질을 담근 후 경화시킴으로써 단단하고 보호적인 코팅이 이루어집니다. 이 공정은 작은 부품이나 부품 코팅이 필요한 산업에서 널리 사용되며 향상된 성능과 미적 매력을 제공합니다. 특정 요구 사항과 응용 분야는 다양할 수 있지만 분말 딥 코팅은 계속해서 많은 코팅 응용 분야에서 인기 있는 선택입니다.
