Why Us
Thermoplastic coating dip powder is a kind of thermoplastic powder coatings that is applied using a fluidized bed dipping system. The preheated parts are immersed in a hopper with a fluidized thermoplastic powder coating. The powder is attracted to and subsequently fuses to the heated surface .
Thermoplastic dip powder coating is usually in powder form. It does not react chemically during heating. The metal’s surface is first heated to the desired temperature. The subsequent dipping,post-heat and cooling process then causes the coating to levelling, harden and gain strength and excellent performance.
PECOAT® thermoplastic polyethylene powder coating and PVC powder coating prevails over other coatings for excellent performance and high cost efficiency. The main advantage lies within its high adhesion strength which makes the coating extremely resistant to impact, mar, scratch even get peeled.
- Thermoplastic powder coatings can be laid down in much thicker coatings than other powder coating options. They feel softer and more comfortable to touch than hard shell coatings.
- The thick plastic coating is an excellent electrical insulator. It also makes the coated objects relatively inert in terms of temperature transmission.
- The thermoplastic material melts and flows to create a very smooth, continuous surface that covers corners well, it is long-lasting and has excellent UV resistance for color retention.
- Compared to thermoset powder coatings, thermoplastic coatings contain no VOCs, halogens or BPA and are environmentally responsible.
The unique properties of thermoplastic coatings make them extremely useful in a range of applications. PECOAT® thermoplastic coating dip powder – polyethylene and PVC powder coating are widely use in:
- Household appliances
- Auto parts
- Coating of aluminum profiles
- Window trim
- Indoor and outdoor furniture
- Building construction
- Metal fences and railings
- Food service area
- Merchandise display, etc.
Different industries have varying requirements for products, and these requirements extend to the performance of the applied coating, encompassing factors such as coating thickness, hardness, scratch resistance, adhesion, and appearance.
There are a number of materials used as thermoplastic dip powder coating and electrostatic spray powder coating, including polyethylene, PVC, nylon, polypropylene. The selection should be based on the specific requirement for the product to be coated.
Polyethylene powder coating is the most widely used, the coating has excellent chemical resistance, anti-aging, impact resistance, bending resistance, acid resistance, salt spray corrosion resistance, and has a better surface decoration performance. Due to it good electrical insulation properties, they are often used in applications where users interact with the objects frequently, such as handles in subway cars.
Polyvinyl coatings (PVC) usually need a primer to gain a strong bond with the object to be coated but retain the flexibility that makes them ideal for use in applications where the objects are subject to fabrication operations post coating, such as bending and drawing.
Nylon coating also needs a primer for best adhesion, nylon coatings are hard wearing with an extremely low coefficient of friction, and are often used for bearings and other applications with moving parts.
Items | PE | PVC | Nylon(PA) |
Weather ability | 2 | 4 | 3 |
Salt spray resistance | 2 | 5 | 3 |
Acid resistance | 4 | 5 | 1 |
Impact resistance | 4 | 5 | 5 |
FDA | Pass | No Pass | Pass |
Electrical insulating | 5 | 4 | 3 |
Adhesion | 4 | 1 | 1 |
Flexibility | 4 | 4 | 4 |
Hardness | 4 | 3 | 4 |
*The above comparison is for reference only. *5 – Excellent , 4 – Better, 3 – Good, 2 – Ok , 1 – Poor |
Thermoplastic coating dip powder is a kind of thermoplastic powder coatings that is applied using a fluidized bed dipping system. The preheated parts are immersed in a hopper with a fluidized thermoplastic powder coating. The powder is attracted to and subsequently fuses to the heated surface .
Thermoplastic coating is usually in powder form. It does not react chemically during heating. The metal’s surface is first heated to the desired temperature. The subsequent dipping,post-heat and cooling process then causes the coating to levelling, harden and gain strength and excellent performance.
PECOAT® thermoplastic polyethylene powder coating and PVC powder coating prevails over other coatings for excellent performance and high cost efficiency. The main advantage lies within its high adhesion strength which makes the coating extremely resistant to impact, mar, scratch even get peeled.
- Thermoplastic powder coatings can be laid down in much thicker coatings than other powder coating options. They feel softer and more comfortable to touch than hard shell coatings.
- The thick plastic coating is an excellent electrical insulator. It also makes the coated objects relatively inert in terms of temperature transmission.
- The thermoplastic material melts and flows to create a very smooth, continuous surface that covers corners well, it is long-lasting and has excellent UV resistance for color retention.
- Compared to thermoset powder coatings, thermoplastic coatings contain no VOCs, halogens or BPA and are environmentally responsible.
The unique properties of thermoplastic coatings make them extremely useful in a range of applications. PECOAT® thermoplastic coating dip powder – polyethylene and PVC powder coating are widely use in:
- Household appliances
- Auto parts
- Coating of aluminum profiles
- Window trim
- Indoor and outdoor furniture
- Building construction
- Metal fences and railings
- Food service area
- Merchandise display, etc.
Different industries have varying requirements for products, and these requirements extend to the performance of the applied coating, encompassing factors such as coating thickness, hardness, scratch resistance, adhesion, and appearance.
There are a number of materials used as thermoplastic powder coating, including polyethylene, PVC, nylon, polypropylene. The selection should be based on the specific requirement for the product to be coated.
Polyethylene powder coating is the most widely used, the coating has excellent chemical resistance, anti-aging, impact resistance, bending resistance, acid resistance, salt spray corrosion resistance, and has a better surface decoration performance. Due to it good electrical insulation properties, they are often used in applications where users interact with the objects frequently, such as handles in subway cars.
Polyvinyl coatings (PVC) usually need a primer to gain a strong bond with the object to be coated but retain the flexibility that makes them ideal for use in applications where the objects are subject to fabrication operations post coating, such as bending and drawing.
Nylon coating also needs a primer for best adhesion, nylon coatings are hard wearing with an extremely low coefficient of friction, and are often used for bearings and other applications with moving parts.
Items | PE | PVC | PA |
Weather ability | 2 | 4 | 3 |
Salt spray resistance | 2 | 5 | 3 |
Acid resistance | 4 | 5 | 1 |
Impact resistance | 4 | 5 | 5 |
FDA | Pass | No | Pass |
Electrical insulating | 5 | 4 | 3 |
Adhesion | 4 | 1 | 1 |
Flexibility | 4 | 4 | 4 |
Hardness | 3 | 4 | 4 |
*The above comparison is for reference only. *5 – Excellent , 4 – Better, 3 – Good, 2 – Ok , 1 – Poor |
Industry News
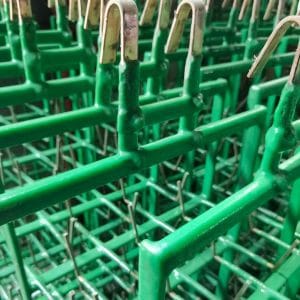
Enhance Electroplating Jigs with Thermoplastic PE Powder PECOAT®EJ3065
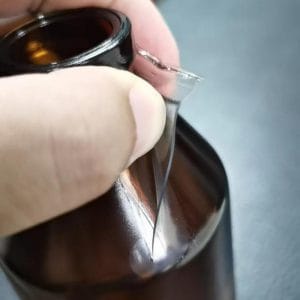
Use PVC Plastisol Coat to Protect Medicine Glass Bottle
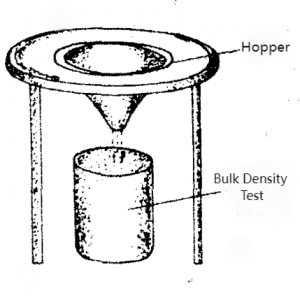
Relationship Between Bulk Density and Specific Density
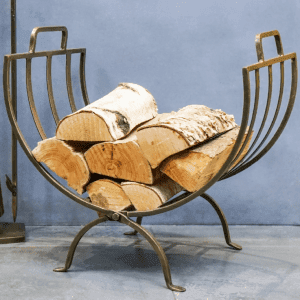