Plastisol Dip Coating :The Durable Solution for Coating Needs
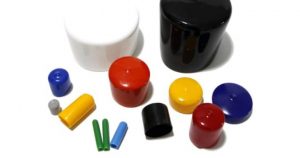
Plastisol dip coating is a versatile and cost-effective process used to apply a protective or decorative coating to a wide range of substrates. It involves immersing the preheated substrate in a plastisol resin, which is a liquid suspension of polyvinyl chloride (PVC) particles. The plastisol adheres to the substrate and forms a continuous film upon curing, typically through heat or ultraviolet (UV) radiation.
Plastisol Dip Coating: A Comprehensive Guide to the Process
Plastisol dip coating is a versatile and widely used technique for applying a protective or decorative coating to various substrates. This comprehensive guide delves into the process, exploring its advantages, applications, and step-by-step instructions.
Plastisol, a suspension of polyvinyl chloride (PVC) resin in a liquid plasticizer, forms the basis of this coating method. In room temperature, the plastisol is a viscous liquid that can be easily applied to the preheated substrate by dipping. Upon cooling, it solidifies into a durable and flexible coating.
The advantages of plastisol dip coating are numerous. It provides excellent corrosion resistance, electrical insulation, and resistance to chemicals and abrasion. Additionally, it offers a wide range of colors and textures, making it suitable for both functional and aesthetic applications.
Plastisol dip coating finds applications in diverse industries, including automotive, construction, electronics, and medical. It is commonly used to coat metal parts, tools, handles, and electrical components. The coating protects these substrates from harsh environments, enhances their durability, and improves their appearance.
The process of plastisol coating involves several steps. First, the substrate is cleaned and prepared to ensure proper adhesion. The substrate is then heated to a specified temperature, and dipped to the liquid plastisol. The thickness of the coating can be controlled by the immersion time and the viscosity of the plastisol.
After dipping, the substrate is removed from the plastisol and transferred to the curing oven. During curing, the plastisol solidifies and forms a continuous coating. The coated substrate can then undergo further processing, such as painting, to enhance its properties.
To achieve optimal results, it is crucial to consider several factors during plastisol dip coating. The viscosity of the plastisol, the temperature of the substrate, and the immersion time all play a role in determining the coating’s thickness, adhesion, and appearance.
In conclusion, plastisol dip coating is a versatile and effective technique for applying protective and decorative coatings to various substrates. Its advantages, wide range of applications, and relatively simple process make it a popular choice in industries seeking durable and aesthetically pleasing coatings. By understanding the process and considering the key factors involved, manufacturers can optimize their plastisol dip coating operations to achieve desired results.
( PECOAT® PVC plastisol coatings)
Benefits of Plastisol Dip Coating for Industrial Applications
Plastisol dip coating, a versatile and cost-effective process, offers numerous advantages for industrial applications. This technique involves immersing a substrate into a plastisol resin, creating a protective and decorative coating.
One of the primary benefits of plastisol dip coating is its durability. The resulting coating exhibits excellent resistance to abrasion, corrosion, and chemicals, making it ideal for harsh industrial environments. Additionally, plastisol coatings provide electrical insulation, protecting components from electrical hazards.
Plastisol dip coating also offers flexibility and impact resistance. The coating can withstand bending and deformation without cracking or peeling, ensuring the integrity of the substrate. This flexibility is particularly advantageous for applications involving vibration or movement.
Furthermore, plastisol dip coating provides excellent adhesion to various substrates, including metals, plastics, and ceramics. The strong bond between the coating and the substrate ensures long-lasting protection and prevents peeling or delamination.
Another advantage of plastisol coating is its ability to create a seamless, uniform coating. The process eliminates sharp edges or corners, reducing the risk of snags or tears. This smooth surface also enhances the aesthetic appeal of the coated product.
Plastisol dip coating is also highly customizable. The resin can be formulated with various pigments and additives to achieve specific colors, textures, and properties. This versatility allows for tailored coatings that meet the unique requirements of different applications.
In addition to its protective and decorative benefits, plastisol dip coating can also improve the functionality of industrial components. For instance, it can provide a non-slip surface for handles or grips, enhancing safety and ergonomics.
Overall, plastisol dip coating offers a wide range of benefits for industrial applications. Its durability, flexibility, adhesion, seamless finish, and customization options make it an ideal choice for protecting and enhancing the performance of various components.
Troubleshooting Common Issues in Plastisol Dip Coating
Plastisol dip coating is a versatile process that provides a durable and protective coating for various substrates. However, certain issues can arise during the process, affecting the coating’s quality and performance. Here are some common problems and their potential solutions:
1. Wrinkling and Cracking:
Cause:Excessive coating thickness or improper curing temperature.
Solution:Adjust the dipping time or thickness to achieve an optimal coating thickness. Ensure the curing temperature is within the recommended range.
2. Poor Adhesion:
Cause: Inadequate surface preparation or improper curing.
Solution: Thoroughly clean and prepare the substrate before dipping. Ensure the curing time and temperature are sufficient to achieve proper adhesion.
3. Pinholing:
Cause:Air entrapment or contamination in the plastisol.
Solution: Filter the plastisol to remove contaminants. Remove air bubbles before dipping.
4. Sagging and Flow Marks:
Cause:Excessive coating thickness or improper curing temperature.
Solution:Adjust the dipping time or thickness to achieve an optimal coating thickness. Ensure the curing temperature is within the recommended range.
5. Contamination:
Cause:Foreign particles or debris in the plastisol or on the substrate.
Solution:Filter the plastisol and clean the substrate thoroughly before dipping. Use a clean dipping tank and equipment.
By understanding these common issues and implementing the appropriate solutions, manufacturers can optimize their plastisol dip coating process, ensuring the production of high-quality and durable coatings.
Leave a Reply