Category: Plastisol Dipping Technology
Plastisol dipping technology is a process used in the manufacturing of various products, including clothing, toys, and industrial components. It involves dipping a substrate, such as fabric or metal, into a liquid polymer called plastisol, which is then cured to form a solid coating.
Plastisol is a suspension of PVC particles in a liquid plasticizer. It is a versatile material that can be formulated to have different properties, such as flexibility, durability, and resistance to chemicals and UV light. Plastisol is also easy to work with, as it can be molded, printed, and coated onto various substrates.
The plastisol dipping process starts with the preparation of the substrate, which is cleaned and pre-treated to ensure good adhesion and surface finish. The substrate is then dipped into a tank of plastisol, which is heated to a temperature of around 180-200°C. The heat causes the plastisol to fuse and crosslink, forming a solid coating on the substrate. The thickness of the coating can be controlled by adjusting the dipping time and the viscosity of the plastisol.
After the dipping process, the coated substrate is cured in an oven or a conveyorized dryer, which heats the plastisol to a higher temperature for a specific time. This step ensures that the plastisol is fully cured and has the desired properties, such as hardness, flexibility, and color stability.
Plastisol dipping technology has many advantages over other coating and printing methods. It can produce a uniform and consistent coating on complex shapes and surfaces, such as 3D objects and irregularly shaped parts. It can also create a variety of textures and finishes, such as glossy, matte, and textured. Plastisol coatings are also resistant to abrasion, impact, and weathering, making them suitable for outdoor and industrial applications.
In the textile industry, plastisol dipping is commonly used for printing designs and logos on t-shirts, sweatshirts, and other garments. The plastisol ink is applied to the fabric by screen printing or transfer printing, and then cured to form a durable and vibrant print. Plastisol printing is preferred over other methods, such as water-based and discharge printing, because it can produce opaque and bright colors on dark fabrics, and does not require pre-treatment or post-curing.
In the toy industry, plastisol dipping is used to create soft and flexible toys, such as rubber ducks, balls, and figurines. The plastisol is molded into the desired shape and then cured to form a solid and durable toy. Plastisol toys are safe for children to play with, as they do not contain harmful chemicals, such as phthalates and lead, which are found in some other types of plastics.
In the automotive and industrial industries, plastisol dipping is used to coat metal parts, such as handles, knobs, and levers, to improve their grip, durability, and appearance. Plastisol coatings can also provide insulation and corrosion resistance, making them suitable for electrical and marine applications.
Overall, plastisol dipping technology is a versatile and cost-effective process that can be used to create a wide range of products with different properties and applications. It is a popular choice for manufacturers who require high-quality and durable coatings on various substrates.
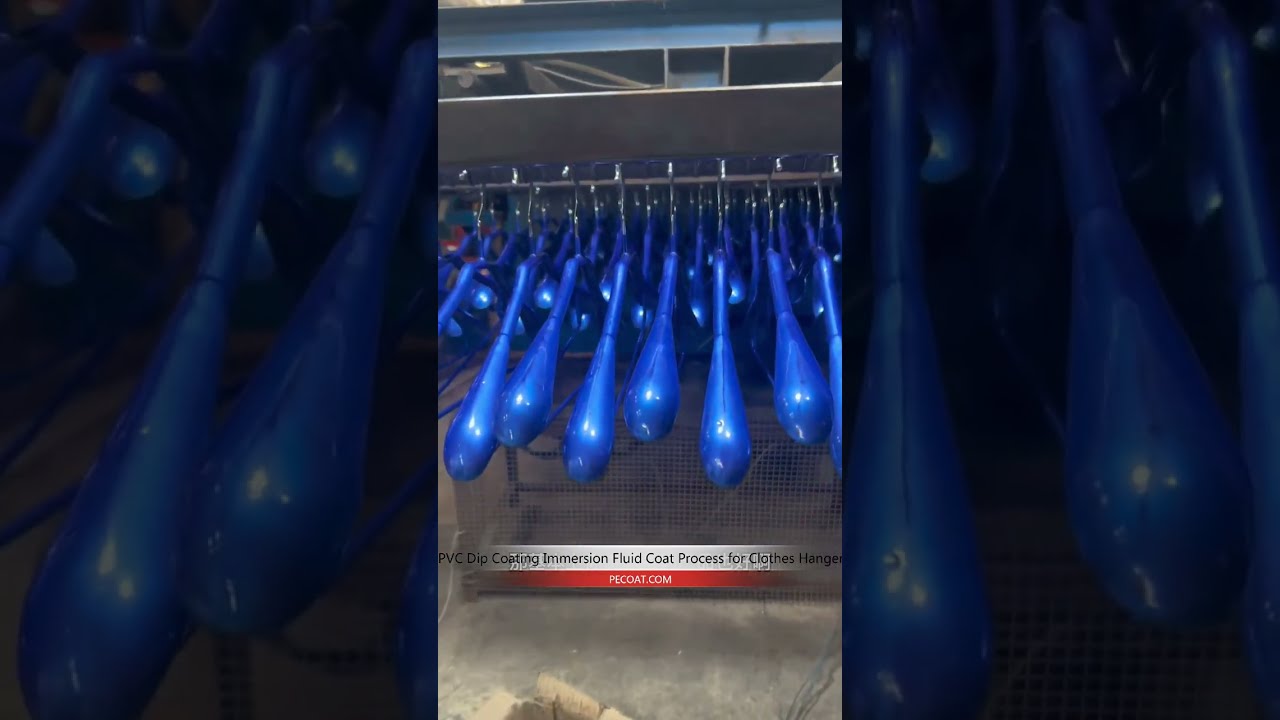
Use PVC Plastisol Coat to Protect Medicine Glass Bottle
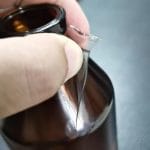
Using PVC plastisol coating to protect medicine glass bottles is a feasible technical approach, which can endow glass bottles with functions such as impact resistance, anti-slip, and chemical corrosion resistance. The following is a detailed introduction to this application, including advantages, processes, considerations, and alternative solutions: Advantages of PVC Plastisol Coating for Pharmaceutical Glass Bottles Enhanced Impact Resistance PVC plastisol forms a flexible protective layer on the glass surface, which can absorb external impacts and reduce the risk of bottleRead More …
Why Use a Release Agent?
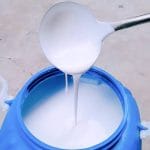
A release agent is a substance applied to molds (molds, dies, or surfaces ) to prevent materials being molded (e.g., plastics, rubber, metal, composites, or concrete) from sticking to the surface, ensuring easy removal of the finished product. Here are the key reasons for using release agents: 1.Prevent Adhesion Between Product and Mold During manufacturing processes (e.g., injection molding, casting, thermoset curing, or composite layup), the material in its molten, liquid, or semi-solid state can bond to the mold surfaceRead More …
Reference values of viscosity for common liquids
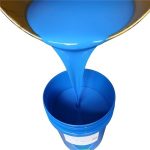
Viscosity definition: Viscosity is the internal friction of a liquid. When a fluid is subjected to an external force and undergoes relative movement, the resistance generated between fluid molecules makes the fluid unable to flow smoothly. The magnitude of this resistance is called viscosity. Fluid viscosity is related to temperature. Dynamic viscosity: Dynamic viscosity is the force required to generate a unit flow velocity per unit area of liquid layer over a unit distance. In the International System of Units,Read More …
Adhesion Primer improve the adhesion bonding of PVC coatings
Table of Contents Enhancing Adhesion Strength: The Role of Adhesion Primer in PVC Coatings Optimizing Bonding Performance: A Guide to Adhesion Primer for PVC Coatings Troubleshooting Adhesion Issues: The Importance of Adhesion Primer in PVC Coatings Enhancing Adhesion Strength: The Role of Adhesion Primer in PVC Dip Coatings Adhesion primer plays a crucial role in enhancing the adhesion bonding ability of PVC coatings. It acts as an intermediary layer between the substrate and the coating, promoting strong and durable adhesion.Read More …
Choosing the Best PVC Dip Coating Supplier: Key Considerations
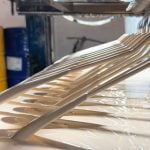
PVC Dip Coating: A Comprehensive Guide for Suppliers PVC dip coating is a versatile and cost-effective process that enhances the properties of various substrates. As a supplier, it is crucial to understand the intricacies of this technique to provide optimal solutions to your customers. 1.Process Overview PVC dip coating involves immersing a substrate into a liquid PVC resin solution. The substrate is then withdrawn, allowing a thin layer of PVC to adhere to its surface. This layer provides protection againstRead More …
Plastisol Dip Coating :The Durable Solution for Coating Needs
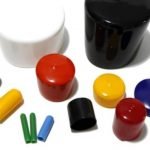
Plastisol dip coating is a versatile and cost-effective process used to apply a protective or decorative coating to a wide range of substrates. It involves immersing the preheated substrate in a plastisol resin, which is a liquid suspension of polyvinyl chloride (PVC) particles. The plastisol adheres to the substrate and forms a continuous film upon curing, typically through heat or ultraviolet (UV) radiation. Plastisol Dip Coating: A Comprehensive Guide to the Process Plastisol dip coating is a versatile and widelyRead More …
Plastisol PVC Liquid : flexible durable material in various industries
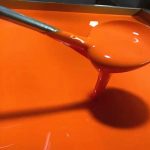
Plastisol PVC Liquid: A Comprehensive Guide Plastisol PVC Liquid, a versatile and widely used material, is a suspension of polyvinyl chloride (PVC) resin in a liquid plasticizer. This unique formulation offers a range of properties that make it suitable for various applications. Composition and Properties Plastisol PVC Liquid consists of PVC resin, plasticizers, stabilizers, and other additives. Plasticizers, such as phthalates or adipates, impart flexibility and softness to the material. Stabilizers prevent degradation and discoloration caused by heat, light, andRead More …
PVC plastisol coating for ultrasonic cleaning basket
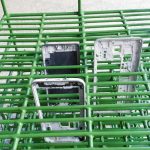
The PVC plastisol coating for the ultrasonic cleaning basket is a highly effective and innovative solution designed to enhance the performance and durability of the cleaning basket. This coating offers several notable benefits and features that make it a popular choice in the field of ultrasonic cleaning. One of the key advantages of the PVC plastisol coating is its excellent durability. It can withstand the rigors of frequent use and exposure to various cleaning solutions, ensuring a long service lifeRead More …
Manufacturing Process of Plastic Coating
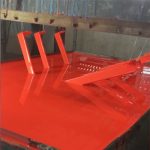
The previous chapters have provided an explanation of the similarities in operation between dip coating and dip molding. This chapter will now delve into the detailed procedures involved in both manufacturing process of plastic coating. Plastic Coating Pretreatment Process The pre-treatment step plays a crucial role in ensuring the proper application of plastic coating onto the metal substrate. These steps are vital for both processes. The pre-treatment process for dip coating is more intricate compared to dip molding, as itRead More …
An Overview of Dip Coating and Dip Molding
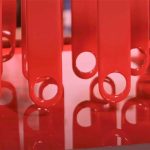
Process of Dip Coating and Dip Molding Dip Coating The process of fusing a plastic material onto a pre-existing metal piece is known as dip coating. The metal to be coated serves as a mold, allowing the plastic or polymer to adhere to it during the process. Prior to dipping, the parts (and sometimes entire pieces) intended for dipping are treated and preheated before being directly placed into the liquid polymer (e.g. PVC plastisol ). Upon cooling, the liquid polymerRead More …
- 1
- 2