ETPU Foaming Materials Have Some Shortcomings
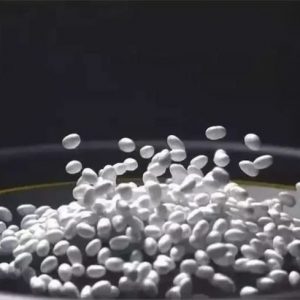
Traditional EVA foam materials have poor resilience, and after wearing for a period of time, the material will collapse and dent. Modifying the material with POE, rubber, and other materials can adjust and improve the material properties, but the improvement is limited. At the same time, there are issues such as high shrinkage and difficulty in molding. The production process uses chemical foaming, which not only causes pollution to the environment but also produces harmful residues to the human body.
ETPU foaming materials particles have ultra-light density, ultra-high resilience, and use supercritical carbon dioxide as foaming agent in the preparation process. They are made by pure physical foaming method, which is green, environmentally friendly, pollution-free, and without chemical residues. However, the current ETPU foaming materials still have the following shortcomings.
1.Currently, the foaming particle preparation technology is not mature enough, and the preparation of ETPU particles relies mostly on experience. The TPU foaming process and its mechanism are not well understood, and only a few companies can produce them in large quantities, which is far from meeting the market demand for ETPU foaming materials.
2.If TPU foaming particles are not subjected to post-forming treatment, the foaming particles will gradually shrink until they become compact. Currently, two forming methods have been proposed: rapid cooling forming method and pressure-holding air compensation method.
3.The faster the equipment depressurizes, the fuller and brighter the ETPU foamingmaterialsparticles will be, and the higher the rebound elasticity. Due to the inability of existing equipment to meet the high depressurization rate required for TPU foaming, further improvement of the foaming equipment is needed.
4. In the TPU heating foaming process, thermocouple heating rods are often used for heating, which results in uneven heating of the particles, leading to inconsistent sizes of ETPU particles. The prepared foamed particles have a higher density, rough surface, severe shrinkage, and poor resistance to yellowing and hydrolysis of the particles.
5.During the process of forming the midsole in ETPU footwear, the mainstream high-temperature steam welding molding method may result in incomplete welding and unclear surface patterns, especially for polyester-based TPU, which may undergo hydrolysis and turn yellow under high-temperature water vapor.
6.Currently, most of the prepared ETPU foaming materials particles are single-colored materials. There are two methods to achieve colored ETPU: direct dyeing of TPU foam with pigments or introducing dyed polyols to prepare colored TPU before foaming.
Direct dyeing of TPU foam with pigments presents a major and challenging issue, which is pigment migration leading to color variations in the final product. This is especially prominent in high-temperature water vapor molding, where the heating process further promotes the migration of small molecule dyes and exacerbates color variations.
Introducing dyed polyols to prepare colored TPU before foaming allows the dyes to disperse in a microscopic form within the polymer chains. With the help of coupling agents like silane, the dye molecules are grafted onto the polymer chains, preventing migration of the dye molecules within the TPU under high-temperature water vapor. However, this process involves material polymerization and has higher process difficulty.
Leave a Reply