Advantages and Disadvantages of ETPU Materials
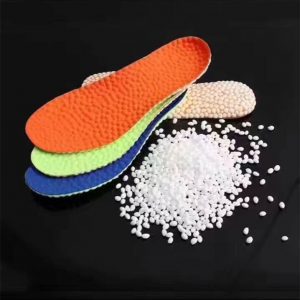
ETPU (thermoplastic polyurethane elastomer) is a thermoplastic elastomer material composed of polyether polyols and polyisocyanates. Here are the advantages and disadvantages of ETPU material:
Advantages:
1. Strong wear resistance: ETPU has higher hardness and strength than traditional rubber and plastic, so it has strong wear resistance and durability.
2. Oil and water resistance: ETPU has good oil and water resistance, and can be used for a long time in humid or oily environments without being easily damaged.
3. Good processability: ETPU material can be processed into various shapes of products through injection molding, extrusion, calendering and other processing methods, which can meet the needs of different applications.
4. Good elasticity: ETPU has good elasticity and resilience, which can effectively reduce impact and vibration, and protect items from damage.
5. Environmentally friendly: ETPU material is recyclable and environmentally friendly.
Disadvantages:
1. Higher price: Compared with traditional rubber and plastic materials, ETPU is more expensive.
2. Poor high temperature resistance: ETPU has poor high temperature resistance and cannot withstand long-term use at high temperatures.
3. Not resistant to ultraviolet rays: After being exposed to sunlight for a period of time, ETPU will become hard, brittle, and even lose its elasticity.
In summary, ETPU material has many advantages, especially in applications that require high strength, wear resistance, and elasticity. However, there are also some disadvantages to be aware of, such as higher price, poor high temperature resistance, and poor resistance to ultraviolet rays.
Leave a Reply