金属用プラスチックコーティング
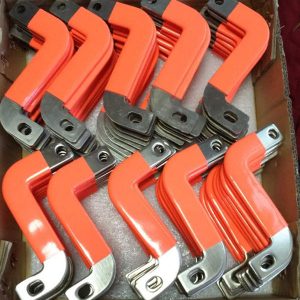
金属加工用プラスチックコーティングとは、金属部品の表面にプラスチックの層を施すことで、金属本来の特性を維持しながら、耐食性、耐摩耗性、電気絶縁性、自己絶縁性などのプラスチックの特性を付与します。 -潤滑。 このプロセスは、製品の適用範囲を拡大し、経済的価値を高める上で非常に重要な意味を持ちます。
金属のプラスチックコーティング方法
プラスチックのコーティングにはフレーム溶射などのさまざまな方法があります。 流動床 スプレー、粉体静電スプレー、ホットメルトコーティング、サスペンションコーティング。 コーティングに使用できるプラスチックの種類も数多くあります。 PVC、PE、PA が最も一般的に使用されます。 コーティングに使用されるプラスチックは粉末状であり、その細かさは 80 ~ 120 メッシュでなければなりません。
塗装後は冷水に浸けて急速に冷却するのがベストです。 急速冷却により、プラスチックコーティングの結晶化度が低下し、含水量が増加し、コーティングの靭性と表面の光沢が向上し、接着力が向上し、内部応力によって引き起こされるコーティングの剥離を克服できます。
コーティングと母材の密着性を向上させるには、コーティング前にワークピースの表面に埃がなく、錆やグリースが付着していない乾燥した状態にする必要があります。 ほとんどの場合、ワークピースには表面処理が必要です。 処理方法には、サンドブラスト、化学処理、その他の機械的方法が含まれます。 中でもサンドブラストは、ワークの表面を粗くして表面積を増やし、フックを形成することで密着性を向上させる効果があります。 サンドブラスト後、ワーク表面にきれいな圧縮空気を吹き付けてほこりを取り除き、6時間以内にプラスチックをコーティングする必要があります。そうしないと表面が酸化し、コーティングの密着性に影響します。
利点
粉末プラスチックを直接コーティングすることには、次のような利点があります。
- 粉末状でしか入手できない樹脂にも使用できます。
- 一度の塗布で厚い塗膜が得られます。
- 複雑な形状や鋭利なエッジの製品も良好にコーティングできます。
- ほとんどの粉末プラスチックは優れた保存安定性を持っています。
- 溶剤を必要としないため、材料の準備プロセスが簡単になります。 ただし、粉体塗装にはいくつかの欠点や制限もあります。 たとえば、ワークピースを予熱する必要がある場合、そのサイズは制限されます。 塗装に時間がかかるため、大型のワークの場合、溶射が完了していない状態で所定の温度以下になっている部分があります。 プラスチック粉体塗装プロセスでは、粉体損失が 60% に達する可能性があるため、経済的要件を満たすために粉体を回収して再利用する必要があります。
火炎溶射
金属用の火炎溶射プラスチックコーティングは、粉末またはペースト状のプラスチックをスプレーガンから放出される炎で溶融または部分的に溶融し、溶融したプラスチックを対象物の表面に吹き付けてプラスチックコーティングを形成するプロセスです。 コーティングの厚さは通常 0.1 ~ 0.7 mm です。 溶射に粉末プラスチックを使用する場合、ワークピースを予熱する必要があります。 予熱はオーブンで行うことができ、予熱温度はさまざまですepeスプレーされるプラスチックの種類を確認します。
スプレー中の火炎温度は厳密に制御する必要があります。温度が高すぎるとプラスチックが燃えたり損傷したりする可能性があり、温度が低すぎると接着に影響を与える可能性があります。 一般に、プラスチックの最初の層をスプレーするときの温度は最も高く、金属とプラスチックの間の接着を向上させることができます。 後続の層がスプレーされると、温度がわずかに低下する可能性があります。 スプレーガンとワーク間の距離は 100 ~ 200 cm にしてください。 平らなワークピースの場合、ワークピースを水平に置き、スプレーガンを前後に動かす必要があります。 円筒形または内径のワークピースの場合、回転スプレー用に旋盤に取り付ける必要があります。 回転するワークの線速度は 20 ~ 60 m/min にしてください。 必要な厚さのコーティングが達成されたら、スプレーを停止し、溶融プラスチックが固化するまでワークピースを回転させ続け、その後急速に冷却する必要があります。
火炎溶射は生産効率が比較的低く、刺激性ガスを使用するため、他の工法に比べて設備投資が少なく、タンクや容器、大型ワークの内面の塗装に有効であることから、依然として産業界では重要な加工法となっている。 。
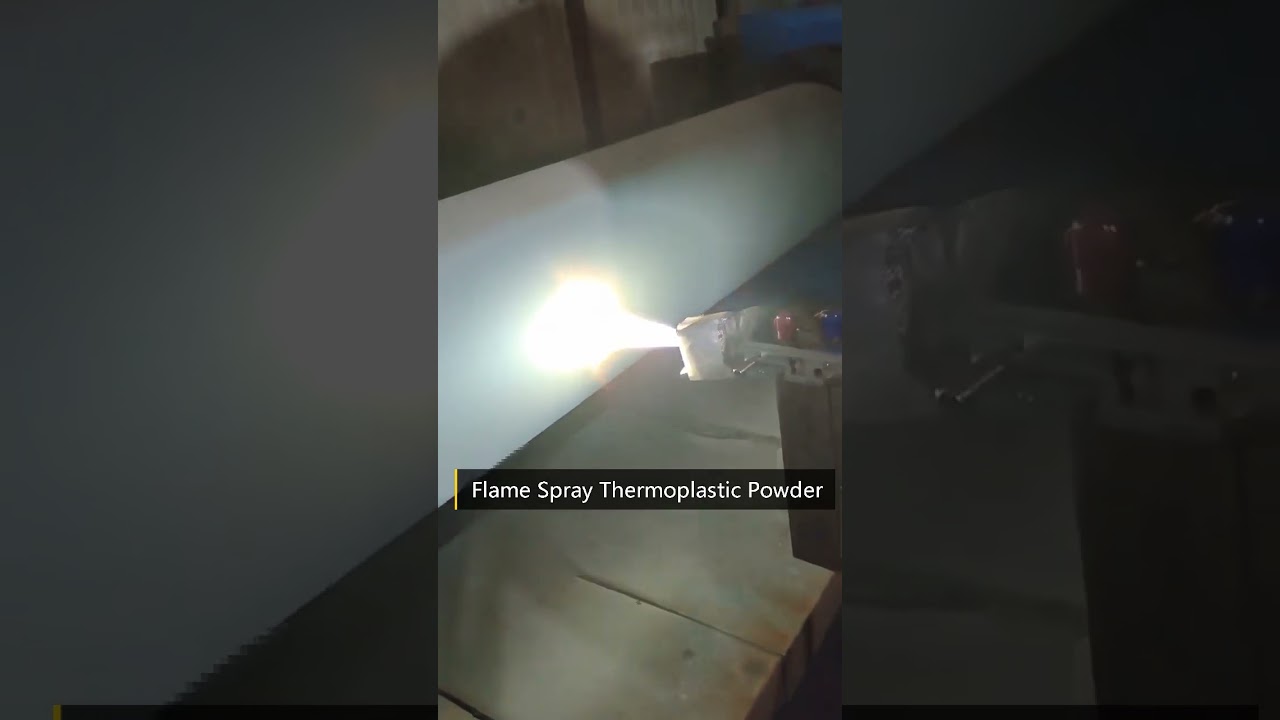
流動層ディッププラスチックコーティング
金属用の流動層浸漬プラスチックコーティングの動作原理は次のとおりです。プラスチックコーティング粉末は、粉末ではなく空気のみを通過させる多孔質の隔壁を上部に備えた円筒形の容器に入れられます。 容器の底から圧縮空気が入ると粉体が吹き上げられ、容器内に浮遊します。 予熱したワークを浸漬すると樹脂粉末が溶けてワークに付着し、被膜を形成します。
流動層で得られるコーティングの厚さ depe温度、比熱容量、表面係数、スプレー時間、ワークピースが流動チャンバーに入るときに使用されるプラスチックの種類が決まります。 ただし、プロセス内で制御できるのはワークピースの温度とスプレー時間だけであり、これらは生産時の実験によって決定する必要があります。
浸漬中、プラスチック粉末は、凝集、渦流、またはプラスチック粒子の過剰な分散がなく、スムーズかつ均一に流れることが要求されます。 これらの要件を満たすためには、対応する措置を講じる必要があります。 撹拌装置を追加すると凝集と渦流を減らすことができます。一方、少量のタルカムパウダーをプラスチックパウダーに添加すると流動化には有益ですが、コーティングの品質に影響を与える可能性があります。 プラスチック粒子の飛散を防ぐには、空気流量とプラスチック粉末粒子の均一性を厳密に制御する必要があります。 ただし、ある程度の分散は避けられないため、流動層上部に回収装置を設置する必要があります。
流動層ディッププラスチックコーティングの利点は、複雑な形状のワークピースをコーティングできること、高いコーティング品質、一度の塗布でより厚いコーティングが得られること、最小限の樹脂損失、およびクリーンな作業環境です。 デメリットは、大きなワークの加工が難しいことです。
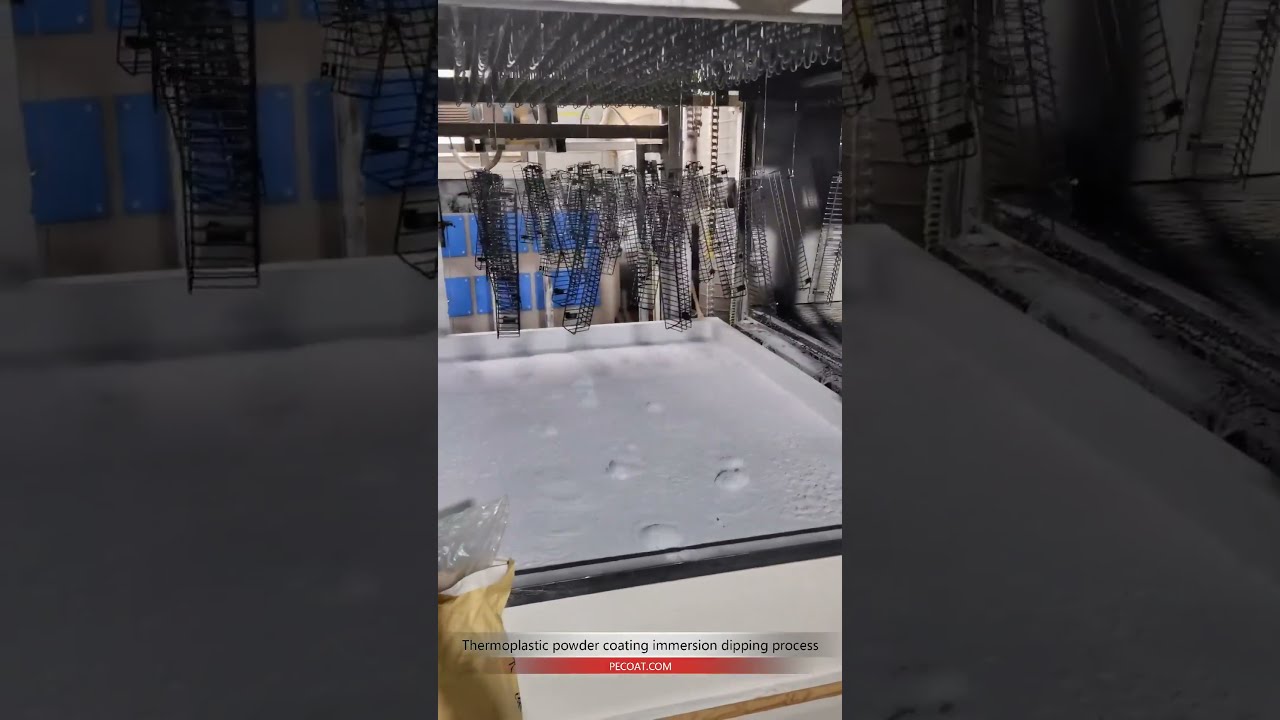
金属用静電溶射プラスチックコーティング
静電スプレーでは、溶融や焼結ではなく、静電力によって樹脂プラスチックコーティング粉末をワークピースの表面に固定します。 原理は、高電圧静電発生装置が形成する静電場を利用して、スプレーガンから噴霧された樹脂粉体に静電気を帯電させ、接地されたワークが高電圧のプラス極となります。 その結果、均一なプラスチック粉末の層がワークピースの表面に急速に堆積します。 電荷が消える前に粉体層がしっかりと密着します。 加熱および冷却後、均一なプラスチックコーティングが得られます。
粉末静電スプレーは 1960 年代半ばに開発され、自動化が容易です。 静電塗装は塗膜を厚くする必要がない場合、ワークの予熱が不要なため、熱に弱い材料や加熱に適さないワークにも使用できます。 また、流動層スプレーに不可欠な大型の保管容器も必要ありません。 ワークを迂回した粉体はワークの裏側に引き寄せられるため、他のスプレー方法に比べてオーバースプレーの量が少なく、片面スプレーでワーク全体を塗装できます。 ただし、大きなワークピースの場合は、依然として両側からスプレーする必要があります。
異なる断面を持つワークピースは、その後の加熱に困難を引き起こす可能性があります。 断面積の差が大きすぎる場合、コーティングの厚い部分は溶融温度に達しない可能性があり、一方、薄い部分はすでに溶融または劣化している可能性があります。 この場合、樹脂の熱安定性が重要になります。
きれいな内部コーナーと深い穴を持つコンポーネントは、これらの領域が静電シールドされているため、静電スプレーで簡単に覆われません。epel 粉末が付着すると、スプレーガンが角や穴に挿入できない限り、コーティングが隅や穴に入るのが妨げられます。 さらに、静電スプレーでは、粒子が大きいほどワークピースから剥がれやすく、150 メッシュより細かい粒子の方が静電作用がより効果的であるため、より微細な粒子が必要です。
ホットメルトコーティング法
ホットメルトコーティング法の動作原理は、スプレーガンを使用して予熱されたワークピースにプラスチックコーティングパウダーをスプレーすることです。 ワークの熱を利用してプラスチックが溶け、冷却後、ワークにプラスチックのコーティングを施すことができます。 必要に応じて後加熱処理も必要となります。
ホットメルトコーティングプロセスを制御する鍵となるのは、ワークピースの予熱温度です。 予熱温度が高すぎると、金属表面の酸化が著しく、コーティングの密着性が低下し、さらには樹脂の分解やコーティングの発泡や変色を引き起こす可能性があります。 予熱温度が低すぎると樹脂の流動性が悪くなり、均一な塗膜が得られにくくなる。 多くの場合、ホットメルトコーティング法の 170 回のスプレー塗布では所望の厚さを達成できないため、複数回のスプレー塗布が必要になります。 各スプレー塗布後、200 番目の層を塗布する前に、コーティングを完全に溶かして光沢を出すために加熱処理が必要です。 これにより、均一で滑らかなコーティングが保証されるだけでなく、機械的強度も大幅に向上します。 推奨加熱処理温度は、高密度ポリエチレンの場合は1℃程度、塩素化ポリエーテルの場合はXNUMX℃程度で、推奨時間はXNUMX時間です。
ホットメルトコーティング法は、樹脂の損失を最小限に抑えながら、高品質で見た目にも美しい、強力に結合したコーティングを生成します。 管理が簡単で、臭いも最小限で、使用するスプレーガンも臭いがありません。
金属のプラスチックコーティングに利用可能な他の方法
1. スプレー: スプレーガンのリザーバーに懸濁液を充填し、ゲージ圧 0.1 MPa 以下の圧縮空気を使用して、コーティングをワークピースの表面に均一にスプレーします。 サスペンションの損失を最小限に抑えるには、空気圧をできるだけ低く保つ必要があります。 ワークピースとノズル間の距離は 10 ~ 20 cm に維持し、スプレー面は材料の流れの方向に対して垂直に保つ必要があります。
2. 浸漬: ワークピースをサスペンションに数秒間浸漬し、その後取り出します。 この時点で、懸濁液の層がワークピースの表面に付着し、余分な液体は自然に流れ落ちます。 外面を完全にコーティングする必要がある小型ワークに適した工法です。
3. ブラッシング: ブラッシングでは、ペイントブラシまたはブラシを使用して懸濁液をワークピースの表面に塗布し、コーティングを作成します。 刷毛塗りは一般的な局所塗装や狭い面への片面塗装に適しています。 ただし、コーティングが乾燥した後の表面は滑らかで均一ではなくなり、各コーティング層の厚さには制限があるため、ほとんど使用されません。
4. 注ぐ: 回転している中空のワークピースにサスペンションを注ぎ、内面がサスペンションで完全に覆われていることを確認します。 その後、余分な液体を注ぎ出してコーティングを形成します。 この方法は、小型反応器、パイプライン、エルボ、バルブ、ポンプ ケーシング、ティー、およびその他の同様のワークピースのコーティングに適しています。
金属線用の熱可塑性コーティングを探しています
このインターネット サイトは私のインスピレーションであり、本当に優れたレイアウトと完璧なコンテンツです。
これは私にとって非常に重要な情報の 1 つだと思います。そしてあなたの記事を読んで幸せです。しかし、いくつかの普通のことについて述べたいと思います。サイトのテイストは完璧で、記事は実際に素晴らしいです : D. お疲れ様でした、乾杯