Thermoplastic Materials In Different Types
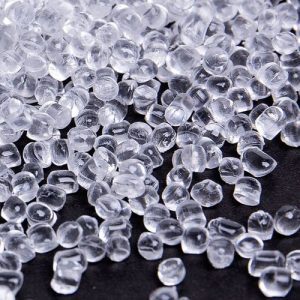
Introduction
Thermoplastic materials are a type of polymer that can be melted and re-molded multiple times without undergoing any significant chemical change. They are widely used in various industries due to their unique properties and versatility.
One of the most significant advantages of thermoplastic materials is their ability to be molded into complex shapes with ease. This makes them ideal for use in manufacturing processes where intricate designs are required. Additionally, thermoplastics are lightweight and have excellent resistance to impact, making them suitable for use in applications where durability is essential.
Another advantage of thermoplastic materials is their ability to be recycled. Unlike thermosetting materials, which undergo a chemical change during the curing process, thermoplastics can be melted and re-molded multiple times without losing their properties. This makes them an environmentally friendly option for manufacturers who want to reduce their carbon footprint.
There are many different types of thermoplastic materials, each with their own unique properties and characteristics. In this answer, we will discuss some of the most common types of thermoplastics and their properties.
1. Polyethylene (PE):
Polyethylene is a lightweight, durable, and flexible plastic that is commonly used in packaging, construction, and automotive applications. It is available in several different grades, including high-density polyethylene (HDPE) and low-density polyethylene (LDPE). HDPE is a strong and rigid plastic that is resistant to chemicals and moisture, while LDPE is more flexible and has better impact resistance.
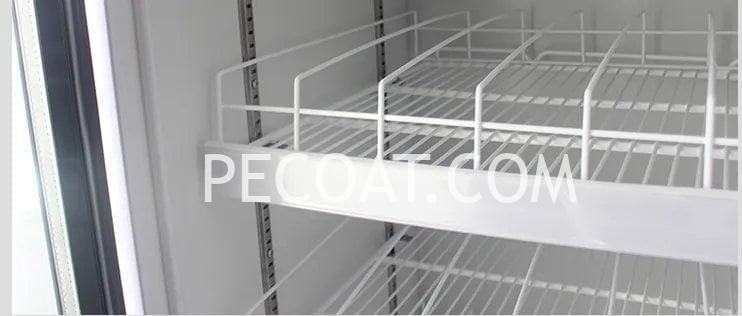
2. Polypropylene (PP):
Polypropylene is a tough, rigid plastic that is resistant to heat, chemicals, and moisture. It is commonly used in packaging, automotive parts, and household appliances. It is available in several different grades, including homopolymer, copolymer, and random copolymer. Homopolymer is the most common grade and has good stiffness and temperature resistance, while copolymer has better impact resistance and random copolymer has better clarity.
3. Polystyrene (PS):
Polystyrene is a lightweight, rigid plastic that is commonly used in packaging, insulation, and disposable tableware. It is available in several different grades, including general-purpose polystyrene (GPPS) and high-impact polystyrene (HIPS). GPPS is a clear and brittle plastic that is used in applications where transparency is important, while HIPS is a more impact-resistant plastic that is used in applications where toughness is important.
4. Polyvinyl chloride (PVC):
Polyvinyl chloride is a versatile plastic that is used in a wide range of applications, including construction, automotive parts, and medical devices. It is available in several different grades, including rigid PVC and flexible PVC. Rigid PVC is a strong and durable plastic that is used in applications where stiffness is important, while flexible PVC is a softer and more flexible plastic that is used in applications where flexibility is important.
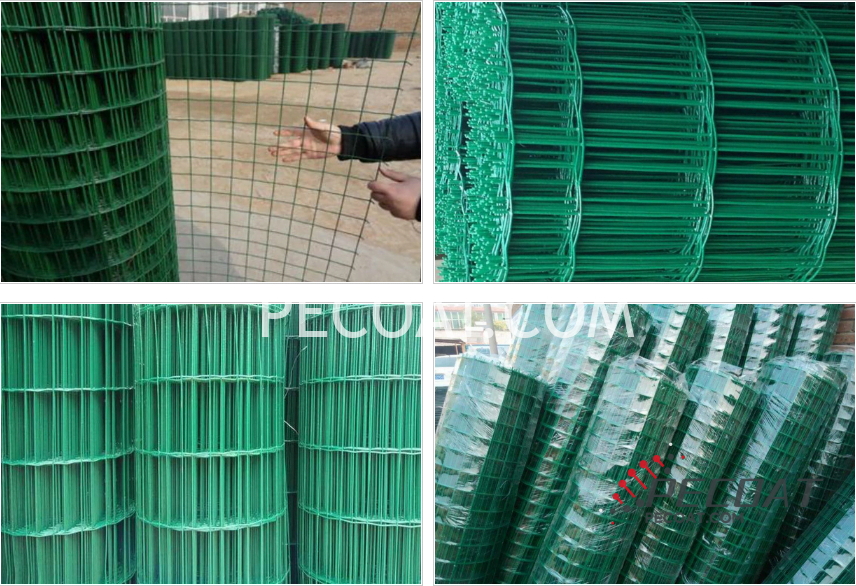
5. Acrylonitrile-butadiene-styrene (ABS):
ABS is a tough, rigid plastic that is commonly used in automotive parts, toys, and electronic housings. It is a blend of three different polymers: acrylonitrile, butadiene, and styrene. ABS has good impact resistance, heat resistance, and chemical resistance.
6. Polycarbonate (PC):
Polycarbonate is a strong, transparent plastic that is commonly used in electronic components, automotive parts, and medical devices. It has excellent impact resistance, heat resistance, and optical clarity. It is also resistant to UV radiation and chemicals.
7. Nylon (PA):
Nylon is a strong, lightweight plastic that is commonly used in automotive parts, sporting goods, and electrical components. It is available in several different grades, including nylon 6 and nylon 66. Nylon 6 is a more flexible plastic that is used in applications where toughness and flexibility are important, while nylon 66 is a more rigid plastic that is used in applications where stiffness and strength are important.
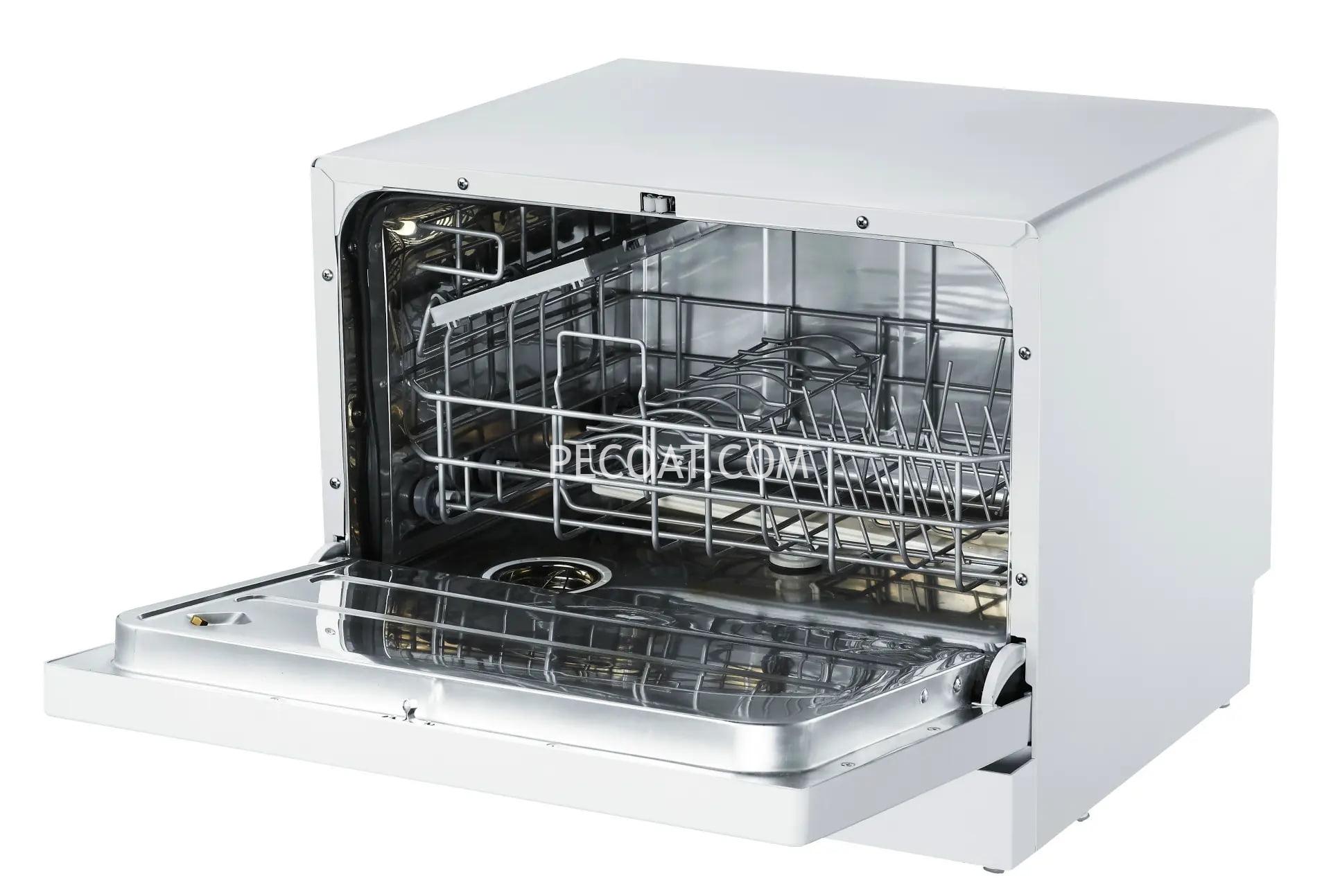
8. Acetal (POM):
Acetal is a strong, rigid plastic that is commonly used in gears, bearings, and other mechanical parts. It has good dimensional stability, low friction, and excellent wear resistance. It is available in several different grades, including homopolymer and copolymer. Homopolymer has better mechanical properties, while copolymer has better chemical resistance.
9. Thermoplastic elastomers (TPE):
TPEs are flexible, rubber-like materials that are commonly used in automotive parts, footwear, and consumer products. They are a blend of two different polymers: a thermoplastic and an elastomer. TPEs have good flexibility, low compression set, and good chemical resistance.
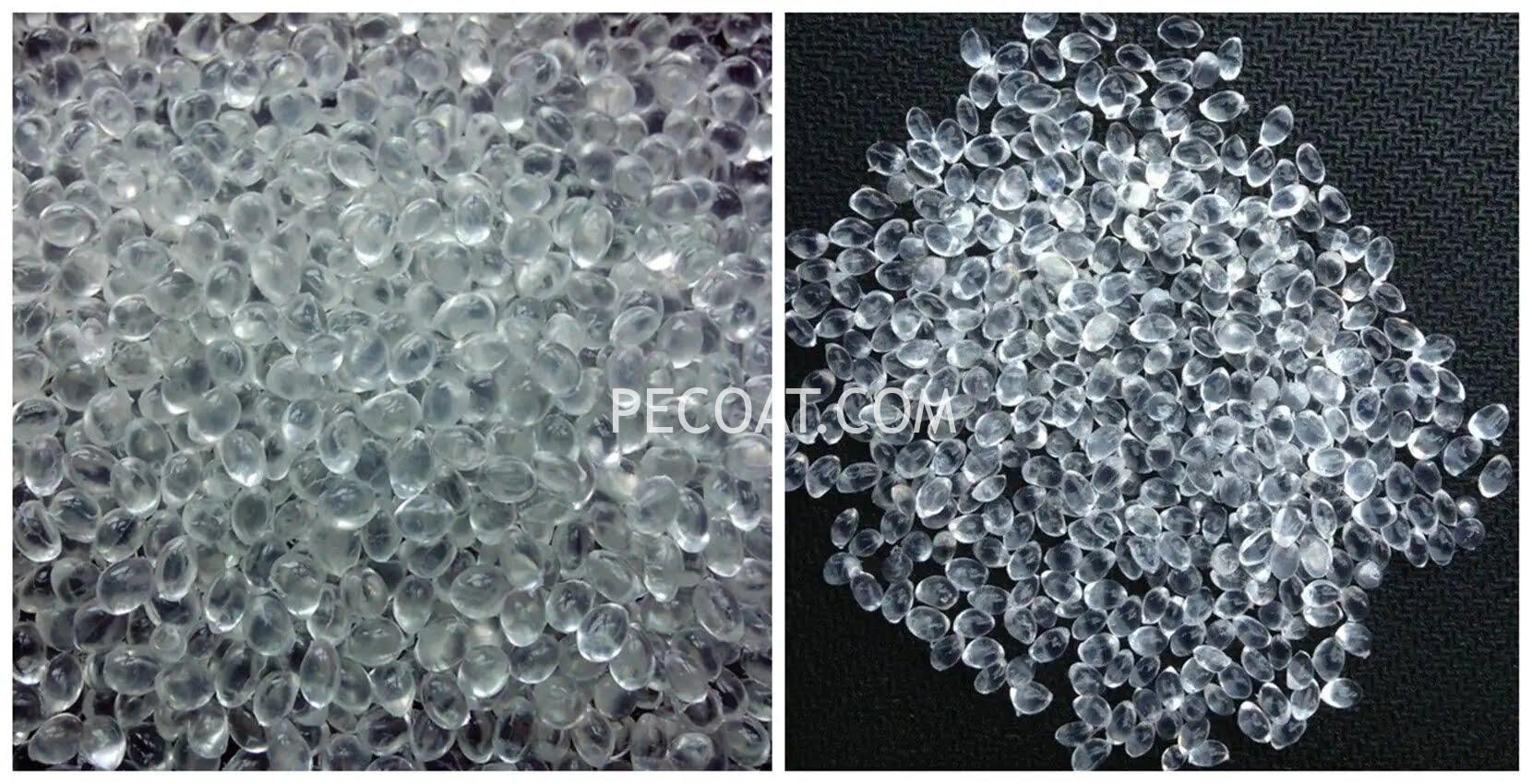
In addition to their unique properties, thermoplastic materials are also easy to process and can be molded using a variety of techniques, including injection molding, blow molding, and extrusion. This makes them an ideal choice for manufacturers who need to produce large quantities of parts quickly and efficiently.
Despite their many advantages, there are also some limitations to using thermoplastic materials. For example, they have a lower heat resistance than thermosetting materials, which can limit their use in high-temperature applications. Additionally, some thermoplastics can be brittle and prone to cracking under stress.
In conclusion, thermoplastic materials are a versatile and widely used type of polymer that offer many advantages over other materials. They are lightweight, durable, and easy to process, making them an ideal choice for a wide range of applications. With their ability to be recycled, they are also an environmentally friendly option for manufacturers who want to reduce their carbon footprint.
Leave a Reply