Category: Thermoplastic Powder Paint
Thermoplastic powder paint is a type of coating process that involves applying a dry powder paints of thermoplastic material onto a substrate, usually a metal surface. The powder is heated until it melts and forms a continuous, protective coating. This coating process can be done using several techniques, including electrostatic spraying and fluidized bed dipping.
Thermoplastic powder paints offers several advantages over traditional liquid coatings, including:
- Durability: Thermoplastic paints are highly durable and resistant to impact, abrasion, and chemicals, making them ideal for use in harsh environments.
- Ease of application: Thermoplastic powder paints can be applied more easily and uniformly than liquid coatings, which can help to reduce material waste and improve efficiency.
- Cost-effectiveness: Because thermoplastic paints can be applied more efficiently, they can often be less expensive than liquid coatings in the long run.
- Environmental friendliness: Thermoplastic paints are free of volatile organic compounds (VOCs), which can make them a more environmentally friendly alternative to liquid coatings.
Common types of thermoplastic powder paint used for coating include polyethylene, polypropylene, nylon, and PVC. Each type of powder has its unique properties and is suitable for different applications, depending on the specific requirements of the substrate being coated.
Buy PECOAT® PE Thermoplastic Polyethylene Powder Paint
Fluidized Bed Dipping Process
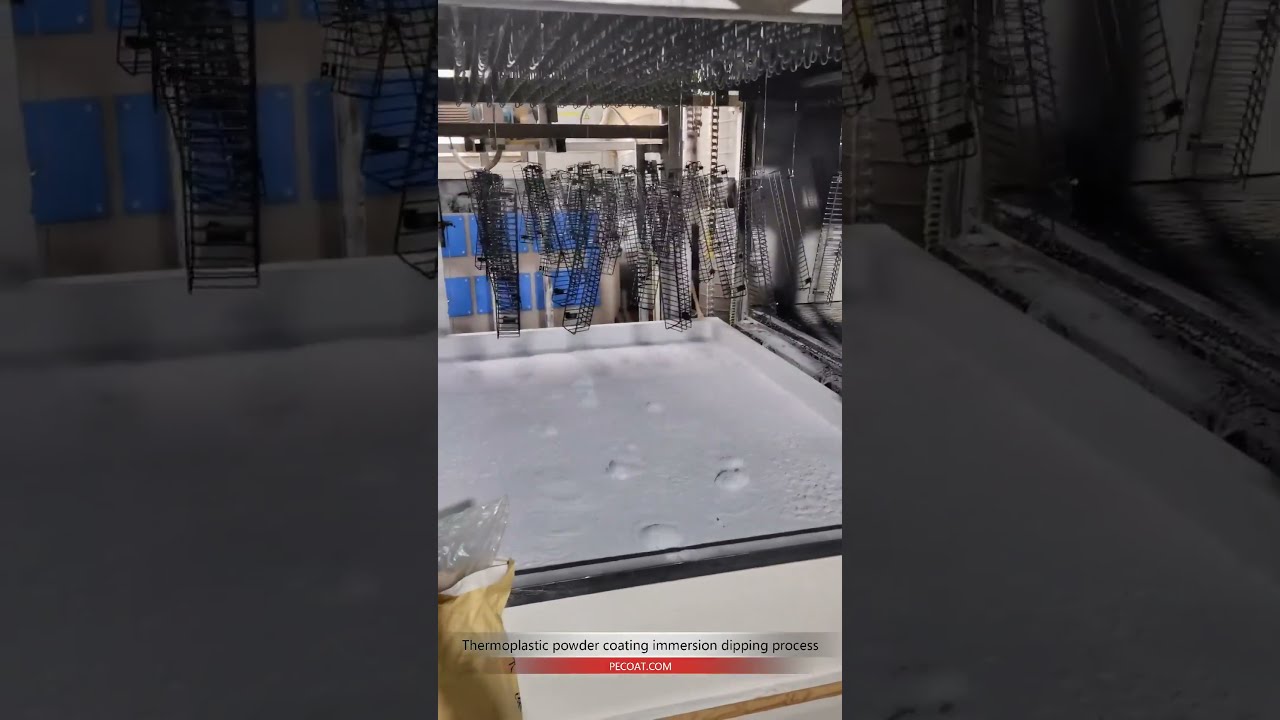
What is Polyethylene (PE) Powder Coating?
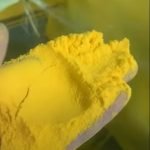
Polyethylene (PE) powder coating is a specialized surface finishing technique that utilizes thermoplastic polyethylene resin in powder form. Applied through electrostatic spray deposition or fluidized bed processes, this coating is cured under heat to form a durable, protective layer. While less common than epoxy or polyester powder coatings, PE offers unique benefits in specific applications, leveraging its chemical resistance, flexibility, and cost-effectiveness. This article explores the composition, application processes, properties, advantages, limitations, and industrial uses of PE powder coating. CompositionRead More …
Conversion between Shore(SH) Hardness and Mohs(MH) Hardness
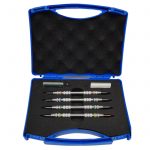
Shore hardness and Mohs hardness are two main methods for measuring the hardness of substances. The conversion relationship between them is as follows: I. Basic Concepts Shore hardness(SH): Also known as gravitational hardness, it is an index for measuring the hardness of a substance according to the deformation depth produced by the substance against gravity. Mohs hardness(MH): Also known as repulsive hardness, it is a testing method for calculating hardness by applying a indenter to the surface of an objectRead More …
Is PP Material Food Grade?
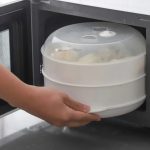
The PP (polypropylene) material can be classified into food grade and non-food grade categories. Food grade PP is extensively utilized in the food industry due to its safety, non-toxicity, excellent resistance to low and high temperatures, as well as its high strength folding resistance. This material finds application in the production of specialized plastic bags for food, food plastic boxes, food straws, and other related products. Moreover, it is also safe for use in microwave ovens. However, not all PPRead More …
Sandblasting vs Powder Coating: What’s the Difference?
Sandblasting and powder coating are two common methods used in the surface preparation and finishing of various materials. In this article, we will explore these two methods in detail, including their processes, advantages, and disadvantages. Sandblasting Sandblasting, also known as abrasive blasting, is a process that involves the use of high-pressure air or water to propel abrasive materials such as sand, glass beads, or steel shot onto a surface to remove contaminants, rust, or old coatings. The process is typicallyRead More …
Shore Hardness ACD Conversion and Difference
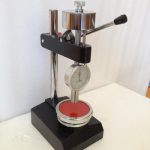
Shore Hardness Concept The Shore scleroscope hardness (Shore), initially proposed by British scientist Albert F. Shore, is commonly referred to as HS and serves as a standard for measuring material hardness. The Shore hardness tester is suitable for determining the Shore hardness value of both ferrous and non-ferrous metals, with the hardness value representing the extent of elastic deformation exhibited by the metal. This term is frequently used in the rubber and plastic industry. Test Method The Shore hardness testerRead More …
Why thermoplastic powder does not bubble in fluidized bed?
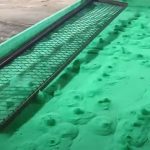
Why thermoplastic powder does not bubble when boiled up in fluidized bed? There may be several reasons for this issue: The Quality Of Thermoplastic Powder If the particle size is inconsistent, there is excessive water content, impurities or aggregates present, it will affect the fluidity and suspension of the powder . Consequently, it becomes difficult for the powder to generate bubbles or maintain stability in the fluidized bed. Air Pressure And Airflow Insufficient or excessive air pressure and flow disruptsRead More …
Preheating Temperature Control In Fluidized Bed Dipping Process
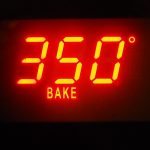
Background Introduction In fluidized bed dipping process, the workpiece’s heat capacity is utilized to melt the thermoplastic powder and achieve the desired coating thickness and quality. Therefore, determining the appropriate preheating temperature of the workpiece is crucial. The preheating temperature should be slightly higher than the melting temperature of thermoplastic powder. If it is too high, flow defects may occur due to excessively thick coatings or polymer resin cracking, resulting in bubbles, yellowing or burning. Conversely, if it is too low,Read More …
Plastic Coating Powder is a Versatile and Efficient Solution
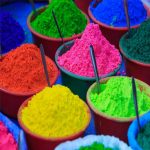
What is plastic coating powder? Plastic coating powder, also known as powder coating, is a dry finishing process used to apply a protective and decorative layer onto various surfaces. It is commonly used in industries such as automotive, furniture, and appliances. The powder coating process involves applying a fine powder made of thermoplastic or thermosetting polymers onto a substrate. The powder is electrostatically charged and then sprayed onto the surface, where it adheres due to the electrostatic attraction. The coatedRead More …
Polyolefin Polyethylene PO/PE lining Coating Powder for Steel Lining
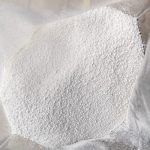
Plastic coating lined steel pipe is based on ordinary carbon steel pipe, with chemically excellent thermoplastic lining. It is formed by cold drawing compound or rolling molding. It has both the mechanical properties of steel pipe and the corrosion resistance of plastic pipe. It has the characteristics of scale inhibition, resistance to microbial growth, making it an ideal pipeline for transporting acid, alkali, salt, corrosive gases, and other media. The thermoplastic coatings commonly used for lining are PO, PE, PP,Read More …
Main Uses of Polyvinyl Chloride (PVC)
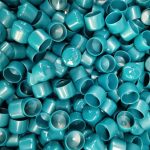
Polyvinyl chloride (PVC) is a versatile synthetic polymer that finds numerous applications across various industries. Here are some of the main uses of Polyvinyl chloride PVC: 1. Construction: PVC is extensively used in the construction industry for pipes, fittings, and plumbing systems. Its excellent durability, corrosion resistance, and low cost make it a popular choice for water supply and drainage systems. 2. Electrical and Electronics: PVC is widely used in electrical cables and wiring due to its excellent insulation properties.Read More …