Powder dip coating offers several advantages
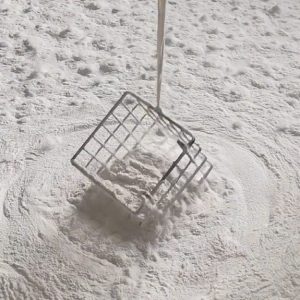
The process of powder dip coating
Powder dip coating is a coating method in which the substrate is immersed in a powder coating material to achieve coating. This process involves several steps to ensure the uniform application and proper adhesion of the coating.
The first step in powder dip coating is to prepare the substrate. The substrate may need to be cleaned, degreased, and roughened to enhance the adhesion of the powder coating. Any contaminants or debris on the surface can affect the coating’s adhesion and quality.
Once the substrate is prepared, it is heated to a specific temperature. Heating the substrate helps to improve the powder’s adherence and promotes better coating uniformity. The exact temperature required depends on the type of powder coating and the substrate being coated.
Next, the substrate is dipped into a container filled with the powder coating material. As the substrate is withdrawn from the powder coating container, the powder adheres to the surface. The dipping process can be repeated one or more times to build up the desired coating thickness.
After dipping, the excess powder is removed from the substrate. This can be done using air blowers, vibration, or other techniques to remove the loose powder that did not adhere to the substrate. Removing the excess powder helps to achieve a smooth and uniform coating.
The coated substrate then enters a curing stage. Curing is typically done by heating the substrate in an oven or using other heating methods. The heat causes the powder coating to melt, flow, resulting in a hard and durable coating. The curing time and temperature depend on the specific powder coating formulation and the thickness of the coating.
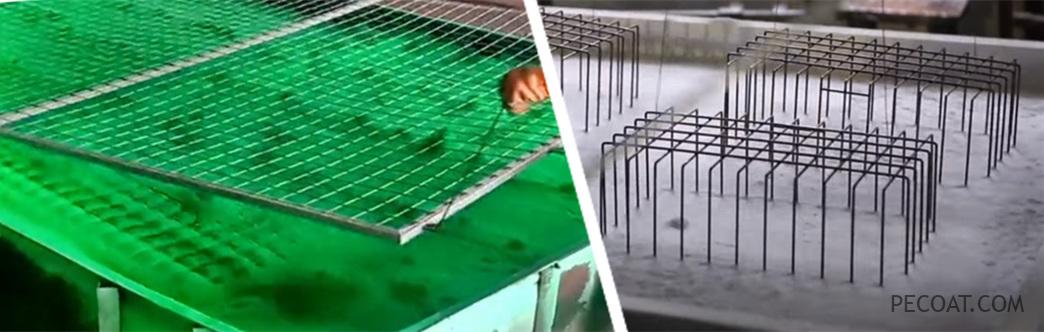
Advantages
Powder dip coating offers several advantages over other coating methods. One of the main advantages is the ability to achieve a uniform coating thickness throughout the substrate. This is particularly important in applications where consistent coating properties are crucial, such as electrical insulation or corrosion protection. Additionally, powder coatings provide good durability, resistance to scratching, fading, and chemical exposure.
Another advantage of powder dip coating is its efficiency. The coating process can be automated, allowing for high-volume production. The powder coating material can be recycled and reused, reducing waste and costs. Powder coatings also have low volatile organic compound (VOC) emissions, making them more environmentally friendly compared to some solvent-based coatings.
Powder dip coating finds applications in various industries. It is commonly used in the automotive, electronics, and household appliance industries for coating small components, such as screws, nuts, and brackets. The coating provides protection against corrosion, improves electrical insulation, and enhances the appearance of the components. Powder dip coating is also used in the manufacturing of medical devices, where a clean and sterile coating is required.
In summary, powder dip coatings is a coating method that offers uniform coating thickness, durability, and efficiency. By immersing the substrate in the powder coating material and subsequent curing, a hard and protective coating is achieved. The process is widely used in industries where coating small parts or components is necessary, providing enhanced performance and aesthetic appeal. The specific requirements and application areas may vary, but powder dip coating continues to be a popular choice for many coating applications.

Leave a Reply