Thermoplastic Powder Paint – Supplier,Develope,Pros and Cons
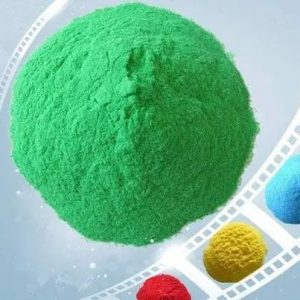
Supplier
China PECOAT® specialized in production and export of thermoplastic powder paint, the product has polyethylene powder paint, pvc powder paint, nylon powder paint, and fluidized bed dipping equipment.
Development History of Thermoplastic Powder Paint
Since the oil crisis in the 1970s, powder coatings have rapidly developed due to their resource conservation, environmental friendliness, and suitability for automated production. Thermoplastic powder paint ( also called thermoplastic powder coating), one of the two main types of powder paint, started to emerge in the late 1930s.
In the 1940s, with the development of the petrochemical industry and other industries, the production of resins such as polyethylene, polyvinyl chloride, and polyamide resin rapidly increased, leading to the research of thermoplastic powder paint. Initially, people wanted to use the good chemical resistance of polyethylene to apply it to metal coating. However, polyethylene is insoluble in solvents and cannot be made into solvent-based coatings, and suitable adhesives were not found to stick the polyethylene sheet to the metal inner wall. Therefore, flame spraying was used to melt and coat the polyethylene powder on the metal surface, thus opening the beginning of thermoplastic powder paint.
Fluidized bed coating, which is currently the most widely used and common coating method for thermoplastic powder paint, began with the direct sprinkling method in 1950. In this method, resin powder is evenly sprinkled on the heated surface of the workpiece to form a coating. In order to make the sprinkling method automated, the fluidized bed coating method was successfully tested in Germany in 1952. The fluidized bed coating method uses air or inert gas blown into the porous permeable plate at the bottom of the fluidized bed to form a uniformly distributed scattered airflow, which makes the powder in the fluidized bed flow into a state close to fluid, so that the workpiece can be evenly distributed on the surface of the workpiece and obtain a smooth and flat surface.
The Types and Pros and Cons of Thermoplastic Powder Paint
Currently, thermoplastic powder paint include various types such as polyethylene/polypropylene powder coatings, polyvinyl chloride powder coatings, nylon powder coatings, polytetrafluoroethylene powder coatings, and thermoplastic polyester powder coatings. They have been widely used in traffic protection, pipeline anti-corrosion, and various household items.
Polyethylene (PE) and polypropylene (PP) powder coating
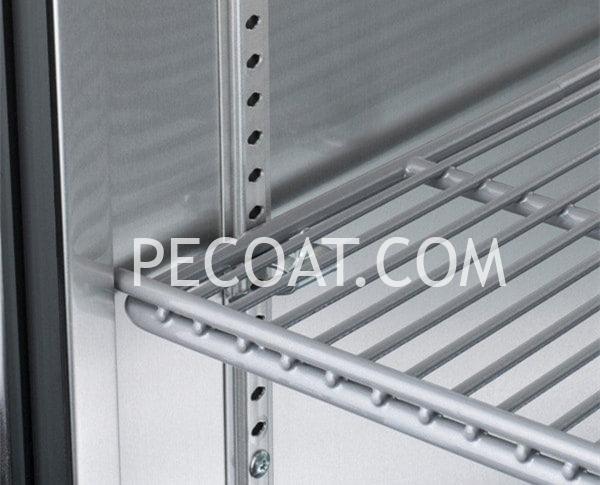
Polyethylene and polypropylene were among the first materials used in thermoplastic powder paint and were the two most important thermoplastic polymers in the last century. Currently, both high-density and low-density polyethylene have been applied in the thermoplastic field. High-density polyethylene is usually used in the industrial field, while low-density polyethylene is used in the civil field.
As the molecular chain of polyethylene and polypropylene is a carbon-carbon bond, both have non-polar characteristics of olefins, so polyethylene and polypropylene powder coatings have good chemical resistance and are widely used in the anti-corrosion field. They are used to protect, store, and transport containers, pipes, and oil pipelines for chemicals and chemical reagents. As an inert material, this kind of powder paint has poor adhesion to the substrate and requires strict surface treatment of the substrate, or the application of primer or modification of polyethylene with other materials.
Advantage
Polyethylene resin is the most widely used and produced thermoplastic powder paint.
It has the following advantages:
- Excellent water resistance, acid and alkali resistance, and chemical resistance;
- Good electrical insulation and thermal insulation properties;
- Excellent tensile strength, flexibility, and impact resistance;
- Good low-temperature resistance, can maintain 400 hours without cracking at -40℃;
- The relative price of raw materials is low, non-toxic and environmentally friendly.
Disadvantage
However, due to the properties of the substrate polyethylene, polyethylene powder paint also have some unavoidable drawbacks:
- The hardness, wear resistance, and mechanical strength of the coating are relatively poor;
- The adhesion of the coating is poor and the substrate needs to be strictly treated;
- Poor weather resistance, prone to stress cracking after exposure to ultraviolet rays;
- Poor high-temperature resistance and poor resistance to humid heat.
Polyvinyl chloride (PVC) powder coating
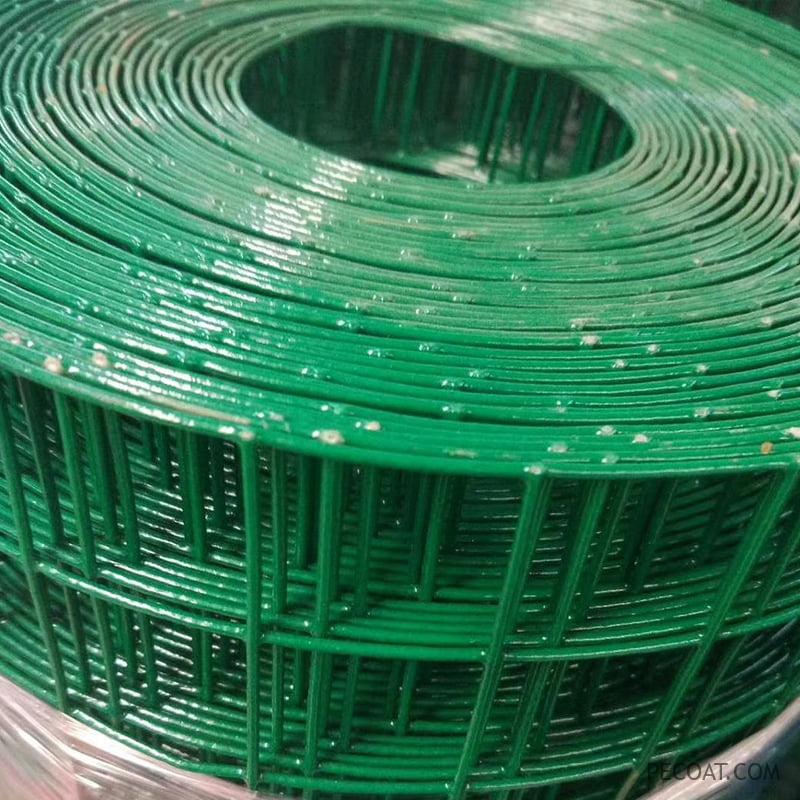
Polyvinyl chloride (PVC) is an amorphous polymer containing a small amount of incomplete crystals. Most PVC resin products have molecular weights between 50,000 and 120,000. Although high molecular weight PVC resins have better physical properties, low molecular weight PVC resins with lower melt viscosity and softening temperature are more suitable as materials for thermoplastic powder paint.
PVC itself is a rigid material and cannot be used as a powder paint material alone. When making coatings, a certain amount of plasticizer needs to be added to adjust the flexibility of PVC. At the same time, adding plasticizers also reduces the material’s tensile strength, modulus, and hardness. Choosing the appropriate type and amount of plasticizer can achieve the desired balance between material flexibility and hardness.
For a complete PVC powder paint formula, stabilizers are also an essential part. To solve the thermal stability of PVC, mixed salts of calcium and zinc with good thermal stability, barium and cadmium soaps, mercaptan tin, dibutyltin derivatives, epoxy compounds, etc. have been developed. Although lead stabilizers have excellent thermal stability, they have been phased out of the market due to environmental reasons.
Currently, the most used products for PVC powder paint are various household appliances and dishwasher racks. PVC products have good wash resistance and resistance to food contamination. They can also reduce noise for dish racks. Dish racks coated with PVC products will not make noise when placing tableware. PVC powder coatings can be applied by fluidized bed construction or electrostatic spraying, but they require different powder particle sizes. It should also be noted that PVC powder paint emit a pungent odor during immersion coating and are harmful to the human body. Their use has already started to be prohibited in foreign countries.
Advantage
The advantages of polyvinyl chloride powder paint are:
- Low raw material prices;
- Good pollution resistance, wash resistance, and corrosion resistance;
- High mechanical strength and good electrical insulation performance.
Disadvantage
The disadvantages of polyvinyl chloride powder paint are:
- The temperature difference between the melting temperature and decomposition temperature of PVC resin is small. During the coating process, the temperature needs to be strictly controlled to prevent the coating from decomposing.
- The coating is not resistant to aromatic hydrocarbons, esters, ketones, and chlorinated solvents, etc.
Polyamide (nylon) powder coating
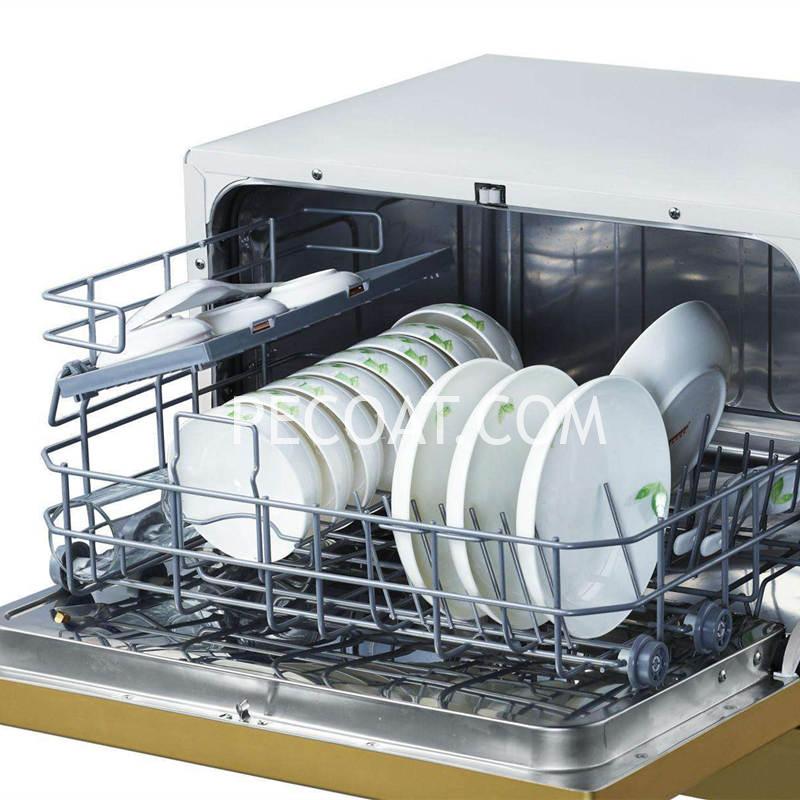
Polyamide resin, commonly known as nylon, is a widely used thermoplastic resin. Nylon has excellent comprehensive properties, high hardness, and outstanding wear resistance. The dynamic and static friction coefficients of nylon coatings are small, and they have lubricity. Therefore, they are used in textile machinery bearings, gears, valves, etc. Nylon powder coatings have good lubricity, low noise, good flexibility, excellent adhesion, chemical resistance, and solvent resistance. They can be used as an ideal wear-resistant and lubricating coating to replace copper, aluminum, cadmium, steel, etc. The density of nylon coating film is only 1/7 of copper, but its wear resistance is eight times that of copper.
Nylon powder coatings are non-toxic, odorless, and tasteless. In combination with the fact that they are not susceptible to fungal invasion or promote bacterial growth, they are successfully applied to the food processing industry to coat machine components and pipeline systems or to coat surfaces that come into direct contact with food. Due to its excellent water and saltwater resistance, it is also commonly used for coating washing machine parts, etc.
An important application area of nylon powder coatings is to coat various types of handles, not only because they have important features such as wear resistance and scratch resistance, but also because their low thermal conductivity makes the handles feel soft. This makes these materials very suitable for coating tool handles, door handles, and steering wheels.
Compared with other coatings, nylon coating films have poor chemical resistance and are not suitable for use in chemical environments such as acids and alkalis. Therefore, some epoxy resins are generally added as modifiers, which can not only improve the corrosion resistance of nylon coatings but also improve the bonding strength between the coating film and the metal substrate. Nylon powder has a high water absorption rate and is susceptible to moisture during construction and storage. Therefore, it needs to be stored under sealed conditions and should not be used for long periods under humid and hot conditions. Another aspect to note is that the plasticizing time of nylon powder is relatively short, and even a coating film that does not need plasticizing can achieve the desired effect, which is a unique feature of nylon powder.
Polyvinylidene fluoride (PVDF) powder paint
The most representative weather-resistant coating in thermoplastic powder paint is polyvinylidene fluoride (PVDF) powder coating. As the most representative weather-resistant ethylene polymer, PVDF has good mechanical and impact resistance, excellent wear resistance, outstanding flexibility and hardness, and can resist most corrosive chemicals such as acids, alkalis, and strong oxidants. Moreover, it is insoluble in the chemical solvents commonly used in the coatings industry, which is due to the F-C bonds contained in PVDF. At the same time, PVDF also meets the requirements of the FDA and can be used in food processing and can come into contact with food.
Due to its high melt viscosity, PVDF is prone to pinholes and poor metal adhesion in thin film coating, and the material price is too high. Therefore, in most cases, it is not used as the sole base material for powder coatings. Generally, about 30% of acrylic resin is added to improve these properties. If the content of acrylic resin is too high, it will affect the weather resistance of the coating film.
The gloss of PVDF coating film is relatively low, generally around 30±5%, which limits its application in surface decoration. Currently, it is mainly used as a building coating for large buildings, applied to roof panels, walls, and extruded aluminum window frames, with extremely excellent weather resistance.
Use Video
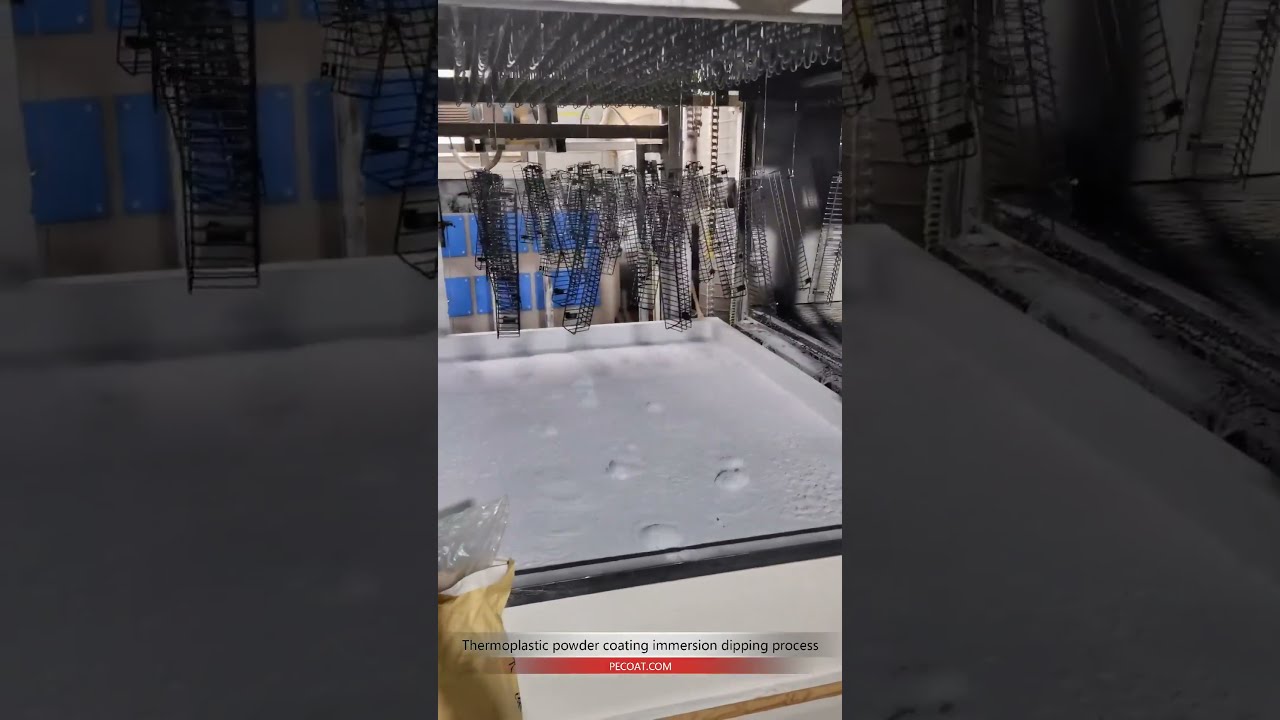
Thanks for your help and for writing this post about powder paint. It’s been great.